Anti-stick mucilage resin and preparation method thereof
An anti-stick and glue technology, which is applied in the field of anti-stick glue resin and its preparation, can solve the problems of difficulty in ensuring the use effect, and the performance of the glue resin is difficult to be reflected, and achieves the effect of improving the anti-stick properties.
- Summary
- Abstract
- Description
- Claims
- Application Information
AI Technical Summary
Problems solved by technology
Method used
Image
Examples
preparation example Construction
[0024] The preparation method of anti-adhesive mortar resin is:
[0025] (1), take each raw material respectively by above-mentioned mass percentage;
[0026] (2), dissolving: dissolve sodium lauryl sulfate with hot water, then cool;
[0027] (3) Pre-emulsification: Combine cooled sodium lauryl sulfate, styrene, butyl acrylate, acrylic acid, N-methylol acrylamide, vinyl triethoxysilane coupling agent, nonionic emulsifier 1. Water and vinyl silicone oil accounting for 90% of the total amount are sequentially added to the disperser to disperse, and after the dispersion is complete, a pre-emulsion is made;
[0028] (4), initiator: ammonium persulfate is mixed with water accounting for 5% of the total amount to form an initiator;
[0029] (5), initial addition: after the temperature of the reactor reaches 75°C, start to initially add 5 to 10% of the initiator and the initial addition of 5 to 10% of the pre-emulsion to the reactor;
[0030] (6) Dropping: After the reaction is st...
Embodiment 1
[0038] The cooled 2.5g sodium lauryl sulfate, 110g styrene, 270g butyl acrylate, 3g acrylic acid, 2g N-methylolacrylamide, 2g vinyltriethoxysilane coupling agent, 6g nonionic emulsifier Add 250g of water and 5g of vinyl silicone oil to the disperser in order to disperse. After the dispersion is complete, a pre-emulsion is made; after the temperature of the reactor reaches 75°C, start to add 10% of 0.5g ammonium persulfate to the reactor. The initiator made with 13g of water and the initial 10% pre-emulsion, after the reaction is stable, start to drop the pre-emulsion and the dropwise addition of the initiator. During the dropping process, the temperature is controlled at 85°C, kept for 1 hour, and then cooled to 50-60°C, then drop in 0.3g tert-butyl hydroperoxide, 0.3g sodium bisulfite and 14g water, keep warm for 20 minutes, then lower the temperature to below 45°C, adjust the pH value of the glue resin with ammonia water to adjust to 7.0±0.5, the product is obtained.
Embodiment 2
[0040] The cooled 2.5g sodium lauryl sulfate, 110g styrene, 270g butyl acrylate, 3g acrylic acid, 2g N-methylolacrylamide, 2g vinyltriethoxysilane coupling agent, 6g nonionic emulsifier Add 250g of water and 10g of vinyl silicone oil to the disperser in order to disperse. After the dispersion is complete, a pre-emulsion is made; after the temperature of the reactor reaches 75°C, start to add 10% of 0.5g ammonium persulfate to the reactor. The initiator made with 13g of water and the initial 10% pre-emulsion, after the reaction is stable, start to drop the pre-emulsion and the dropwise addition of the initiator. During the dropping process, the temperature is controlled at 85°C, kept for 1 hour, and then cooled to 50-60°C, then drop in 0.3g tert-butyl hydroperoxide, 0.3g sodium bisulfite and 14g water, keep warm for 20 minutes, then lower the temperature to below 45°C, adjust the pH value of the glue resin with ammonia water to adjust to 7.0±0.5, the product is obtained.
PUM
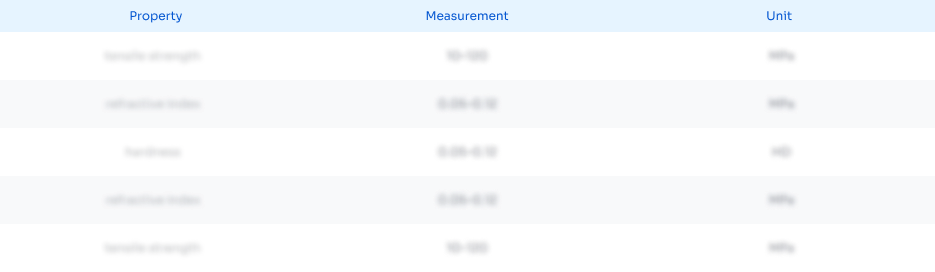
Abstract
Description
Claims
Application Information

- Generate Ideas
- Intellectual Property
- Life Sciences
- Materials
- Tech Scout
- Unparalleled Data Quality
- Higher Quality Content
- 60% Fewer Hallucinations
Browse by: Latest US Patents, China's latest patents, Technical Efficacy Thesaurus, Application Domain, Technology Topic, Popular Technical Reports.
© 2025 PatSnap. All rights reserved.Legal|Privacy policy|Modern Slavery Act Transparency Statement|Sitemap|About US| Contact US: help@patsnap.com