Halogen-free flame-retardant PBT material and preparation process thereof
A preparation process and technology for flame retardant materials, applied in the field of PBT materials and their preparation, can solve the problems of difficulty in sorting, easy bonding of PBT materials, and low purity of PBT materials.
- Summary
- Abstract
- Description
- Claims
- Application Information
AI Technical Summary
Problems solved by technology
Method used
Image
Examples
Embodiment 1
[0072] The invention provides a PBT halogen-free flame retardant material, which is composed of the following components: polybutylene terephthalate, halogen-free flame retardant, antioxidant, compatibilizer, silicate, glass fiber, six of which are The percentages of the components are as follows:
[0073] Polybutylene terephthalate: 58.5%;
[0074] Halogen-free flame retardant: 25%;
[0075] Antioxidant: 0.5%;
[0076] Compatibilizer: 5%;
[0077] Silicate: 1%;
[0078] Fiberglass: 10%.
[0079] In this embodiment, the viscosity of polybutylene terephthalate is selected as 1.0.
[0080] In this embodiment, the material used for the flame retardant is a combination of powdered melamine cyanurate and diethyl hypophosphite, which are mixed at a ratio of 1:8.
[0081] In the present embodiment, antioxidant selects tetrakis [beta-(3,5-di-tert-butyl-4-hydroxyphenyl) propionic acid] pentaerythritol ester, both high molecular weight phosphites are compounded, and according to 1...
Embodiment 2
[0091] The invention provides a PBT halogen-free flame retardant material, which is composed of the following components: polybutylene terephthalate, halogen-free flame retardant, antioxidant, compatibilizer, silicate, glass fiber, six of which are The percentages of the components are as follows:
[0092] Polybutylene terephthalate: 53.5%;
[0093] Halogen-free flame retardant: 22%;
[0094] Antioxidant: 0.5%;
[0095] Compatibilizer: 3%;
[0096] Silicate: 1%;
[0097] Fiberglass: 20%.
[0098] In this embodiment, the viscosity of polybutylene terephthalate is 0.8.
[0099] In this embodiment, the material used for the flame retardant is a combination of powdered melamine cyanurate and diethyl hypophosphite, which are mixed at a ratio of 1:8.
[0100] In the present embodiment, antioxidant selects tetrakis [beta-(3,5-di-tert-butyl-4-hydroxyphenyl) propionic acid] pentaerythritol ester, both high molecular weight phosphites are compounded, and according to 1: 2 mix. In ...
Embodiment 3
[0105] The invention provides a PBT halogen-free flame retardant material, which is composed of the following components: polybutylene terephthalate, halogen-free flame retardant, antioxidant, compatibilizer, silicate, glass fiber, six of which are The percentages of the components are as follows:
[0106] Polybutylene terephthalate: 47.5%;
[0107] Halogen-free flame retardant: 18%;
[0108] Antioxidant: 0.5%;
[0109] Compatibilizer: 3%;
[0110] Silicate: 1%;
[0111] Fiberglass: 30%.
[0112] In this embodiment, the viscosity of polybutylene terephthalate is 0.65.
[0113] In this embodiment, the material used for the flame retardant is a combination of powdered melamine cyanurate and diethyl hypophosphite, which are mixed at a ratio of 1:8.
[0114] In the present embodiment, antioxidant selects tetrakis [beta-(3,5-di-tert-butyl-4-hydroxyphenyl) propionic acid] pentaerythritol ester, both high molecular weight phosphites are compounded, and according to 1: 2 mix. ...
PUM
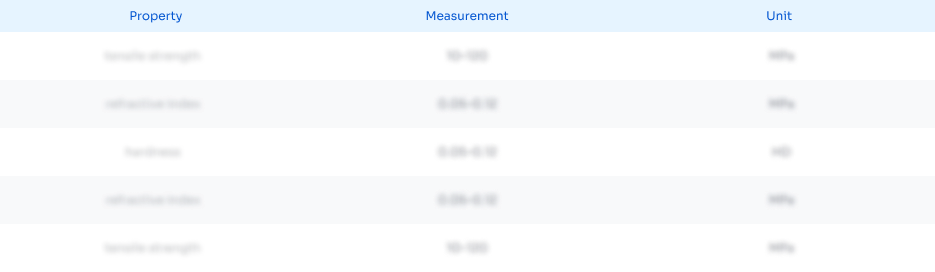
Abstract
Description
Claims
Application Information

- Generate Ideas
- Intellectual Property
- Life Sciences
- Materials
- Tech Scout
- Unparalleled Data Quality
- Higher Quality Content
- 60% Fewer Hallucinations
Browse by: Latest US Patents, China's latest patents, Technical Efficacy Thesaurus, Application Domain, Technology Topic, Popular Technical Reports.
© 2025 PatSnap. All rights reserved.Legal|Privacy policy|Modern Slavery Act Transparency Statement|Sitemap|About US| Contact US: help@patsnap.com