Isopropylbenzene recycling method in epoxypropane preparation process
A technology of propylene oxide and cumene, applied in the field of propylene oxide preparation, can solve the problems of excessive Na residue, influence on epoxidation strength, consumption of sodium hydroxide, etc. The effect of preventing the loss and sintering of metal components and improving the adsorption effect
- Summary
- Abstract
- Description
- Claims
- Application Information
AI Technical Summary
Problems solved by technology
Method used
Image
Examples
Embodiment 1
[0042] Preparation of Catalyst I.
[0043] 1) 97.5gZrO 2 The carrier was impregnated in 200ml aqueous solution containing 1.33g of chloroplatinic acid, and impregnated under reflux at 60°C for 2h; no chlorine was detected after washing and filtering 4 times, dried at 110°C for 2h, and calcined at 300°C for 4h to obtain an intermediate product.
[0044]2) Put the intermediate product in the electrolytic cell, pass 2g of Ag through the electrolytic cell, the current density is 1A, 50ml / min nitrogen gas is passed through the deposition process, the deposition time is 3h, and the type I catalyst is obtained after roasting at 300°C for 4h.
Embodiment 2
[0046] Preparation of Catalyst II.
[0047] 1) 97.5gZrO 2 The carrier was impregnated in 200ml aqueous solution containing 0.84g palladium chloride, refluxed at 60°C for 2h; washed and filtered 5 times, dried at 110°C for 2h, and calcined at 300°C for 4h to obtain an intermediate product.
[0048] 2) Put the intermediate product in the electrolytic cell, pass 2g of Ag through the electrolytic cell, the current density is 0.5A, 50ml / min nitrogen gas is passed through the deposition process, the deposition time is 3h, and the type II catalyst is obtained after roasting at 300°C for 4h .
Embodiment 3
[0050] Preparation of Catalyst III.
[0051] 1) 97.5gZrO 2 The carrier was impregnated in 200ml aqueous solution containing 19.5g of nickel nitrate hexahydrate, and impregnated under reflux at 60°C for 2h; after washing and filtering 5 times, it was dried at 110°C for 2h, and calcined at 300°C for 4h to obtain an intermediate product.
[0052] 2) Put the intermediate product in the electrolytic cell, pass 2g of Ag through the electrolytic cell, the current density is 0.5A, 50ml / min nitrogen gas is passed through the deposition process, the deposition time is 3h, and after calcination at 300°C for 4h, a type III catalyst is obtained .
PUM
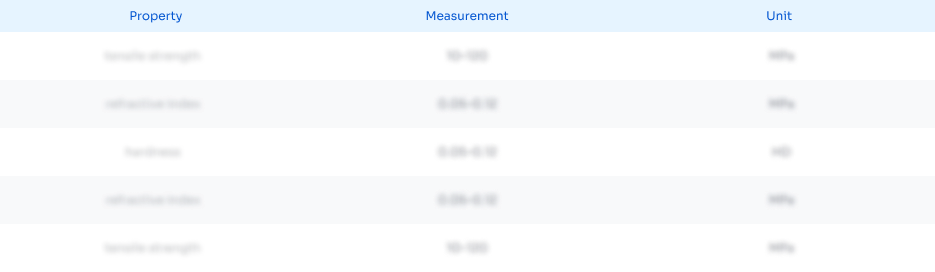
Abstract
Description
Claims
Application Information

- R&D
- Intellectual Property
- Life Sciences
- Materials
- Tech Scout
- Unparalleled Data Quality
- Higher Quality Content
- 60% Fewer Hallucinations
Browse by: Latest US Patents, China's latest patents, Technical Efficacy Thesaurus, Application Domain, Technology Topic, Popular Technical Reports.
© 2025 PatSnap. All rights reserved.Legal|Privacy policy|Modern Slavery Act Transparency Statement|Sitemap|About US| Contact US: help@patsnap.com