Method for cleaner production of sodium vanadate and sodium chromate by pressure leaching of vanadium slag
A sodium vanadate, sodium chromate, clean production technology, applied in chemical instruments and methods, chromate/dichromate, vanadium compounds, etc., can solve the problem of inability to achieve co-extraction of vanadium and chromium, reduce roasting holding time, pollution environmental issues
- Summary
- Abstract
- Description
- Claims
- Application Information
AI Technical Summary
Problems solved by technology
Method used
Image
Examples
Embodiment 1
[0064] (1) Ingredients: In the autoclave, add vanadium slag and 30wt% NaOH solution, wherein the vanadium slag contains V 2 o 5 8.3wt%, Cr 2 O 33.41%, the mass ratio of alkali ore is 10:1;
[0065](2) Reaction: the material prepared in step (1) is heated to 350°C, then 1MPa oxygen is introduced into the solution, and stirred to make the vanadium slag fully contact with oxygen, and the total pressure of the control system is 8MPa (at a certain temperature and alkali concentration The vapor pressure of the lower NaOH solution can be checked by the chlor-alkali industry handbook), and the heat preservation reaction is 10h, so that the vanadium slag and oxygen fully react, and finally obtain the solution containing NaOH, Na 3 VO 4 、Na 2 CrO 4 、Na 2 SiO 4 and other solutions, iron-rich tailings, and the conversion rates of vanadium and chromium in vanadium slag are 99.4% and 99.0% respectively;
[0066] (3) Dilution: add water to the slurry obtained in step (2) and dilute t...
Embodiment 2
[0073] (1) Ingredients: In the autoclave, add vanadium slag and 60wt% NaOH solution, wherein the vanadium slag contains V 2 o 5 11.3wt%, Cr 2 o 3 4.41%, the mass ratio of alkali ore is 4:1;
[0074] (2) Reaction: Heat the material prepared in step (1) to 260°C, then feed 2MPa oxygen into the solution, and stir to make the vanadium slag fully contact with oxygen, control the total pressure of the system to 3MPa, and heat the reaction for 8h to make The vanadium slag fully reacts with oxygen, and finally gets NaOH, Na 3 VO 4 、Na 2 CrO 4 、Na 2 SiO 4 and other solutions, sodium chromate crystals and iron-rich tailings, and the conversion rates of vanadium and chromium in vanadium slag are 99.5% and 99.1% respectively;
[0075] (3) Dilution: Add 1 washing liquid to the slurry obtained in step (2), and dilute to NaOH concentration of 220g / L;
[0076] (4) Solid-liquid separation: filter and separate the diluted slurry obtained in step (3) at 100° C. to obtain eluate and i...
Embodiment 3
[0082] (1) Ingredients: In the autoclave, add vanadium slag and 75wt% NaOH solution, wherein the vanadium slag contains V 2 o 5 15.3wt%, Cr 2 o 3 6.51%, the mass ratio of alkali ore is 2:1;
[0083] (2) Reaction: Heat the material prepared in step (1) to 200°C, then pass 1.5MPa oxygen-enriched air into the solution, and stir to make the vanadium slag fully contact with oxygen, control the total pressure of the system to 1.5MPa, keep warm React for 1h to fully react the vanadium slag with oxygen, and finally get NaOH, Na 3 VO 4 、Na 2 CrO 4 、Na 2 SiO 4 and other solutions, sodium chromate crystals and iron-rich tailings, and the conversion rates of vanadium and chromium in vanadium slag are 99.4% and 99.3% respectively;
[0084] (3) Dilution: add steam condensed water to step (2) gained slurry and dilute to NaOH concentration 300g / L;
[0085] (4) Solid-liquid separation: filter and separate the diluted slurry obtained in step (3) at 130° C. to obtain eluate and iron-...
PUM
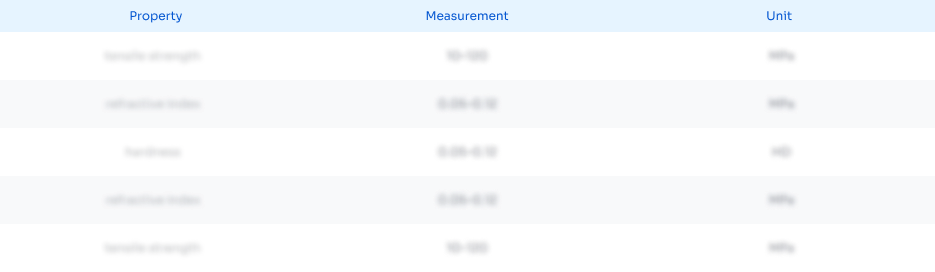
Abstract
Description
Claims
Application Information

- R&D
- Intellectual Property
- Life Sciences
- Materials
- Tech Scout
- Unparalleled Data Quality
- Higher Quality Content
- 60% Fewer Hallucinations
Browse by: Latest US Patents, China's latest patents, Technical Efficacy Thesaurus, Application Domain, Technology Topic, Popular Technical Reports.
© 2025 PatSnap. All rights reserved.Legal|Privacy policy|Modern Slavery Act Transparency Statement|Sitemap|About US| Contact US: help@patsnap.com