Method for recovering byproduct ethylbenzene in production of epoxypropane by using co-oxidation method
A technology of propylene oxide and recovery method, which is applied in the direction of chemical instruments and methods, organic chemistry, hydrocarbons, etc., can solve the problems affecting the use and takeaway of ethylbenzene, the impact of product quality, and low relative volatility, so as to increase the activity Effects of site density, difficulty in separation, and low volatility
- Summary
- Abstract
- Description
- Claims
- Application Information
AI Technical Summary
Problems solved by technology
Method used
Image
Examples
Embodiment 1
[0117] Example 1 (S1)
[0118] The acidic functionalized ionic liquid C modified by the immobilized metal complex was prepared according to the following steps:
[0119] (i) Dissolve 0.10mol 1-vinylimidazole (alkene precursor) and 0.40mol 1,3-propane sultone (sulfonating agent) in 100mL ethanol, and stir at room temperature for 0.5h to obtain a mixture; The resulting mixture was heated to 50°C and reacted for 2 hours to obtain a solid substance; then the solid substance was washed 3 times with 4 times the volume of ethanol, and dried to obtain the amphoteric precursor salt a 1 , specifically PS-VIm;
[0120] 0.20mol of the resulting amphoteric precursor salt a 1 Add it to an aqueous solution containing 0.40 mol of sulfuric acid, carry out the acidification reaction of the precursor hydrochloride, and react at 80°C for 1 hour to obtain the acidified material; then evaporate the obtained acidified material to remove the solvent-water, and obtain the acidified crude product ; ...
Embodiment 2-7
[0127] Embodiment 2-7 (S2-7)
[0128] Prepare the acidic functionalized ionic liquid C modified by the immobilized metal complex according to the method of Example 1 2 -C 7 ,in,
[0129] In step (i), the amphoteric precursor salt a 1 -a 7 The preparation conditions are as shown in table 1;
[0130] In step (i), acidification treatment prepares functionalized multi-acid site ionic liquid A 1 -A 7 The preparation conditions are as shown in table 2;
[0131] In step (ii), the functionalized multi-acid site ionic liquid b of the monodentate phosphine ligand 1 -b 7 The preparation conditions are as shown in table 3;
[0132] In step (ii), the multi-acid site ionic liquid B modified by the metal complex is introduced into the metal complex 1 -B 7 The preparation conditions are as shown in table 4;
[0133] In step (iii), the acidic functionalized ionic liquid C modified by the immobilized metal complex 1 -C 7 The preparation raw materials and preparation conditions are...
Embodiment 8
[0150] Compared with embodiment 1, only following difference:
[0151] In step (i), prepare amphoteric precursor salt a 8 When, the organic solvent used is acetone, and the detergent used is acetone;
[0152] In step (i), acidification treatment prepares functionalized multi-acid site ionic liquid A 8 When, the detergent used is dimethyl sulfoxide;
[0153] The acidic functionalized ionic liquid C modified by the immobilized metal complex was obtained 8 .
PUM
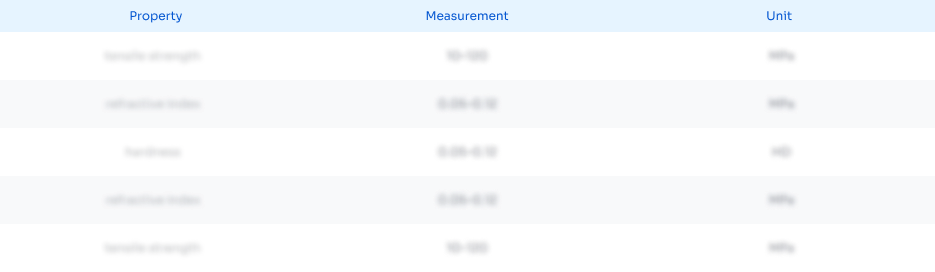
Abstract
Description
Claims
Application Information

- R&D
- Intellectual Property
- Life Sciences
- Materials
- Tech Scout
- Unparalleled Data Quality
- Higher Quality Content
- 60% Fewer Hallucinations
Browse by: Latest US Patents, China's latest patents, Technical Efficacy Thesaurus, Application Domain, Technology Topic, Popular Technical Reports.
© 2025 PatSnap. All rights reserved.Legal|Privacy policy|Modern Slavery Act Transparency Statement|Sitemap|About US| Contact US: help@patsnap.com