Anti-rust treatment method for iron-based alloy magnetic powder core
An iron-based alloy, anti-rust treatment technology, applied in the direction of preventing/reducing unwanted electric/magnetic effects, magnetic objects, magnetic materials, etc., can solve the problem of long-term and comprehensive anti-rust and silane couple The joint agent anti-rust process damages the magnetic properties of the powder core, and the cost of the spray paint anti-rust process is high, so as to achieve the effects of significantly worsening the loss, increasing the breaking strength, and improving the mechanical strength
- Summary
- Abstract
- Description
- Claims
- Application Information
AI Technical Summary
Problems solved by technology
Method used
Image
Examples
Embodiment 1
[0024] The antirust treatment operation steps of an iron-based alloy magnetic powder core are as follows:
[0025] (1) Take 500g of insulated aerosolized iron-silicon-aluminum alloy powder, put it into 5kg of anti-rust solution for soaking, soaking time is 20 minutes; drying, drying temperature is 60 ℃, drying time is 60 minutes , to obtain rust-proof iron-based alloy powder.
[0026] The anti-rust liquid is prepared by uniformly mixing acrylic emulsion, epoxy acrylate resin and lauryl alcohol fat at a volume ratio of 1:1:3.
[0027] (2) Evenly mix 500g of anti-rust iron-based alloy powder with 0.5g of mold release agent, and press it into a green body with a forming pressure of 1600 MPa.
[0028] (3) Put the green body into the anti-rust solution for a second immersion, and the immersion time is 60 minutes. Dry the surface of the green body at 60°C, and then bake at a low temperature at 130°C for 30 minutes to obtain the soaked green body.
[0029] The anti-rust liquid use...
Embodiment 2
[0033] The antirust treatment operation steps of an iron-based alloy magnetic powder core are as follows:
[0034] (1) Take 500g of insulated ball-milled crushed iron-silicon-aluminum alloy powder, soak it in 5kg anti-rust solution for 60 minutes, and dry it at 120°C for 70 minutes. The rust-proof ball-milled and crushed iron-silicon-aluminum alloy powder is obtained.
[0035] The anti-rust solution is prepared by uniformly mixing acrylic emulsion, epoxy acrylate resin and dodecyl alcohol fat at a volume ratio of 1:1:10.
[0036] (2) Evenly mix 500g of anti-rust ball milled sendust aluminum alloy powder with 2.5g of mold release agent, and press it into a green body with a forming pressure of 1900 MPa.
[0037] (3) Put the green body into the anti-rust solution for a second immersion, and the immersion time is 120min. Dry the surface of the green body at 70°C, and then bake at a low temperature at 200°C for 60 minutes to obtain the soaked green body.
[0038] The anti-rust ...
Embodiment 3
[0043] The antirust treatment operation steps of an iron-based alloy magnetic powder core are as follows:
[0044] (1) Take 500g of insulated aerosolized iron-silicon alloy powder, put it into 5kg of anti-rust solution for soaking, soaking time is 80 minutes; drying, drying temperature is 160 ℃, drying time is 80 minutes, The anti-rust gas atomized iron-silicon alloy powder is obtained.
[0045] The anti-rust liquid is made by uniformly mixing acrylic emulsion, epoxy acrylate resin and lauryl alcohol fat at a volume ratio of 1:1:18.
[0046] (2) Evenly mix 500g of anti-rust gas atomized iron-silicon alloy powder with 5g of release agent, and press it into a green body with a forming pressure of 2500 MPa.
[0047] (3) Put the green body into the anti-rust solution for secondary soaking, and the soaking time is 180min. The surface of the green body was dried at 80°C, and then baked at a low temperature at 300°C for 100 minutes to obtain the soaked green body.
[0048] The ant...
PUM
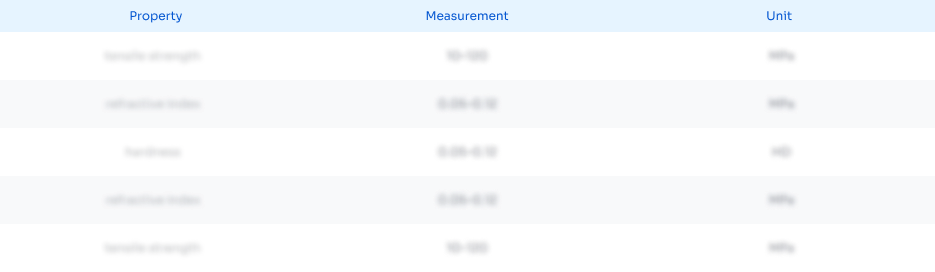
Abstract
Description
Claims
Application Information

- R&D Engineer
- R&D Manager
- IP Professional
- Industry Leading Data Capabilities
- Powerful AI technology
- Patent DNA Extraction
Browse by: Latest US Patents, China's latest patents, Technical Efficacy Thesaurus, Application Domain, Technology Topic, Popular Technical Reports.
© 2024 PatSnap. All rights reserved.Legal|Privacy policy|Modern Slavery Act Transparency Statement|Sitemap|About US| Contact US: help@patsnap.com