Spiral tool electrode and bipolar electrolysis grinding processing method thereof
A tool electrode and processing method technology, applied in the field of electrolytic grinding compound processing, can solve the problems of damage accuracy and surface integrity, low efficiency, short-circuit prone to processing, etc., to improve processing efficiency, processing stability, and process stability. Good, improve the effect of short circuit phenomenon
- Summary
- Abstract
- Description
- Claims
- Application Information
AI Technical Summary
Problems solved by technology
Method used
Image
Examples
Embodiment Construction
[0028] The present invention will be further explained below in conjunction with specific drawings.
[0029] Such as figure 1 As shown, a spiral tool electrode includes a tool electrode substrate 1, an abrasive layer 2, an electrically insulating layer 3, and an inert metal layer 4. The tool electrode substrate 1 is made of a common conductive material, such as carbon steel, and made into a stepped cylindrical structure. The large-diameter cylindrical part is called the tool bar 5, the small-diameter cylindrical part is called the tool head 6, and the tool head 6 The outer diameter is less than 1mm. The spiral groove 7 is machined on the outer surface of the side wall of the tool head 6 by a common process, such as ion milling or laser engraving, and the distributed length of the spiral groove 7 on the tool head 6 is less than or equal to the length of the tool head 6. By conventional methods, such as electroplating or chemical plating, the insulating abrasive is fixed on the b...
PUM
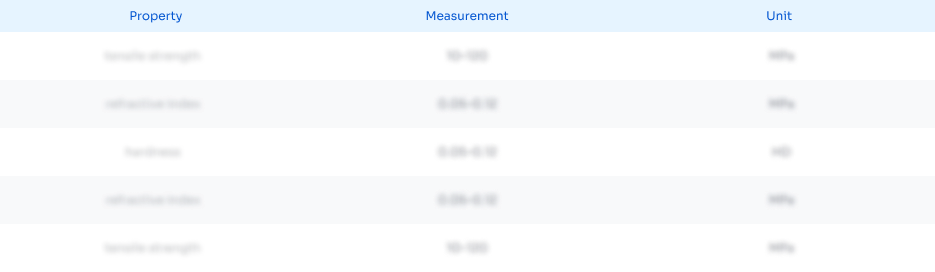
Abstract
Description
Claims
Application Information

- R&D
- Intellectual Property
- Life Sciences
- Materials
- Tech Scout
- Unparalleled Data Quality
- Higher Quality Content
- 60% Fewer Hallucinations
Browse by: Latest US Patents, China's latest patents, Technical Efficacy Thesaurus, Application Domain, Technology Topic, Popular Technical Reports.
© 2025 PatSnap. All rights reserved.Legal|Privacy policy|Modern Slavery Act Transparency Statement|Sitemap|About US| Contact US: help@patsnap.com