Method for preparing graphite-phase carbon nitride film electrode through spray thermal polymerization
A graphite phase carbon nitride, thin film electrode technology, applied in the direction of electrodes, electrolysis process, electrolysis components, etc., can solve the problems of inferior electrical conductivity as the substrate itself, reduced electron transport ability, uneven carbon nitride film, etc., to improve the electronic Conductivity, broadening the photoresponse range, reducing the effect of the band gap
- Summary
- Abstract
- Description
- Claims
- Application Information
AI Technical Summary
Problems solved by technology
Method used
Image
Examples
Embodiment 1
[0027] A method for preparing graphite phase carbon nitride film electrodes by spray thermal polymerization, the specific steps are as follows:
[0028] (1) Put dicyandiamide in a mortar and grind it into powder at room temperature, and then put it in an oven at 50°C for 24 hours to remove the moisture in dicyandiamide. 5g of dicyandiamide was dissolved in 1L of deionized water, and stirred for 100min to obtain a precursor solution;
[0029] (2) Place the electrode base FTO flat on the upper nozzle of the vertical tube furnace, adjust the exposed area of the electrode substrate FTO in the nozzle to be a square of 1cm*1cm, and cover the beaker above the nozzle to seal;
[0030] (3) Inject the precursor solution in step (1) into the ultrasonic atomizer, connect the atomization port to the lower end of the vertical tube furnace, set and wait for the temperature in the heating zone of the tube furnace to rise to 650°C;
[0031] (4) At a temperature of 650°C, turn on the ultraso...
Embodiment 2
[0035] A method for preparing graphite phase carbon nitride film electrodes by spray thermal polymerization, the specific steps are as follows:
[0036] (1) Put the urea in a mortar and grind it into powder at room temperature, then put it in an oven at 50°C for 24 hours to remove the moisture in the urea, and take 10g of the ground and dried urea while stirring Dissolve in 1L deionized water, stir for 5 minutes to obtain a precursor solution;
[0037] (2) Place the electrode base quartz glass sheet flatly on the outlet end of the horizontal tube furnace, adjust the exposed area of the electrode base quartz glass sheet in the nozzle to be a square of 5cm*5cm, and cover the beaker on the nozzle to seal;
[0038] (3) Inject the precursor solution in step (1) into the mesh atomizer, connect the atomization port to the inlet end of the horizontal tube furnace, set and wait for the temperature in the heating zone of the tube furnace to rise to 800°C;
[0039] (4) At a temperatur...
Embodiment 3
[0042] A method for preparing graphite phase carbon nitride film electrodes by spray thermal polymerization, the specific steps are as follows:
[0043] (1) Put melamine in a mortar and grind it fully into powder at room temperature, and then put it in an oven at 50°C for 24 hours to remove the moisture in melamine. Under the condition of stirring, take 0.1 g was dissolved in 1L deionized water, and stirred for 100 minutes to obtain a precursor solution;
[0044] (2) Place the electrode base FTO flatly on the upper nozzle of the vertical tube furnace, adjust the exposed area of the electrode substrate FTO at the nozzle to be a square of 2cm*2cm, and cover the beaker above the nozzle to seal;
[0045] (3) Inject the precursor solution in step (1) into the compression atomizer, connect the atomization port to the lower end of the vertical tube furnace, set and wait for the temperature in the heating zone of the tube furnace to rise to 550°C;
[0046] (4) At a temperature of 5...
PUM
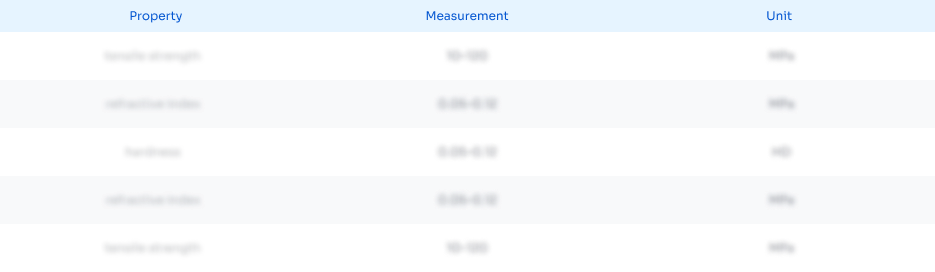
Abstract
Description
Claims
Application Information

- R&D
- Intellectual Property
- Life Sciences
- Materials
- Tech Scout
- Unparalleled Data Quality
- Higher Quality Content
- 60% Fewer Hallucinations
Browse by: Latest US Patents, China's latest patents, Technical Efficacy Thesaurus, Application Domain, Technology Topic, Popular Technical Reports.
© 2025 PatSnap. All rights reserved.Legal|Privacy policy|Modern Slavery Act Transparency Statement|Sitemap|About US| Contact US: help@patsnap.com