Modified glass material for repairing carbon/carbon composite material SiC coating based on laser cladding method and preparation and use methods
A carbon composite material, laser cladding technology, applied in glass manufacturing equipment, glass furnace equipment, manufacturing tools and other directions, can solve the problems of low absorption rate, difficult to prepare coatings, poor cladding quality, etc., to improve the absorption rate, The effect of improving cladding quality and improving anti-oxidation performance
- Summary
- Abstract
- Description
- Claims
- Application Information
AI Technical Summary
Problems solved by technology
Method used
Image
Examples
Embodiment 1
[0021] 1) Weigh SiO with a molar percentage of 70% respectively 2 Powder, 20% B 2 o 3 Powder, 9% Al 2 o 3 Powder with 1% Sm 2 o 3 Powder, mixed evenly after ball milling for 3 hours;
[0022] 2) Put the mixed raw material powder into a corundum crucible and place it in a muffle furnace, raise the temperature to 1573K with the furnace in an air atmosphere, and continue heat treatment for 2 hours to fully melt and react the raw material powder at high temperature, and then take it out directly Cool to room temperature to obtain Sm modified borosilicate glass;
[0023] 3) In order to facilitate subsequent repair and use, the Sm-modified borosilicate glass block that has been melted and formed is ground into powder;
[0024] 4) Cladding the damaged area of the C / C composite SiC coating on the modified glass powder using a fiber laser, and verifying the improvement of the borosilicate glass coating by the rare earth element Sm by comparing the process parameters and observ...
Embodiment 2
[0026] 1) Weigh SiO with a molar percentage of 70% respectively 2 Powder, 20% B 2 o 3 powder, 5% Al 2 o 3 Powder with 5% Sm 2 o 3 Powder, mixed evenly after ball milling for 3 hours;
[0027] 2) Put the mixed raw material powder into a corundum crucible and place it in a muffle furnace, raise the temperature to 1573K with the furnace in an air atmosphere, and continue heat treatment for 2 hours to fully melt and react the raw material powder at high temperature, and then take it out directly Cool to room temperature to obtain Sm modified borosilicate glass;
[0028] 3) In order to facilitate subsequent repair and use, the Sm-modified borosilicate glass block that has been melted and formed is ground into powder;
[0029] 4) Cladding the damaged area of the C / C composite SiC coating on the modified glass powder using a fiber laser, and verifying the improvement of the borosilicate glass coating by the rare earth element Sm by comparing the process parameters and observ...
Embodiment 3
[0031] 1) Weigh respectively SiO with a molar percentage of 65%. 2 Powder, 20% B 2 o 3 powder, 5% Al 2 o 3 Powder with 10% Sm 2 o 3 Powder, mixed evenly after ball milling for 3 hours;
[0032] 2) Put the mixed raw material powder into a corundum crucible and place it in a muffle furnace, raise the temperature to 1573K with the furnace in an air atmosphere, and continue heat treatment for 2 hours to fully melt and react the raw material powder at high temperature, and then take it out directly Cool to room temperature to obtain Sm modified borosilicate glass;
[0033] 3) In order to facilitate subsequent repair and use, the Sm-modified borosilicate glass block that has been melted and formed is ground into powder;
[0034] 4) Cladding of the damaged area of the C / C composite SiC coating was carried out on the modified glass powder by using a fiber laser, and the improvement of the borosilicate glass coating by the rare earth element Sm was verified by comparing the proc...
PUM
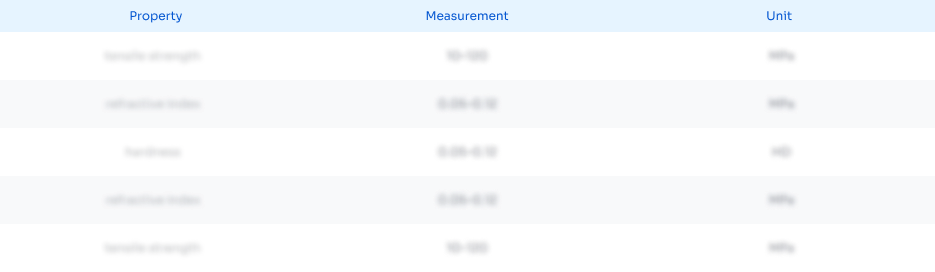
Abstract
Description
Claims
Application Information

- R&D
- Intellectual Property
- Life Sciences
- Materials
- Tech Scout
- Unparalleled Data Quality
- Higher Quality Content
- 60% Fewer Hallucinations
Browse by: Latest US Patents, China's latest patents, Technical Efficacy Thesaurus, Application Domain, Technology Topic, Popular Technical Reports.
© 2025 PatSnap. All rights reserved.Legal|Privacy policy|Modern Slavery Act Transparency Statement|Sitemap|About US| Contact US: help@patsnap.com