Method for smelting ultra-low carbon stainless steel in vacuum induction furnace
A vacuum induction furnace and ultra-low carbon technology, which is applied in the field of vacuum induction furnace smelting, can solve the problems of smelting ultra-low carbon stainless steel without a vacuum induction furnace and other problems, and achieve the effect of ensuring the decarburization effect.
- Summary
- Abstract
- Description
- Claims
- Application Information
AI Technical Summary
Problems solved by technology
Method used
Image
Examples
Embodiment 1
[0034] This embodiment adopts a vacuum induction furnace with a rated capacity of 50kg, its rated power is 140kw, and the ultimate vacuum degree is 6.67×10 -2 Pa, the chemical composition and target content of ultra-low carbon stainless steel are shown in Table 1. The smelting steps are as follows:
[0035] (1) Before smelting, bake and dry industrial pure iron, metal chromium, ferromolybdenum, iron ore, nickel plate, ferroniobium, and metal titanium at 120-180°C for 4-6 hours.
[0036] (2) Arrange 5kg of small pieces of industrial pure iron and 0.5kg of nickel plate at the bottom of the crucible, 1.25kg of ferromolybdenum with a molybdenum content of 60% is placed in the middle, and 28kg of industrial pure iron is placed in the upper part; 0.05kg of iron ore, 16kg of metal chromium, 0.02 kg of aluminum particles, 0.125kg of ferroniobium, and 0.025kg of titanium metal are put into the distribution bin.
[0037] (3) Vacuumize to 10Pa and power on, and all the raw materials in...
Embodiment 2
[0047] This embodiment adopts a vacuum induction furnace with a rated capacity of 500kg, its rated power is 400kw, and the ultimate vacuum degree is 6.67×10 -2 Pa, the chemical composition and target content of ultra-low carbon stainless steel are shown in Table 2. The smelting steps are as follows:
[0048](1) Before smelting, bake and dry industrial pure iron, metal chromium, ferromolybdenum, iron ore, nickel plate, ferroniobium, and metal titanium at 120-180°C for 4-6 hours.
[0049] (2) 50kg of small pieces of industrial pure iron and 2.5kg of nickel plate are arranged at the bottom of the crucible, 8.33kg of ferromolybdenum with a molybdenum content of 60% is placed in the middle, and 342.17kg of industrial pure iron is placed in the upper part; 0.5kg of iron ore, 98kg of metal chromium, 0.2kg of aluminum pellets, 2.08kg of ferroniobium, and 0.5kg of titanium metal are put into the distribution bin.
[0050] (3) Vacuumize to 8Pa and power on, and after 2.5 hours, all th...
Embodiment 3
[0060] In this embodiment, a vacuum induction furnace with a rated capacity of 1t is used, with a rated power of 750kw and a limit vacuum of 0.1Pa. The chemical composition and target content of ultra-low carbon stainless steel are shown in Table 3. The smelting steps are as follows:
[0061] (1) Before smelting, bake and dry industrial pure iron, metal chromium, ferromolybdenum, iron ore, nickel plate, ferroniobium, and metal titanium at 120-180°C for 4-6 hours.
[0062] (2) 200kg of small pieces of industrial pure iron and 8kg of nickel plate are arranged at the bottom of the crucible, 8.34kg of ferromolybdenum with a molybdenum content of 60% is placed in the middle, and 675.26kg of industrial pure iron is placed in the upper part; 1.5kg of iron ore, 105kg of metallic chromium, 0.6 kg of aluminum particles, 6.67kg of ferroniobium, and 1.5kg of titanium metal are put into the distribution bin.
[0063] (3) Vacuumize to 5Pa and power on, and all the raw materials in the cruc...
PUM
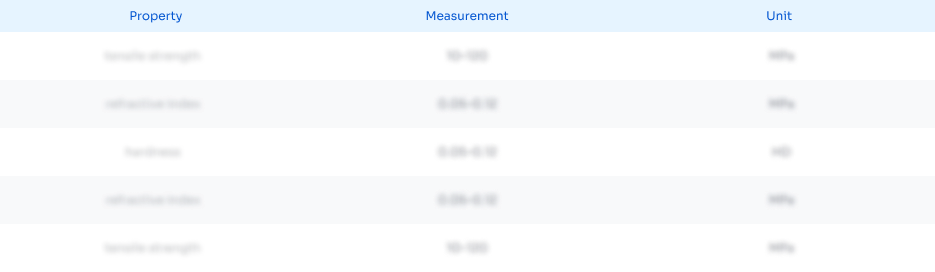
Abstract
Description
Claims
Application Information

- R&D
- Intellectual Property
- Life Sciences
- Materials
- Tech Scout
- Unparalleled Data Quality
- Higher Quality Content
- 60% Fewer Hallucinations
Browse by: Latest US Patents, China's latest patents, Technical Efficacy Thesaurus, Application Domain, Technology Topic, Popular Technical Reports.
© 2025 PatSnap. All rights reserved.Legal|Privacy policy|Modern Slavery Act Transparency Statement|Sitemap|About US| Contact US: help@patsnap.com