A method for separating germanium by inorganic precipitation in zinc hydrometallurgy solution
A technology of hydrometallurgy and inorganic precipitation, which is applied to the improvement of process efficiency, can solve the problems of large consumption of tannin, large consumption of germanium in tannin deposition, and loss of germanium, so as to avoid the generation of hydrogen arsine, The effect of clean and efficient process and easy subsequent processing
- Summary
- Abstract
- Description
- Claims
- Application Information
AI Technical Summary
Problems solved by technology
Method used
Examples
Embodiment 1
[0021] Example 1: Precipitation and separation of germanium was carried out using a germanium-rich zinc oxide fume leach solution (Zn 142 g / L, Fe 8.52 g / L, Ge 0.167 g / L, pH 1.56) as a raw material;
[0022] The method for separating germanium by inorganic precipitation in zinc hydrometallurgy solution, the specific steps are as follows:
[0023] (1) By controlling the acidity at the end point of the hydro-smelting zinc leaching process, the pH value of the hydro-smelting zinc leaching solution is adjusted to 1.0-2.0; the pH of the germanium-rich zinc oxide fume leaching solution in this embodiment is 1.56, and no further adjustment is required;
[0024] (2) The temperature of the zinc hydro-smelting solution is 50°C, and air is introduced into the zinc hydro-smelting solution to react with ferrous ions until the ferric ion concentration is 4.11g / L to obtain solution A;
[0025] (3) Heat the mixed liquid A to a temperature of 70~75°C for 3 hours to react for 3 hours, so that ir...
Embodiment 2
[0027] Example 2: Precipitation and separation of germanium was carried out using a germanium-rich zinc oxide fume leaching solution (Zn 139 g / L, Fe 10.33 g / L, Ge 0.289 g / L, pH 3.11) as a raw material;
[0028] The method for separating germanium by inorganic precipitation in zinc hydrometallurgy solution, the specific steps are as follows:
[0029] (1) Regulate the pH value of the hydro-smelting zinc leaching solution to 1.12 through the hydro-smelting zinc waste electrolyte;
[0030] (2) The temperature of the zinc hydrometallurgy solution is 55°C, and air is introduced into the zinc hydrometallurgy solution to react with ferrous ions until the ferric ion concentration is 5.93g / L to obtain solution A;
[0031] (3) Raise the temperature of the mixture A to a temperature of 80~85°C and react for 4 hours, so that iron ions and germanate ions are precipitated synchronously to form germanium slag, and the germanium content in the germanium slag is mainly Fe 3 GeO 2 (OH) 5 (SO ...
Embodiment 3
[0033] Example 3: Precipitation and separation of germanium was carried out using a germanium-rich zinc oxide fume leach solution (Zn 145 g / L, Fe 6.85 g / L, Ge 0.096 g / L, pH 2.72) as a raw material;
[0034] The method for separating germanium by inorganic precipitation in zinc hydrometallurgy solution, the specific steps are as follows:
[0035] (1) Regulate the pH value of the hydro-smelting zinc leaching solution to 1.98 through the hydro-smelting zinc waste electrolyte;
[0036] (2) The temperature of the zinc hydrometallurgy solution is 60°C, and air is introduced into the zinc hydrometallurgy solution to react with ferrous ions until the ferric ion concentration is 5.21g / L to obtain solution A;
[0037] (3) Raise the temperature of the mixture A to a temperature of 95~100°C for 3 hours to react for 3 hours, so that iron ions and germanate ions are precipitated simultaneously to form a germanium deposit slag, and the germanium object in the germanium deposit slag is mainly...
PUM
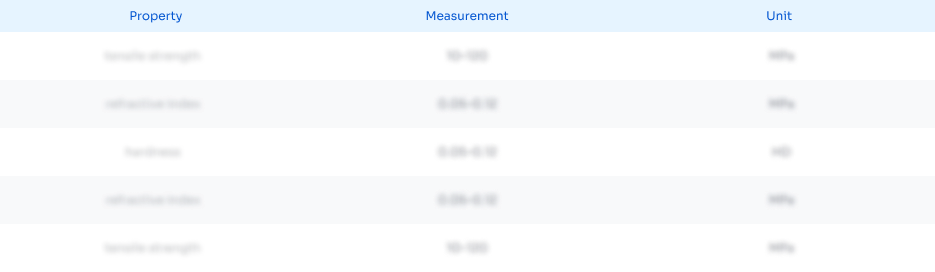
Abstract
Description
Claims
Application Information

- R&D
- Intellectual Property
- Life Sciences
- Materials
- Tech Scout
- Unparalleled Data Quality
- Higher Quality Content
- 60% Fewer Hallucinations
Browse by: Latest US Patents, China's latest patents, Technical Efficacy Thesaurus, Application Domain, Technology Topic, Popular Technical Reports.
© 2025 PatSnap. All rights reserved.Legal|Privacy policy|Modern Slavery Act Transparency Statement|Sitemap|About US| Contact US: help@patsnap.com