An intumescent coating for steel structures
An expansion type, steel structure technology, applied in fireproof coatings, epoxy resin coatings, coatings, etc., can solve problems such as loss of cohesion of the charcoal layer, loss of steel structure protection, cracking of the charcoal layer, etc., to achieve stability of the steel structure The effect of reducing resistance, avoiding cracking, and enhancing flame retardancy
- Summary
- Abstract
- Description
- Claims
- Application Information
AI Technical Summary
Problems solved by technology
Method used
Image
Examples
preparation example Construction
[0025] 1. Preparation of borosilicate resin:
[0026] The preparation method of borosilicate resin among the present invention comprises the following steps:
[0027] Step 1, phenyltriethoxysilane and dimethyldiethoxysilane are mixed in a mass molar ratio of 1:1 to obtain a mixed silane monomer, and then the mixed silane monomer and boric acid are mixed in a mass molar ratio of 2:1 was mixed to obtain mixture 1.
[0028] Step 2. On the basis of step 1, add 100ml of absolute ethanol to mixture 1 for mixing, and then add hydrochloric acid and deionized water with a molar concentration of 1mol / L on the basis of mixing mixture 1 and absolute ethanol , and finally hydrolyzed at 60°C for 3h. Wherein, the volume of hydrochloric acid is 5% of the volume of the mixed silane monomer, and the deionized water is 60% of the water required for the complete hydrolysis of the mixed silane monomer.
[0029] Step 3. On the basis of step 2, continue to heat up to 130° C., polycondense for 2 h...
Embodiment 1
[0044] A kind of intumescent paint for steel structure, by weight, comprises following component:
[0045]
[0046] Wherein, the dehydration catalyst in this embodiment is composed of amidinourea phosphate, ammonium polyphosphate and melamine pyrophosphate; wherein, the mass ratio of amidinourea phosphate, ammonium polyphosphate and melamine pyrophosphate is 2:1:1.
[0047] The antifoaming agent in this embodiment selects simethicone oil.
Embodiment 2
[0049] A kind of intumescent paint for steel structure, by weight, comprises following component:
[0050]
[0051]
[0052] Wherein, the dehydration catalyst in this embodiment is composed of amidinourea phosphate, ammonium polyphosphate and melamine pyrophosphate; wherein, the mass ratio of amidinourea phosphate, ammonium polyphosphate and melamine pyrophosphate is 2:1:1.
[0053] The antifoaming agent in this embodiment selects simethicone oil.
PUM
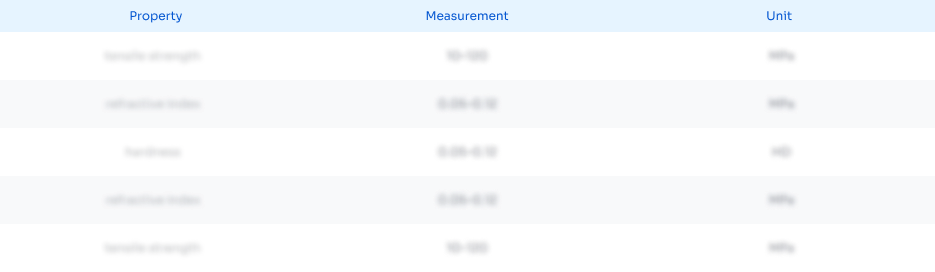
Abstract
Description
Claims
Application Information

- R&D
- Intellectual Property
- Life Sciences
- Materials
- Tech Scout
- Unparalleled Data Quality
- Higher Quality Content
- 60% Fewer Hallucinations
Browse by: Latest US Patents, China's latest patents, Technical Efficacy Thesaurus, Application Domain, Technology Topic, Popular Technical Reports.
© 2025 PatSnap. All rights reserved.Legal|Privacy policy|Modern Slavery Act Transparency Statement|Sitemap|About US| Contact US: help@patsnap.com