Microwave-assisted efficient construction method for high-strength interface of carbon-based reinforcement/resin composite material
A resin composite material and microwave-assisted technology, which is applied in the field of composite materials, can solve the problems of carbon-based reinforcement mechanical property damage, difficult control of uniformity, low efficiency, etc., to achieve the effect of high efficiency and quick enhancement, and solve the loss of mechanical properties
- Summary
- Abstract
- Description
- Claims
- Application Information
AI Technical Summary
Problems solved by technology
Method used
Image
Examples
Embodiment 1
[0022] The mass parts of epoxy resin, amine curing agent and diluent are prepared according to the ratio of 60:37:40. The epoxy resin adopts 4,5-epoxyhexane-1,2-dicarboxylic acid diglycidyl ester, and the amine curing agent adopts 1,3-bis-(γ-aminopropyl)-5,5-dimethyl For hydantoin, the diluent is ethylene glycol diglycidyl ether. The carbon-based reinforcement is modified into graphene microplatelets, and nickel phthalocyanine nanowires act as both transition metal-type catalysts and nanoparticles. Grind the graphite powder and the nickel phthalocyanine nanowire sheet fully separately, then mix them according to the mass ratio of 50:1.5, and fully mix them with a double-helix conical mixer for 0.5h, so that the appearance of the mixed nanoparticles no longer presents the original nanoparticles The state of the ingredients forms a powdery precursor. Subsequently, 1.5 g of the powdery precursor and 50 mL of deionized water were treated with magnetic stirring at a rate of 3500 ...
Embodiment 2
[0027] Toray T800 carbon fiber was desized by reflux with acetone for 24 hours to prepare desized fiber tow. Grind ferrous chloride, graphite powder ink and zinc oxide nanowires fully separately, then mix them according to the mass ratio of 1:50:0.5, and fully mix them with a double-helix conical mixer for 0.5h, so that the appearance of the mixed nanoparticles The state of the original nanoparticle composition is no longer present, and a powdery precursor is formed. Subsequently, 1.5 g of well-mixed nanoparticles and 50 mL of 1-butyl-3-methylimidazolium tetrafluoroborate were treated with magnetic stirring at a rate of 3500 rpm for 1 h, while removing insufficiently ground nanoparticles to prepare a powder Precursor dispersion. In the resin system, the main resin is a compound of multifunctional cycloaliphatic epoxy resin and triglycidyl isocyanate with a mass fraction of 40:60, and the curing agent is 1-cyanoethyl-2-ethyl- A compound of 4-methylimidazole and 2,2-bis(amino-...
Embodiment 3
[0032] The main resin is a compound of triglycidyl tripolyisocyanate and 1,3-diglycidyl-5,5-dimethylhydantoin epoxy resin with a mass fraction of 50:50, and the curing agent is 2, 2-bis(amino-4-hydroxyphenyl)hexafluoropropane and 1-cyanoethyl-2-ethyl-4-methylimidazole are at a mass fraction of 30:10, and the reactive diluent is diglycidyl adipate The ratio of ester, main resin, curing agent, and reactive diluent in parts by mass is 100:40:20. Nickel phthalocyanine nanowires act as both transition metal-type catalysts and nanoparticles. Grind graphite powder and nickel phthalocyanine nanowires fully separately, then mix them at a mass ratio of 50:1.5, and mix them thoroughly for 0.5 hours, so that the appearance of the mixed nanoparticles no longer shows the state of the original nanoparticle components, and a cage-like interface is prepared Structural precursors. Then, 1.5 g of well-mixed nanoparticles and 50 mL of N,N dimethylformamide were treated with magnetic stirring at...
PUM
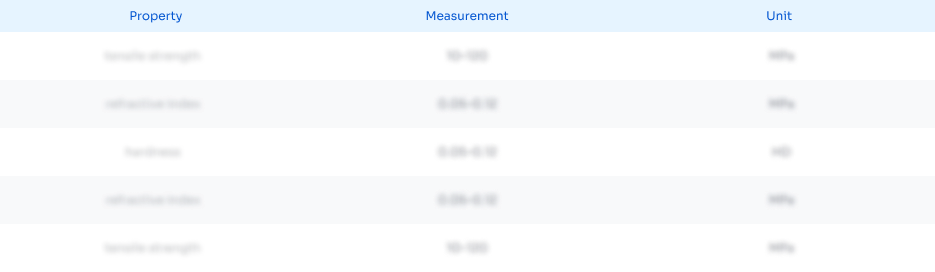
Abstract
Description
Claims
Application Information

- R&D Engineer
- R&D Manager
- IP Professional
- Industry Leading Data Capabilities
- Powerful AI technology
- Patent DNA Extraction
Browse by: Latest US Patents, China's latest patents, Technical Efficacy Thesaurus, Application Domain, Technology Topic, Popular Technical Reports.
© 2024 PatSnap. All rights reserved.Legal|Privacy policy|Modern Slavery Act Transparency Statement|Sitemap|About US| Contact US: help@patsnap.com