Method for removing hydrogen sulfide, hydrogen phosphide and arsenic hydride by using low-temperature plasma modified alumina-based catalyst
A low-temperature plasma, alumina-based technology, used in catalyst activation/preparation, metal/metal oxide/metal hydroxide catalysts, physical/chemical process catalysts, etc. , secondary pollution of the environment, etc., to achieve the effect of improving physical and chemical properties, good thermal stability and adsorption, and high commercial value
- Summary
- Abstract
- Description
- Claims
- Application Information
AI Technical Summary
Problems solved by technology
Method used
Image
Examples
Embodiment 1
[0029] Embodiment 1: The method for removing hydrogen sulfide, phosphine and arsine by this low-temperature plasma modified alumina-based catalyst is as follows:
[0030] (1) Immerse the alumina particles in a beaker filled with ultrapure water, pre-treat with ultrasonic at 20 Hz for 3 hours to remove dust and impurities on the surface of the sample, and then dry them in an oven at 120°C for 13 hours;
[0031](2) Grind the alumina particles into a powder below 200 meshes, weigh 3g of the alumina powder into the copper nitrate solution (the amount of copper in the copper nitrate solution is 30% of the mass of the alumina particles) and put it into a rotary evaporator In the instrument, use a rotary evaporator to rotate at a speed of 80r / min for 20min, take it out and put it in an oven to dry at 120°C for 12h;
[0032] (3) Calcinate the alumina-based catalyst loaded with copper nitrate in a microwave muffle furnace at 400°C for 3 hours, then press into tablets, grind and sieve t...
Embodiment 2
[0033] Embodiment 2: The method for removing hydrogen sulfide, phosphine and arsine by this low-temperature plasma modified alumina-based catalyst is as follows:
[0034] (1) Immerse the alumina particles in a beaker filled with ultrapure water, pre-treat with ultrasonic at 20 Hz for 3 hours to remove dust and impurities on the surface of the sample, and then dry them in an oven at 120°C for 13 hours;
[0035] (2) Grind the alumina particles into a powder below 200 meshes, weigh 3g of the alumina powder into the copper nitrate solution (the amount of copper in the copper nitrate solution is 30% of the mass of the alumina particles) and put it into a rotary evaporator In the instrument, use a rotary evaporator to rotate at a speed of 80r / min for 20min, take it out and put it in an oven to dry at 120°C for 12h;
[0036] (3) Calcinate the alumina-based catalyst loaded with copper nitrate in a microwave muffle furnace at 300°C for 4 hours, then press into tablets, grind and sieve ...
Embodiment 3
[0038] Embodiment 3: The method for removing hydrogen sulfide, phosphine and arsine by this low-temperature plasma modified alumina-based catalyst is as follows:
[0039] (1) Immerse the alumina particles in a beaker filled with ultrapure water, pre-treat with ultrasonic at 25Hz for 2.5h to remove dust and impurities on the surface of the sample, and then dry in an oven at 100°C for 13h;
[0040] (2) Grind the alumina particles into a powder below 200 meshes, weigh 3g of alumina powder and dip it into the copper nitrate solution (the amount of copper in the copper nitrate solution is 25% of the mass of the alumina particles) and put it into a rotary evaporator , use a rotary evaporator to rotate at a speed of 80r / min for 30min, take it out and dry it in an oven at 100°C for 15h;
[0041] (3) Calcinate the alumina-based catalyst loaded with copper nitrate in a microwave muffle furnace at 400°C for 3 hours, then press into tablets, grind and sieve to 40-60 mesh;
[0042] (4) Pl...
PUM
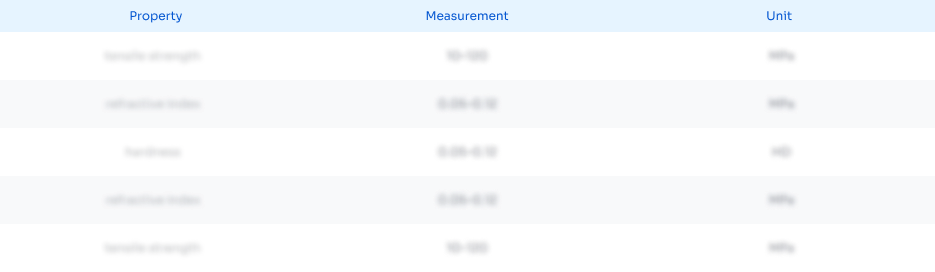
Abstract
Description
Claims
Application Information

- R&D
- Intellectual Property
- Life Sciences
- Materials
- Tech Scout
- Unparalleled Data Quality
- Higher Quality Content
- 60% Fewer Hallucinations
Browse by: Latest US Patents, China's latest patents, Technical Efficacy Thesaurus, Application Domain, Technology Topic, Popular Technical Reports.
© 2025 PatSnap. All rights reserved.Legal|Privacy policy|Modern Slavery Act Transparency Statement|Sitemap|About US| Contact US: help@patsnap.com