Surface coating for building aluminum alloy template capable of preventing concrete adhesion and preparation method of surface coating
A technology of aluminum alloy formwork and surface coating, applied in the direction of coating, etc., to achieve the effect of high mechanical strength, excellent chemical stability, and high bonding strength
- Summary
- Abstract
- Description
- Claims
- Application Information
AI Technical Summary
Problems solved by technology
Method used
Image
Examples
Embodiment 1
[0036] Preparation of modified epoxy resin:
[0037] S1. Under the protection of nitrogen, add 100g of bisphenol A and 300g of epichlorohydrin into the reaction flask, heat to 80°C under stirring, add 1g of tetrabutylammonium bromide, and react for 5h. After the reaction is over, distill under reduced pressure to remove excess Epichlorohydrin, intermediate one;
[0038] S2. Under the protection of nitrogen, add Intermediate 1 and 1.5L of toluene into the reaction flask, heat to 80°C under stirring, add sodium hydroxide, and react for 3 hours to obtain Solution 1;
[0039] S3. Add 100g of bisphenol A to solution 1, heat to 80°C, react for 3 hours, cool the reaction solution to room temperature, add disodium hydrogen phosphate to adjust the pH to 6-7, filter, and wash the filtrate with deionized water for 3 Second, the toluene is removed by organic phase decompression distillation to obtain bisphenol A epoxy resin;
[0040] S4. Under the protection of nitrogen, dissolve 50g of...
Embodiment 2
[0043] Preparation of modified epoxy resin:
[0044] S1. Under the protection of nitrogen, add 100g of bisphenol A and 350g of epichlorohydrin into the reaction flask, heat to 80°C under stirring, add 1g of tetrabutylammonium bromide, and react for 5h. After the reaction is over, distill under reduced pressure to remove excess Epichlorohydrin, intermediate one;
[0045] S2. Under the protection of nitrogen, add Intermediate 1 and 1.5L of toluene into the reaction flask, heat to 80°C under stirring, add sodium hydroxide, and react for 3 hours to obtain Solution 1;
[0046] S3. Add 100g of bisphenol A to solution 1, heat to 80°C, react for 3 hours, cool the reaction solution to room temperature, add disodium hydrogen phosphate to adjust the pH to 6-7, filter, and wash the filtrate with deionized water for 3 Second, the toluene is removed by organic phase decompression distillation to obtain bisphenol A epoxy resin;
[0047] S4. Under the protection of nitrogen, dissolve 50g of...
Embodiment 3
[0050] Preparation of modified epoxy resin:
[0051] S1. Under the protection of nitrogen, add 80g of bisphenol A and 300g of epichlorohydrin into the reaction flask, heat to 80°C under stirring, add 1g of tetrabutylammonium bromide, and react for 5h. After the reaction, the excess is distilled off under reduced pressure. Epichlorohydrin, intermediate one;
[0052] S2. Under the protection of nitrogen, add Intermediate 1 and 1.5L of toluene into the reaction flask, heat to 80°C under stirring, add sodium hydroxide, and react for 3 hours to obtain Solution 1;
[0053] S3. Add 80g of bisphenol A to solution 1, heat to 80°C, react for 3 hours, cool the reaction solution to room temperature, add disodium hydrogen phosphate to adjust the pH to 6-7, filter, and wash the filtrate with deionized water for 3 Second, the toluene is removed by organic phase decompression distillation to obtain bisphenol A epoxy resin;
[0054] S4. Under nitrogen protection, dissolve 50g of hexafluorobu...
PUM
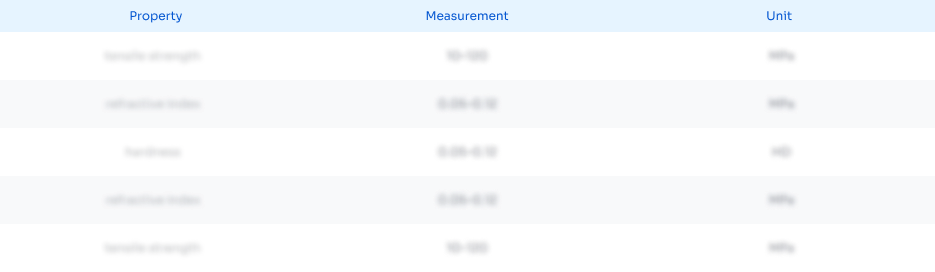
Abstract
Description
Claims
Application Information

- Generate Ideas
- Intellectual Property
- Life Sciences
- Materials
- Tech Scout
- Unparalleled Data Quality
- Higher Quality Content
- 60% Fewer Hallucinations
Browse by: Latest US Patents, China's latest patents, Technical Efficacy Thesaurus, Application Domain, Technology Topic, Popular Technical Reports.
© 2025 PatSnap. All rights reserved.Legal|Privacy policy|Modern Slavery Act Transparency Statement|Sitemap|About US| Contact US: help@patsnap.com