A method for comprehensive recovery of zinc and germanium from lead slag
A technology of lead slag and zinc germanium, applied in the direction of improving process efficiency, etc., can solve problems such as difficult practical production, lower germanium recovery rate, and large acid consumption, so as to improve economic and social benefits, improve germanium recovery rate, The effect of improving the quality of lead
- Summary
- Abstract
- Description
- Claims
- Application Information
AI Technical Summary
Problems solved by technology
Method used
Image
Examples
Embodiment 1
[0050] Take 20,000 grams of lead slag produced by a company in Yunnan and dry it for use. The lead slag contains 25.8% moisture, 16.5wt% zinc, 0.023wt% germanium, 13.6wt% lead, and 0.17wt% fluorine.
[0051] 1) Slurrying of lead slag: take 30 liters of industrial water, add 10,000 grams of lead slag for slurrying, the slurrying time is 10 minutes, stir and slurry evenly before use;
[0052] 2) Lead slag flotation: add 60.0 milliliters of 5% butyl xanthate aqueous solution to the ore pulp after stirring and slurrying evenly, and the dosage is 300 g / ton of butyl xanthate for lead slag; add 0.2 gram pinitol after stirring for 10 minutes Oil, pine alcohol oil with dosage of 20 grams / ton of lead slag; aeration for 2 minutes, scraping foam for flotation, output No. 1 concentrate and No. 1 tailings slurry;
[0053] 3) Dehydration of No. 1 concentrate: No. 1 concentrate is dehydrated through filtration I to obtain 3360 grams of No. 2 concentrate and 6.6 liters of No. 1 filtrate. No. ...
Embodiment 2
[0062] Take 20,000 grams of lead slag produced by a company in Yunnan and dry it for use. The lead slag contains 23.8% moisture, 11.4wt% zinc, 0.039wt% germanium, 17.6wt% lead, and 0.11wt% fluorine.
[0063] 1) Slurrying of lead slag: Take 40 liters of germanium sinking solution, add 10,000 grams of lead slag for slurrying, the slurrying time is 10 minutes, stir and slurry evenly before use. After sinking germanium, the liquid contains 4.2 g / L zinc, 0.006 g / L germanium, and 4.6 g / L fluorine;
[0064] 2) Lead slag flotation: add 80 milliliters of 5% butyl xanthate aqueous solution to the ore pulp after stirring and slurrying evenly, and the dosage is 400 g / ton of butyl xanthate for lead slag; add 0.25 gram pinitol after stirring for 10 minutes Oil, pine alcohol oil with dosage of 25 grams / ton of lead slag; aeration for 2 minutes, scraping foam and carrying out flotation to produce No. 1 concentrate and No. 1 tailings slurry;
[0065] 3) Dehydration of No. 1 concentrate: No. 1 ...
Embodiment 3
[0074] Take 20,000 grams of lead slag produced by a company in Yunnan and dry it for use. The lead slag contains 29.2% moisture, 18.6wt% zinc, 0.031wt% germanium, 16.4wt% lead, and 0.14wt% fluorine.
[0075] 1) Slurry of lead slag: Take 50 liters of germanium-sedimented liquid, add 10,000 grams of lead slag for slurrying, the slurrying time is 10 minutes, stir and slurry evenly before use. After sinking germanium, the solution contains 5.8 g / L of zinc, 0.0036 g / L of germanium, and 8.12 g / L of fluorine;
[0076] 2) Lead slag flotation: add 100 milliliters of 5% butyl xanthate aqueous solution to the ore pulp after stirring and pulping evenly, and the dosage is 500 g / ton of butyl xanthate for lead slag; add 0.3 gram pinitol after stirring for 10 minutes Oil, pine alcohol oil with dosage of 30 grams / ton of lead slag; aeration for 2 minutes, scraping foam and carrying out flotation to produce No. 1 concentrate and No. 1 tailings slurry;
[0077] 3) Dehydration of No. 1 concentrat...
PUM
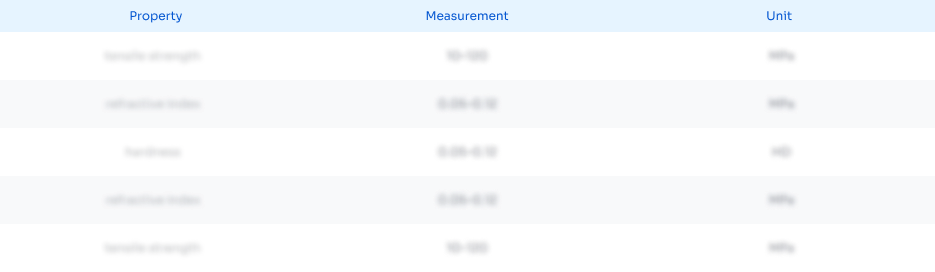
Abstract
Description
Claims
Application Information

- R&D
- Intellectual Property
- Life Sciences
- Materials
- Tech Scout
- Unparalleled Data Quality
- Higher Quality Content
- 60% Fewer Hallucinations
Browse by: Latest US Patents, China's latest patents, Technical Efficacy Thesaurus, Application Domain, Technology Topic, Popular Technical Reports.
© 2025 PatSnap. All rights reserved.Legal|Privacy policy|Modern Slavery Act Transparency Statement|Sitemap|About US| Contact US: help@patsnap.com