Solid waste regenerated foamed ceramic material for thermal insulation wall and preparation method
A foam ceramic, thermal insulation technology, applied in the field of solid waste recycled foam ceramic material preparation, can solve the problems of high water absorption, domestic utilization rate of less than 10%, and reduced structural durability
- Summary
- Abstract
- Description
- Claims
- Application Information
AI Technical Summary
Problems solved by technology
Method used
Image
Examples
preparation example Construction
[0030] A method for preparing a solid waste regenerated foam ceramic material for thermal insulation walls, comprising the following steps:
[0031] 1) Purification and optimization of solid waste materials: industrial waste (fly ash, coal gangue, polishing slag, blast furnace slag, cinder, steel slag, red mud, copper tailings, iron tailings, gold tailings, granite tailings) and construction Waste (slag, waste concrete, waste ceramic glass, brick fragments, mud, waste mortar) solid waste contains a large amount of active ingredients, such as alumina, silica, silicate, calcium salt, iron oxide, etc. It also contains a large amount of organic matter and harmful substances. First, manually sort and screen to remove large pieces of plastic, wood, metal and other debris in solid waste. The solid waste is then sintered in flowing oxygen (sintering temperature 500-600°C) to remove carbon impurities. Subsequently, the solid waste is pulverized and sieved (4-10 meshes in sieve apertu...
Embodiment 1
[0037] A method for preparing a solid waste regenerated foam ceramic material for thermal insulation walls, comprising the following steps:
[0038]1) Purification and optimization of solid waste materials: manual classification and screening to remove large pieces of plastic, wood, metal and other debris in the cinder. The solid waste is then sintered in flowing oxygen at a temperature of 500°C to remove carbon impurities. Subsequently, the coal cinder is pulverized and sieved, the sieve hole diameter is 4 mesh, and the fine grain obtained by removing large particles is obtained. The refined pellets are washed with water to remove the dissolved harmful impurities in the material and purify the raw materials. Finally, ball mill the purified raw material with water for 20 minutes (solid:water=1:1) to obtain a precursor slurry uniformly dispersed in the solution.
[0039] 2) Preparation of foaming slurry: add 5% hydrogen peroxide, 40% cement, and 5% polyacrylamide to the precu...
Embodiment 2
[0043] A method for preparing a solid waste regenerated foam ceramic material for thermal insulation walls, comprising the following steps:
[0044] 1) Purification and optimization of solid waste materials: First, manually sort and screen to remove large pieces of plastic, wood, metal and other debris in waste concrete. The waste concrete is then sintered in flowing oxygen (550°C sintering temperature) to remove carbon impurities. Subsequently, the waste concrete is pulverized and sieved (the sieve aperture is 8 mesh) to remove the fine grains obtained from the large grains. The refined pellets are washed with water to remove the dissolved harmful impurities in the material and purify the raw materials. Finally, ball mill the purified raw material with water for 230 minutes (solid:water=1.5:1) to obtain a precursor slurry uniformly dispersed in the solution.
[0045] 2. Preparation of foaming slurry: add 10% sodium bicarbonate by mass ratio, 40% gypsum by mass ratio, and so...
PUM
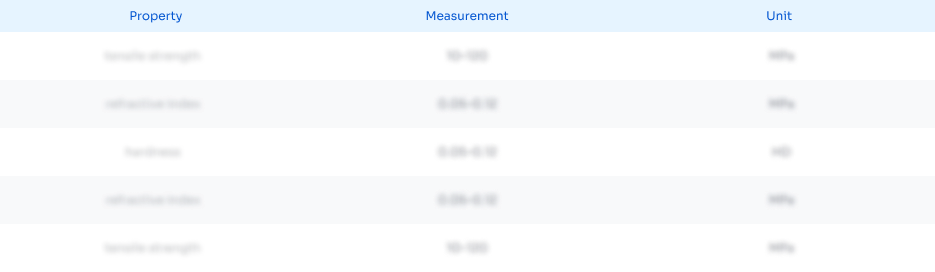
Abstract
Description
Claims
Application Information

- R&D
- Intellectual Property
- Life Sciences
- Materials
- Tech Scout
- Unparalleled Data Quality
- Higher Quality Content
- 60% Fewer Hallucinations
Browse by: Latest US Patents, China's latest patents, Technical Efficacy Thesaurus, Application Domain, Technology Topic, Popular Technical Reports.
© 2025 PatSnap. All rights reserved.Legal|Privacy policy|Modern Slavery Act Transparency Statement|Sitemap|About US| Contact US: help@patsnap.com