Laser strengthening technology for surface of steel rail of railway
A technology for surface strengthening and steel rails, which is applied in the field of laser surface strengthening technology, can solve the problems of reducing the bending strength and impact toughness fatigue strength of steel rails, affecting the operation efficiency and transportation safety, and the wear and tear of track curves, so as to achieve the reduction of fatigue strength, Improve stability, corrosion resistance and service life, and save fuel
- Summary
- Abstract
- Description
- Claims
- Application Information
AI Technical Summary
Problems solved by technology
Method used
Examples
Embodiment 1
[0041] A laser surface strengthening process for railway rails, comprising the following process steps:
[0042] (1) Use gasoline, alcohol or decontamination solvent to remove oil or rust on the surface of the rail, and then use sandpaper or an angle grinder to polish the surface of the rail to further remove dirt and polish;
[0043] (2) Carry out flaw detection inspection on rails by ultrasonic flaw detection method, and require that there are no cracks or spalling defects on the surface of the rails;
[0044] (3) Use the W-77 spray gun to mix the SiO2 with the adhesive 2 The light-absorbing paint is pre-prepared evenly on the surface of the rail, and dried naturally or with a fan to improve the resistance of the rail surface to CO 2 Laser absorption rate; the ratio of paint, thinner and adhesive is: 100gSiO 2 + 600ml alcohol + 10g paint flakes, the preset thickness is 30μm;
[0045] (4) Use broadband integrating mirror technology to transform the circular spot into a rec...
Embodiment 2
[0060] A laser surface strengthening process for railway rails, comprising the following process steps:
[0061] (1) Use gasoline, alcohol or decontamination solvent to remove oil or rust on the surface of the rail, and then use sandpaper or an angle grinder to polish the surface of the rail to further remove dirt and polish;
[0062] (2) Carry out flaw detection inspection on rails by ultrasonic flaw detection method, and require that there are no cracks or spalling defects on the surface of the rails;
[0063] (3) Use the W-77 spray gun to mix the SiO2 with the adhesive 2 The light-absorbing paint is pre-prepared evenly on the surface of the rail, and dried naturally or with a fan to improve the resistance of the rail surface to CO 2 Laser absorption rate; the ratio of paint, thinner and adhesive is: 125gSiO 2+ 700ml alcohol + 10g paint flakes, the preset thickness is 40μm;
[0064] (4) Use broadband integrating mirror technology to transform the circular spot into a rect...
Embodiment 3
[0079] A laser surface strengthening process for railway rails, comprising the following process steps:
[0080] (1) Use gasoline, alcohol or decontamination solvent to remove oil or rust on the surface of the rail, and then use sandpaper or an angle grinder to polish the surface of the rail to further remove dirt and polish;
[0081] (2) Carry out flaw detection inspection on rails by ultrasonic flaw detection method, and require that there are no cracks or spalling defects on the surface of the rails;
[0082] (3) Use the W-77 spray gun to mix the SiO2 with the adhesive 2 The light-absorbing paint is pre-prepared evenly on the surface of the rail, and dried naturally or with a fan to improve the resistance of the rail surface to CO 2 Laser absorption rate; the ratio of paint, thinner and adhesive is: 150gSiO 2 + 800ml alcohol + 10g paint flakes, the preset thickness is 50μm;
[0083] (4) Use broadband integrating mirror technology to transform the circular spot into a rec...
PUM
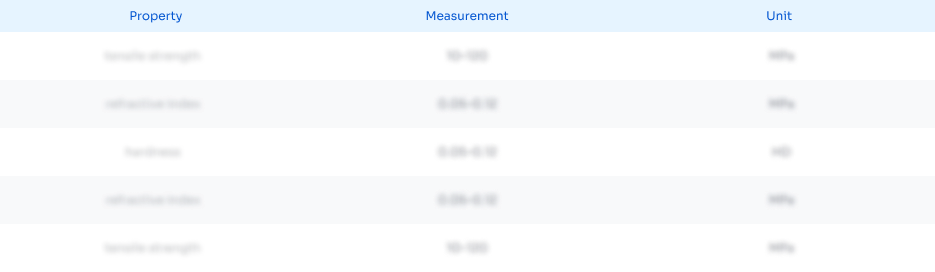
Abstract
Description
Claims
Application Information

- Generate Ideas
- Intellectual Property
- Life Sciences
- Materials
- Tech Scout
- Unparalleled Data Quality
- Higher Quality Content
- 60% Fewer Hallucinations
Browse by: Latest US Patents, China's latest patents, Technical Efficacy Thesaurus, Application Domain, Technology Topic, Popular Technical Reports.
© 2025 PatSnap. All rights reserved.Legal|Privacy policy|Modern Slavery Act Transparency Statement|Sitemap|About US| Contact US: help@patsnap.com