Heavy metal recovery method and sulfide precipitation method for magnesium-containing wastewater
A recycling method and sulfide precipitation technology, applied in chemical instruments and methods, flocculation/sedimentation water/sewage treatment, water pollutants, etc., can solve problems such as only stacking treatment, high magnesium-containing impurities, and no resource value. Achieve the effect of increasing resource recycling rate, reducing magnesium-containing impurities and avoiding overreaction
- Summary
- Abstract
- Description
- Claims
- Application Information
AI Technical Summary
Problems solved by technology
Method used
Image
Examples
Embodiment 1
[0050] The magnesium-containing wastewater used in this embodiment is cobalt smelting high-magnesium wastewater, wherein the main components are: Co 2+ : 2.3g / L, Ni 2+ : 0.67g / L, Mg 2+ : 45.7g / L, Cu 2+ : 0.0002g / L. Take 5L of raw high-magnesium wastewater, place it in an experimental container, heat it to 50°C, and adjust the pH to 3.6 with 32% liquid caustic soda; add sodium sulfide and sulfur that can provide sulfide ions that are 1.2 times the total molar amount of cobalt-nickel metal in the wastewater Sodium sulfide, the molar ratio of sodium sulfide and sodium thiosulfate is 10:1, the terminal potential is controlled at -63mV, and the reaction time is 1h; after the sulfide precipitation is completed, add 20% dilute sulfuric acid to adjust the pH to 7.6; then filter Separate, and add pure water to the filter residue with a liquid-solid ratio of 4:1 to rinse until the concentration of magnesium ions in circulating water that is 4 times the mass of the precipitate is not ...
Embodiment 2
[0052] The magnesium-containing wastewater used in this embodiment is cobalt smelting high-magnesium wastewater, wherein the main components are: Co 2+ : 2.8g / L, Ni 2+ : 1.5g / L, Mg 2+ : 47.3g / L, Cu 2+ : 0.00023g / L. Take 5L of raw high-magnesium wastewater, place it in an experimental container, heat it to 50°C, and adjust the pH to 3.6 with 32% liquid caustic soda; add sodium sulfide and sulfur that can provide sulfide ions that are 1.4 times the total molar amount of cobalt-nickel metal in the wastewater Sodium sulfide, the molar ratio of sodium sulfide and sodium thiosulfate is 12:1, the terminal potential is controlled at -78mV, and the reaction time is 1h; after the sulfide precipitation is completed, add 20% dilute sulfuric acid to adjust the pH to 7.8; then filter Separate, and add pure water to the filter residue with a liquid-solid ratio of 4:1 to rinse until the concentration of magnesium ions in circulating water that is 4 times the mass of the precipitate is not ...
Embodiment 3
[0054] The magnesium-containing wastewater used in this embodiment is cobalt smelting high-magnesium wastewater, wherein the main components are: Co 2+ : 0.91g / L, Ni 2+ : 1.12g / L, Mg 2+ : 45.32g / L, Cu 2+ : 0.00016g / L. Take 5L of raw high-magnesium wastewater, place it in an experimental container, heat it to 50°C, and adjust the pH to 4.0 with 32% liquid caustic soda; add sodium sulfide and sulfur that can provide sulfide ions that are 1.2 times the total molar amount of cobalt-nickel metal in the wastewater Sodium sulfide, the molar ratio of sodium sulfide and sodium thiosulfate is 6:1, the terminal potential is controlled at -98mV, and the reaction time is 1h; after the sulfide precipitation is completed, add 20% dilute sulfuric acid to adjust the pH to 7.0; then filter Separate, and add pure water to the filter residue with a liquid-solid ratio of 4:1 to rinse until the concentration of magnesium ions in circulating water that is 4 times the mass of the precipitate is no...
PUM
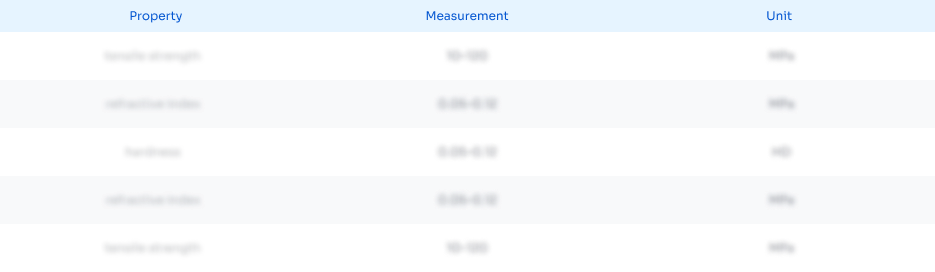
Abstract
Description
Claims
Application Information

- R&D
- Intellectual Property
- Life Sciences
- Materials
- Tech Scout
- Unparalleled Data Quality
- Higher Quality Content
- 60% Fewer Hallucinations
Browse by: Latest US Patents, China's latest patents, Technical Efficacy Thesaurus, Application Domain, Technology Topic, Popular Technical Reports.
© 2025 PatSnap. All rights reserved.Legal|Privacy policy|Modern Slavery Act Transparency Statement|Sitemap|About US| Contact US: help@patsnap.com