Preparation method of direct type backlight lens
A direct type and lens technology, which is applied in the field of direct type backlight lens preparation, can solve the problems of low light energy utilization rate of backlight lens, low energy utilization rate of LED chips, and affecting light distribution brightness, etc., to achieve sufficient and uniform illumination brightness , improve brightness, improve the effect of integration
- Summary
- Abstract
- Description
- Claims
- Application Information
AI Technical Summary
Problems solved by technology
Method used
Image
Examples
Embodiment Construction
[0024] In order to further understand the features, technical means, and specific objectives and functions achieved by the present invention, the present invention will be further described in detail below in conjunction with the accompanying drawings and specific embodiments.
[0025] refer to figure 2 .
[0026] The embodiment of the present invention discloses a method for preparing a direct-type backlight lens, which includes the following steps in sequence:
[0027] S1. The lens body is made by injection molding. The two sides of the lens body are the installation plane and the light-emitting curved surface respectively, and an inwardly recessed optical cavity is formed at the center of the installation plane;
[0028] S2. Cover each surface of the lens body with a positive photoresist to obtain a protective mask layer, and the protective mask layer covers the installation plane, the light-emitting curved surface, and the inner wall of the optical cavity;
[0029] S3. ...
PUM
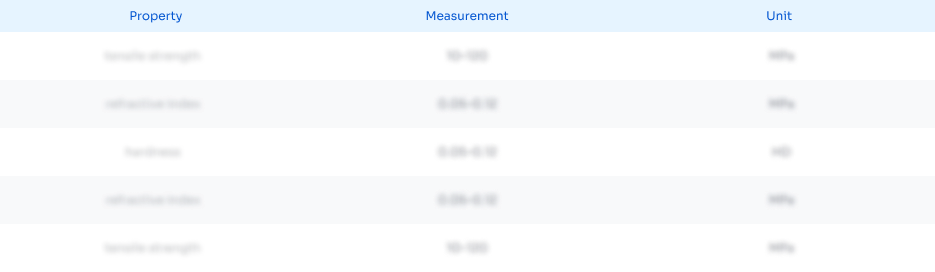
Abstract
Description
Claims
Application Information

- R&D
- Intellectual Property
- Life Sciences
- Materials
- Tech Scout
- Unparalleled Data Quality
- Higher Quality Content
- 60% Fewer Hallucinations
Browse by: Latest US Patents, China's latest patents, Technical Efficacy Thesaurus, Application Domain, Technology Topic, Popular Technical Reports.
© 2025 PatSnap. All rights reserved.Legal|Privacy policy|Modern Slavery Act Transparency Statement|Sitemap|About US| Contact US: help@patsnap.com