High-strength wear-resistant closed steel frame and machining process thereof
A processing technology and steel frame technology, applied in metal material coating technology, liquid chemical plating, cleaning methods and utensils, etc., can solve problems such as unsatisfactory wear resistance, complicated process steps, and easy peeling of coatings, etc., to achieve Improved comprehensive wear resistance, reasonable process design, and excellent wear resistance
- Summary
- Abstract
- Description
- Claims
- Application Information
AI Technical Summary
Problems solved by technology
Method used
Image
Examples
Embodiment 1
[0032] A process for processing a high-strength wear-resistant closed steel frame, comprising the following steps:
[0033] (1) The preparation steps of porous tungsten carbide are: take aminonitrile and mesoporous molecular sieve, stir and mix for 10 minutes, place in a 50°C water bath for constant temperature heating, vacuumize and constant temperature for 4 hours, centrifuge, vacuum dry, and transfer to argon after drying In the atmosphere, calcined at 530°C for 4 hours, acid etched for 18 hours after calcination, separated and dried to obtain material A;
[0034] Take material A, tungsten hexachloride and ethanol, stir and mix for 10 minutes, transfer to a nitrogen atmosphere after drying, and perform high-temperature calcination. During calcination, first raise the temperature to 680°C, and calcine at a constant temperature for 15 minutes, then raise the temperature to 4°C / min. Calcined at 940°C for 2.5 hours to obtain porous tungsten carbide.
[0035] (2) Take porous tu...
Embodiment 2
[0042] A process for processing a high-strength wear-resistant closed steel frame, comprising the following steps:
[0043] (1) The preparation steps of porous tungsten carbide are as follows: take aminonitrile and mesoporous molecular sieve, stir and mix for 15 minutes, place in a water bath at 52°C for constant temperature heating, vacuum and constant temperature treatment for 3.5 hours, centrifugal separation, vacuum drying, and transfer to argon after drying Calcined at 540°C for 3.5 hours in air atmosphere, acid etched for 19 hours after calcination, separated and dried to obtain material A;
[0044] Take material A, tungsten hexachloride and ethanol, stir and mix for 16 minutes, transfer to a nitrogen atmosphere after drying, and perform high-temperature calcination. During calcination, first raise the temperature to 685°C, and then calcine at a constant temperature for 13 minutes, then raise the temperature to Calcined at 945°C for 2.2 hours to obtain porous tungsten ca...
Embodiment 3
[0052] A process for processing a high-strength wear-resistant closed steel frame, comprising the following steps:
[0053] (1) The preparation steps of porous tungsten carbide are: take aminonitrile and mesoporous molecular sieve, stir and mix for 20 minutes, place in a water bath at 55°C for constant temperature heating, vacuumize and constant temperature for 3 hours, centrifuge, vacuum dry, and transfer to argon after drying Calcined at 550°C for 3 hours in the atmosphere, etched for 20 hours after calcination, separated and dried to obtain material A;
[0054] Take material A, tungsten hexachloride and ethanol, stir and mix for 20 minutes, transfer to a nitrogen atmosphere after drying, and perform high-temperature calcination. During calcination, first raise the temperature to 690°C, and calcine at a constant temperature for 10 minutes, then raise the temperature to 5°C / min. Calcined at 950°C for 2 hours to obtain porous tungsten carbide.
[0055] (2) Take porous tungste...
PUM
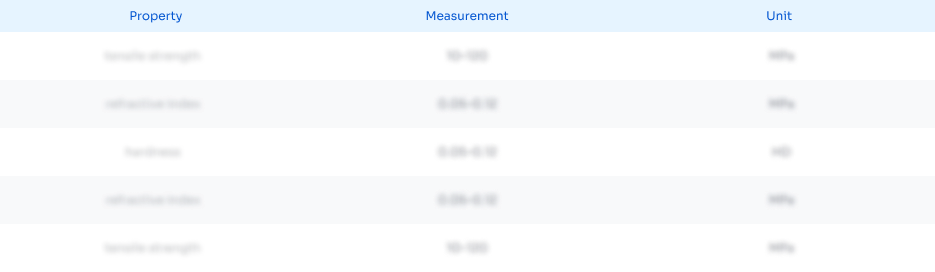
Abstract
Description
Claims
Application Information

- R&D Engineer
- R&D Manager
- IP Professional
- Industry Leading Data Capabilities
- Powerful AI technology
- Patent DNA Extraction
Browse by: Latest US Patents, China's latest patents, Technical Efficacy Thesaurus, Application Domain, Technology Topic, Popular Technical Reports.
© 2024 PatSnap. All rights reserved.Legal|Privacy policy|Modern Slavery Act Transparency Statement|Sitemap|About US| Contact US: help@patsnap.com