Antistatic power protection tube and preparation method thereof
A power protection and anti-static technology, applied in the field of anti-static power protection tube and its preparation, can solve the problems of stress concentration, poor compatibility, reduced mechanical properties and processing performance of the power protection tube, etc., to achieve compatibility Good properties, good antistatic ability, the effect of maintaining mechanical properties and processability
- Summary
- Abstract
- Description
- Claims
- Application Information
AI Technical Summary
Problems solved by technology
Method used
Image
Examples
Embodiment 1
[0038] Prepare the modifier:
[0039] Step S11, mix o-phenylenediamine and solvent, add phosphorus oxychloride at a temperature of 20°C, and after the dropwise addition, raise the temperature to 50°C for reflux reaction for 4 hours, and carry out post-treatment after the reaction; post-treatment The process is as follows: the reaction solution is cooled to room temperature, then washed with acetonitrile, and then vacuum-dried at 60°C to constant weight to obtain intermediate 1;
[0040] Step S12, mix p-hydroxybenzaldehyde, dichloromethane and triethylamine, stir and cool down to 0°C under the condition of nitrogen protection, slowly add the dichloromethane solution of intermediate 1 dropwise, after the dropwise addition, keep the temperature No change, monitor the reaction with a TLC plate during the reaction, and carry out post-treatment after the reaction; the post-treatment process is: the obtained reaction solution is washed with deionized water, 5% sodium hydroxide soluti...
Embodiment 2
[0046] Preparation of modified graphene:
[0047] Put graphite oxide into N,N-dimethylformamide, ultrasonically disperse to obtain a dispersion liquid, add a modifier, react for 24 hours under nitrogen protection, then adjust the pH value to 9 with ammonia water, and raise the temperature to 95°C , and then add hydrazine hydrate to react for 1.5h, after the reaction, post-treatment is carried out; the post-treatment process is: the obtained reaction solution is centrifugally washed 3 times with N,N-dimethylformamide, and modified graphene is obtained after washing. .
[0048] Wherein, the dosage ratio of graphite oxide, N,N-dimethylformamide, modifier and hydrazine hydrate is 0.5g:200mL:5g:0.5g, and the modifier is prepared in Example 1.
Embodiment 3
[0050] Preparation of modified graphene:
[0051] Put graphite oxide into N,N-dimethylformamide, ultrasonically disperse to obtain a dispersion liquid, add a modifier, react for 24 hours under nitrogen protection, then adjust the pH value to 9 with ammonia water, and raise the temperature to 95°C , and then add hydrazine hydrate to react for 1.6h, after the reaction, post-treatment is carried out; the process of post-treatment is: the obtained reaction solution is centrifugally washed 3 times with N,N-dimethylformamide, and modified graphene is obtained after washing .
[0052] Wherein, the dosage ratio of graphite oxide, N,N-dimethylformamide, modifier and hydrazine hydrate is 0.5g:200mL:5g:0.5g, and the modifier is prepared in Example 1.
PUM
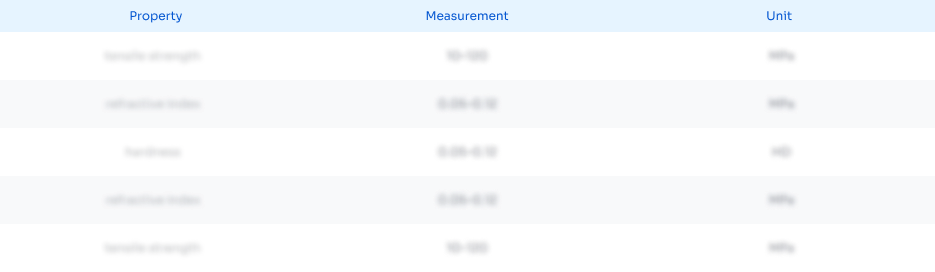
Abstract
Description
Claims
Application Information

- R&D Engineer
- R&D Manager
- IP Professional
- Industry Leading Data Capabilities
- Powerful AI technology
- Patent DNA Extraction
Browse by: Latest US Patents, China's latest patents, Technical Efficacy Thesaurus, Application Domain, Technology Topic, Popular Technical Reports.
© 2024 PatSnap. All rights reserved.Legal|Privacy policy|Modern Slavery Act Transparency Statement|Sitemap|About US| Contact US: help@patsnap.com