Method for separating and recovering silver and palladium from silver-palladium alloy scrap
A silver-palladium alloy, separation and recovery technology, applied in the field of precious metal recovery, can solve the problems of loss of precious metal ions, incomplete silver electrolysis, long recovery time, etc., achieve the effect of shortening the palladium recovery process, significant effect of palladium precipitation, and short recovery period
- Summary
- Abstract
- Description
- Claims
- Application Information
AI Technical Summary
Problems solved by technology
Method used
Examples
Embodiment 1
[0024] A method of separating the recovery silver and palladium from the silver palladium alloy waste, including the following steps: 500 g of the silver palladium alloy waste is placed in a chemometric ratio of 1.1 times industrial-grade nitric acid solution, silver palladium alloy waste is in silver The mass fraction is 80%, resulting in a palladium-containing leaching liquid; adding a chemical metering liquid containing 1.5 times a first deposit palladium, filtration, palladium salt and silver filtrate, palladium The precipitation rate is 99% or more, and the palladium ion concentration is less than 2 ppm in silver-rich filtrate; the resulting fine palladium salt, an oxidant-hydrogenant oxygen is added to the hydrochloric acid solution to obtain a palladium solution, a palladium copper. The impurity is less than 2 ppm, adding a chemical measurement of 1.5 times to a second fine palladium-ammonium chloride reaction to the prepared grastination solution to obtain high purity chlo...
Embodiment 2
[0026] A method of separating the recovery silver and palladium from the silver palladium alloy waste, including the following steps: 500 g of the silver palladium alloy waste is placed in a chemical measurement ratio of 1.2 times industrial-grade nitric acid solution, silver palladium alloy waste is in silver The mass fraction is 85%, resulting in a palladium-containing leaching liquid to add a chemical metering solution to a first concentrated palladium-butyl yellower having a chemical measurement of 2 times, and filtered the palladium salt and silver filtrate, palladium. The precipitation rate is 99.2%, and the palladium ion concentration is less than 1 ppm in silver-rich filtrate; the resulting fine palladium salt, oxidizing agent-sodium chlorite is added to the hydrochloric acid solution to obtain a palladium solution, a palladium copper. The impurity is less than 1 ppm, and the chemically measured apron-rich solution is added to a second depotium-ammonium chloride reaction t...
Embodiment 3
[0028] A method of separating the recovery silver and palladium from the silver palladium alloy waste, including the following steps: 500 g of the silver palladium alloy waste is placed in a chemical measurement ratio of 1.2 times industrial-grade nitric acid solution, silver palladium alloy waste is in silver The mass fraction is 98.5% to obtain palladium-containing leaching liquid; adding a chemical metering solution to a palladium-containing liquid to a first concentrated palladium-butbate ketode oxime to selectively precipitate palladium, filtered from palladium salt and silver filtrate, palladium The precipitation rate is 99.2%, and the palladium ion concentration is less than 1 ppm in silver-rich filtrate; the resulting fine palladium salt, the oxidant-hypochlorite is added to the hydrochloric acid solution to dissolve filtration, to obtain a palladium solution, palladium copper gem of silver copper 锗 锗 锗 锗 锗1 ppm, adding a chemical measurement of 2 times a second depotium-a...
PUM
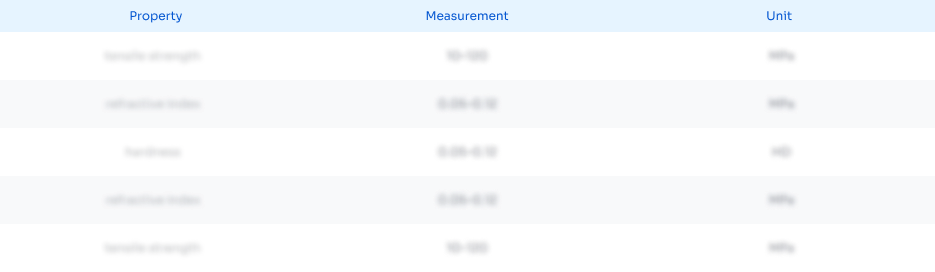
Abstract
Description
Claims
Application Information

- Generate Ideas
- Intellectual Property
- Life Sciences
- Materials
- Tech Scout
- Unparalleled Data Quality
- Higher Quality Content
- 60% Fewer Hallucinations
Browse by: Latest US Patents, China's latest patents, Technical Efficacy Thesaurus, Application Domain, Technology Topic, Popular Technical Reports.
© 2025 PatSnap. All rights reserved.Legal|Privacy policy|Modern Slavery Act Transparency Statement|Sitemap|About US| Contact US: help@patsnap.com