Method for preparing boron-doped nano-metal/porous silicon-carbon composite negative electrode based on cut silicon wastes
A technology of nano-metal and porous silicon, which is applied in the direction of nanotechnology, silicon compound, nanotechnology, etc. for materials and surface science, and can solve the problem of silicon material loss and other issues
- Summary
- Abstract
- Description
- Claims
- Application Information
AI Technical Summary
Problems solved by technology
Method used
Image
Examples
Embodiment 1
[0030] Example 1: A method for preparing boron-doped nano-metal / porous silicon-carbon composite negative electrodes based on cutting silicon waste, the specific steps are as follows:
[0031] (1) Diamond wire cutting silicon waste is dried, crushed, and ground to obtain waste silicon powder. At room temperature and under stirring conditions, the waste silicon powder is soaked and purified in an alkali-alcohol solution (NaOH-ethanol solution) for 180 minutes. Separate, wash the solid repeatedly with deionized water until the washing liquid is neutral to obtain purified silicon powder; wherein the mass concentration of NaOH in the alkali-alcohol solution (NaOH-methanol solution) is 10%,
[0032] (2) Place the purified silicon powder in step (1) in the HF-metal salt-alcohol solution system (HF-AgNO 3 -methanol solution system) and metal Ag-assisted etching treatment at a temperature of 60°C for 120min, ultrasonically rinsed with deionized water until the washing liquid is neutral...
Embodiment 2
[0037] Embodiment 2: A method for preparing a boron-doped nano-metal / porous silicon-carbon composite negative electrode based on cutting silicon waste, the specific steps are as follows:
[0038] (1) Diamond wire cutting silicon waste is dried, crushed, and ground to obtain waste silicon powder. At room temperature and under stirring conditions, the waste silicon powder is soaked and purified in an alkali-alcohol solution (NaOH-methanol solution) for 150 minutes. Solid-liquid Separation, washing the solid with deionized water several times until the washing liquid is neutral to obtain purified silicon powder; wherein the mass concentration of NaOH in the alkali-alcohol solution (NaOH-methanol solution) is 15%;
[0039] (2) Place the purified silicon powder in step (1) in the HF-metal salt-alcohol solution system (HF-CuNO 3 -methanol solution system) and at a temperature of 60°C, metal Cu-assisted etching treatment was carried out for 120 min, ultrasonically rinsed with deioniz...
Embodiment 3
[0044] Embodiment 3: A method for preparing boron-doped nano-metal / porous silicon-carbon composite negative electrode based on cutting silicon waste, the specific steps are as follows:
[0045] (1) Diamond wire cutting silicon waste is dried, crushed, and ground to obtain waste silicon powder. At room temperature and under stirring conditions, the waste silicon powder is soaked and purified in an alkali-alcohol solution (NaOH-methanol solution) for 200 minutes. Separation, washing the solid with deionized water several times until the washing liquid is neutral to obtain purified silicon powder; wherein the mass concentration of NaOH in the alkali-alcohol solution (NaOH-methanol solution) is 20%;
[0046] (2) Put the purified silicon powder in step (1) in the HF-metal salt-alcohol solution system (HF-NiNO 3 -methanol solution system) at a temperature of 70° C. for 100 minutes of metal Ni-assisted etching treatment, ultrasonically rinsed with deionized water until the washing li...
PUM
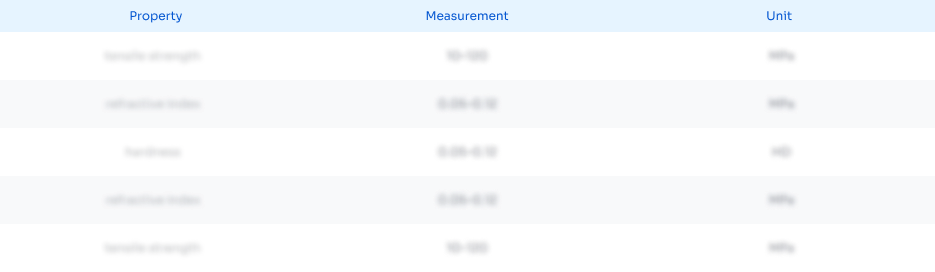
Abstract
Description
Claims
Application Information

- R&D
- Intellectual Property
- Life Sciences
- Materials
- Tech Scout
- Unparalleled Data Quality
- Higher Quality Content
- 60% Fewer Hallucinations
Browse by: Latest US Patents, China's latest patents, Technical Efficacy Thesaurus, Application Domain, Technology Topic, Popular Technical Reports.
© 2025 PatSnap. All rights reserved.Legal|Privacy policy|Modern Slavery Act Transparency Statement|Sitemap|About US| Contact US: help@patsnap.com