Method for preparing spherical titanium nitride powder through reaction atomization method
A technology of titanium nitride powder and atomization method, applied in the field of powder metallurgy, can solve the problems of difficulty in powder feeding and dispersion, increased oxygen content of raw materials, and high oxygen content of titanium nitride powder, so as to avoid the limitation of raw material purity and particle size, improve the Production efficiency, the effect of improving nitrogen content
- Summary
- Abstract
- Description
- Claims
- Application Information
AI Technical Summary
Problems solved by technology
Method used
Image
Examples
Embodiment 1
[0033] a) Put the titanium wire into a 1:5 solution of hydrogen fluoride and nitric acid, ultrasonically clean it at 50°C for 20 minutes, dry it and set it aside;
[0034] b) Vacuumize the atomization reaction chamber to 10 -1 Pa, refill N 2 The active gas establishes a protective atmosphere and adjusts the pressure of the atomization reaction chamber to +50Kpa;
[0035] c) Preheat the titanium wire to 500°C by high-frequency induction heating equipment; 2 The plasma melts the preheated titanium filament into a continuous stream or droplets, and at the same time, the highly reactive N 2 The plasma reacts rapidly with the stream or droplets to form titanium nitride droplets;
[0036]The above radio frequency plasma modulation and stabilization: using radio frequency plasma power of 50KW, the plasma is stabilized in two steps, the first step is to use argon as the main gas to ignite the plasma, the flow rate is 30L / min, argon is used as the edge gas to cool and compress the p...
Embodiment 2
[0040] a) Put the titanium wire into a 1:5 solution of hydrogen fluoride and nitric acid, ultrasonically clean it at 30°C for 30 minutes, dry it and set it aside;
[0041] b) Vacuumize the atomization reaction chamber to 10 -2 Pa, refill N 2 The active gas establishes a protective atmosphere and adjusts the pressure of the atomization reaction chamber to 10Kpa;
[0042] c) Preheat the titanium wire to 1000°C by high-frequency induction heating equipment; 2 The plasma melts the preheated titanium filament into a continuous stream or droplets, and at the same time, the highly reactive N 2 The plasma reacts rapidly with the stream or droplets to form titanium nitride droplets;
[0043] The above radio frequency plasma modulation and stabilization: using radio frequency plasma power 60KW, the plasma is stabilized in two steps, the first step is to use argon as the main gas to ignite the plasma, the flow rate is 35L / min, argon is used as the edge gas to cool and compress the pla...
Embodiment 3
[0047] a) Put the titanium wire into a 1:5 solution of hydrogen fluoride and nitric acid, ultrasonically clean it at 60°C for 10 minutes, and dry it for later use;
[0048] b) Vacuumize the atomization reaction chamber to 10 -3 Pa, refill N 2 The active gas establishes a protective atmosphere and adjusts the pressure of the atomization reaction chamber to -10Kpa;
[0049] c) Preheat the titanium wire to 800°C by high-frequency induction heating equipment; 2 The plasma melts the preheated titanium filament into a continuous stream or droplets, and at the same time, the highly reactive N 2 The plasma reacts rapidly with the stream or droplets to form titanium nitride droplets;
[0050] The above radio frequency plasma modulation and stabilization: use radio frequency plasma power of 40KW, the plasma is stabilized in two steps, the first step is to use argon as the main gas to ignite the plasma, the flow rate is 25L / min, argon is used as the side gas to cool and compress the p...
PUM
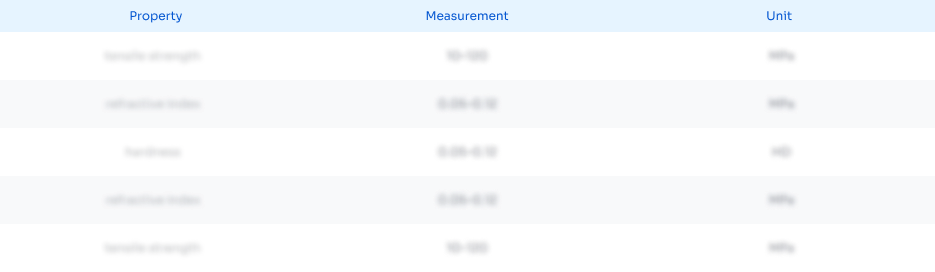
Abstract
Description
Claims
Application Information

- Generate Ideas
- Intellectual Property
- Life Sciences
- Materials
- Tech Scout
- Unparalleled Data Quality
- Higher Quality Content
- 60% Fewer Hallucinations
Browse by: Latest US Patents, China's latest patents, Technical Efficacy Thesaurus, Application Domain, Technology Topic, Popular Technical Reports.
© 2025 PatSnap. All rights reserved.Legal|Privacy policy|Modern Slavery Act Transparency Statement|Sitemap|About US| Contact US: help@patsnap.com