Method for removing hydrazine nitrate and hydroxylamine nitrate in nitric acid
A technology of hydroxylamine nitrate and hydrazine nitrate, applied in chemical instruments and methods, water/sludge/sewage treatment, metal/metal oxide/metal hydroxide catalyst, etc., can solve the problems of violent reaction, safety risk, leakage, etc. , to achieve the effect of mild reaction conditions, no safety hazards, and excellent economy.
- Summary
- Abstract
- Description
- Claims
- Application Information
AI Technical Summary
Problems solved by technology
Method used
Image
Examples
Embodiment 1
[0028] Get 95g through pre-abrasion treatment and dry granular coconut shell activated carbon carrier (4-8 mesh), add 82g mass fraction and be 18% new ammonium chloride solution, soak overnight, filter, the activated carbon particles after filtering are put into vacuum oven Dry at 80°C for 4 hours to obtain 104.6 g of activated carbon carrier pre-impregnated with ammonium chloride salt. Put the pre-soaked ammonium chloride activated carbon carrier dry particles into the pot of the medical sugar coating machine, and spray 40g of ruthenium trichloride solution in the rotating state, which contains 3.0g of metallic ruthenium; Silica gel solution, the mass fraction of silicon dioxide in the silica gel solution is 24%. The material was dried in a drying oven at 120°C for 12 hours, then transferred to a tube furnace, heated to 400°C for 80 minutes under nitrogen protection, and roasted at a constant temperature for 5 hours, with a nitrogen flow rate of 40L / h; changed to hydrogen and...
Embodiment 2
[0034] Get 95g through pre-abrasion treatment and dried granular coconut shell activated carbon carrier (4-8 order), add 90g mass fraction and be 12% new ammonium chloride solution, soak overnight, filter, and the activated carbon particles after filtering are put into vacuum oven Dry at 80°C for 4 hours to obtain 101.8 g of activated carbon carrier pre-impregnated with ammonium chloride salt. Put the pre-soaked ammonium chloride activated carbon carrier dry particles into the pot of the medical sugar coating machine, and spray 40g of ruthenium trichloride and chloroplatinic acid mixed solution under the rotating state. The solution contains 3.0g of metal ruthenium and 1.0g of metal platinum; continue to rotate Spray 9.5g of alkaline silica gel solution with pH 10.0, and the mass fraction of silicon dioxide in the silica gel solution is 18%. The material was dried in a drying oven at 120°C for 12 hours, then transferred to a tube furnace, heated to 400°C for 80 minutes under n...
Embodiment 3
[0037] The catalyst preparation operation is the same as in Example 1, except that the particle size of the carrier is 20 to 40 mesh, the pH of the silica gel solution is 9.0, and 4.5 g of ruthenium is contained in 40 g of ruthenium trichloride solution to obtain 196.2 g of 3# catalyst, and the catalyst moisture content is 48.5 %, the moisture content of the catalyst is 48.7%.
[0038] Take 100mL of prepared reaction feed liquid (the feed liquid composition is an aqueous solution of 1.0mol / L nitric acid, 0.1mol / L hydrazine nitrate and 0.3mol / L hydroxylamine nitrate, saturated with tributyl phosphate n-dodecane at a volume ratio of 1:100 Equilibrium) into a 250mL three-neck flask, turn on the constant temperature magnetic stirring water bath and preheat it to 95°C, add 5.23g of 3# catalyst (dry product) at a stirring speed of 400rpm, and time the reaction until there are no more bubbles in the reaction system. Reaction, record the reaction time, and recover the catalyst by vacu...
PUM
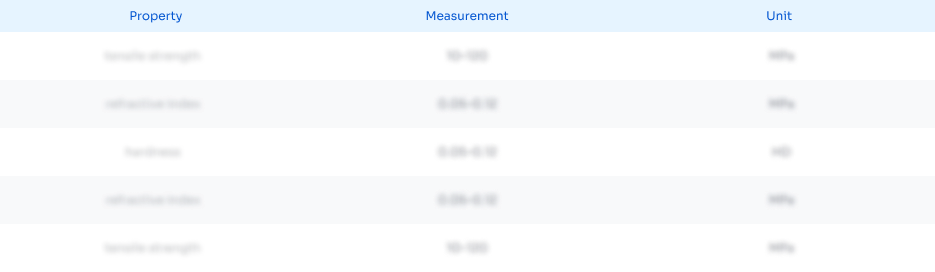
Abstract
Description
Claims
Application Information

- Generate Ideas
- Intellectual Property
- Life Sciences
- Materials
- Tech Scout
- Unparalleled Data Quality
- Higher Quality Content
- 60% Fewer Hallucinations
Browse by: Latest US Patents, China's latest patents, Technical Efficacy Thesaurus, Application Domain, Technology Topic, Popular Technical Reports.
© 2025 PatSnap. All rights reserved.Legal|Privacy policy|Modern Slavery Act Transparency Statement|Sitemap|About US| Contact US: help@patsnap.com