Epoxy resin and graphene composite heat dissipation coating for 6061 aluminum alloy plate and preparation method
An aluminum alloy sheet and graphene composite technology, applied in epoxy resin coatings, anti-corrosion coatings, coatings and other directions, can solve the problem that the improvement of heat dissipation performance of 6061 aluminum alloy sheet is not particularly obvious, it is difficult to improve the heat dissipation performance of 6061 aluminum alloy sheet, and it is impossible to improve the heat dissipation performance of 6061 aluminum alloy sheet. To meet the heat dissipation requirements and other issues, to achieve the effects of excellent adhesion, improved heat dissipation, and high insulation
- Summary
- Abstract
- Description
- Claims
- Application Information
AI Technical Summary
Problems solved by technology
Method used
Image
Examples
Embodiment 1
[0064] The comparative example of Example 1 is the existing nano heat dissipation coating A (corresponding to the curve A in the figure), the comparative example of Example 2 is the existing nano heat dissipation coating B (corresponding to the curve B in the figure), and the comparative example of Example 3 is the existing nano heat dissipation coating Coating C (corresponding to the C curve in the figure), the comparative example of Example 4 is the existing nano heat dissipation coating D (corresponding to the D curve in the figure), and the comparative example of Example 5 is the existing nano heat dissipation coating E (corresponding to the E curve in the figure), The inspection result of the uncoated 6061 aluminum alloy plate corresponds to the 2 curve, and the inspection result of the 6061 aluminum alloy plate coated with the heat dissipation coating of the present application corresponds to the 1 curve.
[0065] Figure 1-Figure 5 , the heat source gradually heats up, ...
Embodiment 2
[0085] A kind of epoxy resin graphene composite heat-dissipating coating for 6061 aluminum alloy plate, comprises the raw material of following weight part:
[0086] 18 parts of epoxy resin,
[0087] Active diluent 4.5 parts,
[0088] Dispersant 1.3 parts,
[0089] 3.5 parts of curing agent,
[0090] 2.3 parts of cerium compound,
[0091] Nitrogen-boron compound 1.1 parts,
[0092] 2.3 parts of titanium compound,
[0093] Graphene oxide powder 0.0009 part.
[0094] The epoxy resin is bisphenol A type epoxy resin E-51.
[0095] The curing agent is synthesized by reaction of epoxy resin and aliphatic amine, which is curing agent T31.
[0096] The dispersant is polyacrylic acid ammonium salt AD8058, and the reactive diluent is linear aliphatic monoepoxy diluent 602.
[0097] The cerium compound is cerium nitrate, the nitrogen-boron compound is nitrogen borate, and the titanium compound is titanium fluoride.
[0098] A kind of epoxy resin graphene composite heat-dissipati...
Embodiment 3
[0103] A kind of epoxy resin graphene composite heat-dissipating coating for 6061 aluminum alloy plate, comprises the raw material of following weight part:
[0104] 20 parts of epoxy resin,
[0105] Active diluent 5 parts,
[0106] Dispersant 1.5 parts,
[0107] 4 parts curing agent,
[0108] 2.5 parts of cerium compound,
[0109] Nitrogen-boron compound 1 part,
[0110] Titanium compound 2 parts,
[0111] Graphene oxide powder 0.001 part.
[0112] The epoxy resin is bisphenol A type epoxy resin E-44.
[0113] The curing agent is synthesized by reaction of epoxy resin and aliphatic amine, which is curing agent 593.
[0114] The dispersant is ammonium polyacrylate 1124, and the reactive diluent is linear aliphatic monoepoxy diluent 501.
[0115] The cerium compound is cerium oxide, the nitrogen-boron compound is boron nitride, and the titanium compound is titanium oxide.
[0116] A kind of epoxy resin graphene composite heat-dissipating coating for 6061 aluminum alloy...
PUM
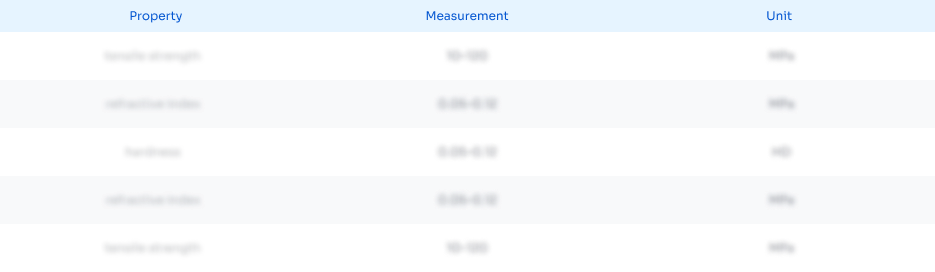
Abstract
Description
Claims
Application Information

- R&D
- Intellectual Property
- Life Sciences
- Materials
- Tech Scout
- Unparalleled Data Quality
- Higher Quality Content
- 60% Fewer Hallucinations
Browse by: Latest US Patents, China's latest patents, Technical Efficacy Thesaurus, Application Domain, Technology Topic, Popular Technical Reports.
© 2025 PatSnap. All rights reserved.Legal|Privacy policy|Modern Slavery Act Transparency Statement|Sitemap|About US| Contact US: help@patsnap.com