Polyether end group functionalized polymer prepared by negative ion polymerization technology and preparation method and application thereof
A technology of functionalized polymer and end group, which is applied in the field of polyether end-group functionalized polymer and its preparation, can solve the problem of reducing the end-group functionalization end-capping efficiency, easily producing dimers and multimers, affecting extreme It can improve the processing performance and mechanical properties, low cost and mild preparation conditions.
- Summary
- Abstract
- Description
- Claims
- Application Information
AI Technical Summary
Problems solved by technology
Method used
Image
Examples
Embodiment 1
[0049] The reaction kettle was washed before polymerization, and the inert gas was evacuated. Then, 1500g cyclohexane, 105g butadiene and 45g styrene were introduced in sequence in a 5-liter stainless steel reaction kettle to prepare a solution with a monomer mass concentration of 10%. 1. Add the structure regulator ETE (ethyl tetrahydrofurfuryl ether) according to the molar ratio ETE / n-BuLi=1, start stirring, in a constant temperature water bath at 50°C, according to the design molecular weight of 13×10 4 , add 5.9mmol initiator n-BuLi (n-butyllithium) to initiate polymerization, react for 30 minutes, add DVB (divinylbenzene) according to molar ratio DVB / n-BuLi=2, after coupling reaction for 30min, molar ratio A1(i-Bu) 3 / n-BuLi=10 add catalyst A1(i-Bu) 3 According to the design polyether degree of polymerization = 20, add ethylene oxide and continue to react for 60 minutes at 50°C. Finally, the terminator isopropanol was added to terminate the reaction, the glue solution w...
Embodiment 2
[0056] According to the synthesis method of Example 1, the difference is that only 150g of butadiene monomer is added to form a solution with a monomer mass concentration of 15%, and the structure regulator DTHFP (double tetrahydro furfuryl propane).
[0057] The molecular weight of GPC before and after coupling is 13.1×10 4 and 16.3×10 4 , the molecular weight distributions were 1.04 and 1.10, respectively, and the coupling efficiency was 46.3%. The raw rubber has a moderate viscosity, does not stick to the roller, is easy to mix with additives and fillers, has low heat generation, and is easy to unload, indicating that the prepared end-functionalized polymer has good processability.
Embodiment 3-6
[0059] Prepared according to the method of Example 1, the difference is to change Bd / St (mass ratio), Bd is butadiene, St is styrene, and the mechanical properties of Bd / St and the prepared terminal functionalized polymer composite are shown in Table 4.
[0060] Table 4
[0061]
[0062]
PUM
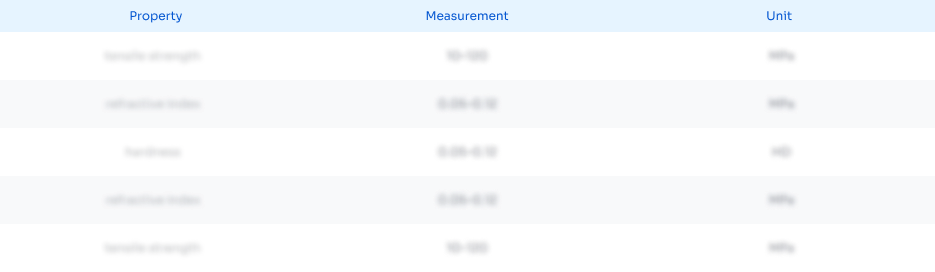
Abstract
Description
Claims
Application Information

- R&D
- Intellectual Property
- Life Sciences
- Materials
- Tech Scout
- Unparalleled Data Quality
- Higher Quality Content
- 60% Fewer Hallucinations
Browse by: Latest US Patents, China's latest patents, Technical Efficacy Thesaurus, Application Domain, Technology Topic, Popular Technical Reports.
© 2025 PatSnap. All rights reserved.Legal|Privacy policy|Modern Slavery Act Transparency Statement|Sitemap|About US| Contact US: help@patsnap.com