Catalyst for preparing low-carbon olefin through hydrogenation and preparation method thereof
A low-carbon olefin and catalyst technology, which is applied in the field of hydrogenation to low-carbon olefin catalyst and its preparation, can solve the problem of high selectivity of methane, and achieve the effects of simple preparation method, promotion of product diffusion, and reduction of carbon deposition and deactivation.
- Summary
- Abstract
- Description
- Claims
- Application Information
AI Technical Summary
Problems solved by technology
Method used
Examples
Embodiment 1
[0021] Weigh 8.8g of lanthanum nitrate, 15.3g of ferric nitrate and 10.5g of manganese nitrate, dissolve them in distilled water, then add 23.28g of citric acid, after dissolving in distilled water, mechanically stir in a water bath with a water bath temperature of 80°C and a stirring speed of 500r / min. After stirring to a gel state, dry at 100°C for 12 hours. Grind 5g of the dried powder and 10g of melamine thoroughly, put it into a muffle furnace, and bake it for 4h at a temperature of 750°C and a heating rate of 2.5°C / min. After cooling to room temperature, powder A is obtained through thorough grinding. Take 6 g of powder A in a beaker, add 200 mL of 1 mol / L hydrogen peroxide, stir magnetically for 2 h, and then filter and dry to obtain powder B. Take 3 g of powder B and place it in a reaction kettle, add 250 mL of ammonia water with a mass fraction of 2.5 wt%, stir it magnetically for 2 h, put it in an oven, react at 150 °C for 3 h, and then take it out and dry it by suct...
Embodiment 2
[0023]Weigh 8.8g of lanthanum nitrate and 10.5g of manganese nitrate, dissolve them in distilled water, then add 23.28g of citric acid, after dissolving in distilled water, mechanically stir in a water bath, the temperature of the water bath is 80°C, and the stirring speed is 500r / min. After stirring to gel state, dry at 100°C for 12h. Fully grind the dried powder with an equal mass of melamine, roast for 4 hours at a temperature of 600°C and a heating rate of 5°C / min, cool to room temperature, and grind thoroughly to obtain powder A. Take 5 g of powder A in a beaker, add 50 mL of 2 mol / L hydrogen peroxide, stir magnetically for 2 hours, and then filter and dry to obtain powder B. Take 3 g of powder B in a reaction kettle, add 100 mL of ammonia water with a mass fraction of 3 wt%, magnetically stir it for 2 h, put it in an oven, react at 180 °C for 3 h, take it out and dry it with suction to obtain powder C; Take 0.5 g of powder B, 2 g of powder C, and mechanically mix to obt...
Embodiment 3
[0025] Weigh 5.29g of strontium nitrate, 7.27g of cobalt nitrate, and 10.1g of ferric nitrate, dissolve them in distilled water, then add 19.21g of citric acid, after dissolving in distilled water, mechanically stir in a water bath with a water bath temperature of 80°C and a stirring speed of 500r / min. After stirring to a gel state, dry at 100°C for 12 hours. Grind the dried powder with an equal mass of melamine fully, put it into a muffle furnace, and roast it for 6 hours at a temperature of 700°C with a heating rate of 2°C / min. After cooling down to room temperature, it is fully ground to obtain powder A. Take 5 g of powder A in a beaker, add 100 mL of 5 mol / L hydrogen peroxide, stir for 3 hours, and then filter and dry to obtain powder B. Take 5 g of powder B and place it in a reaction kettle, add 50 mL of ammonia water with a mass fraction of 20 wt%, stir it magnetically for 2 h, put it in an oven, react at 200 °C for 5 h, and then take it out and dry it with suction to ob...
PUM
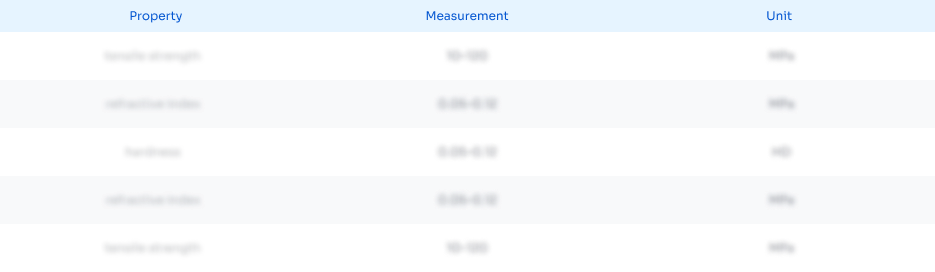
Abstract
Description
Claims
Application Information

- R&D
- Intellectual Property
- Life Sciences
- Materials
- Tech Scout
- Unparalleled Data Quality
- Higher Quality Content
- 60% Fewer Hallucinations
Browse by: Latest US Patents, China's latest patents, Technical Efficacy Thesaurus, Application Domain, Technology Topic, Popular Technical Reports.
© 2025 PatSnap. All rights reserved.Legal|Privacy policy|Modern Slavery Act Transparency Statement|Sitemap|About US| Contact US: help@patsnap.com