Method for recovering waste/used lithium iron phosphate positive-pole material by acid leaching method
A technology for recycling and processing lithium iron phosphate, which is applied in battery recycling, recycling technology, recycling by waste collectors, etc., can solve the problems that iron phosphate is easy to stay in the solid phase, unfavorable for leaching, and low recovery rate
- Summary
- Abstract
- Description
- Claims
- Application Information
AI Technical Summary
Problems solved by technology
Method used
Image
Examples
Embodiment 1
[0038] (1) Weigh 50 g of the positive electrode active material of the waste lithium iron phosphate battery, and add it into the sulfuric acid solution. According to the stoichiometric calculation of lithium in the raw material, the excess of sulfuric acid is 0%. The liquid-solid ratio was controlled to be 1.5:1, the leaching temperature was 25° C., and the leaching time was 30 minutes to obtain a suspension. The above suspension was filtered.
[0039] The waste lithium ion battery material processed in this step can be the waste lithium ion battery cathode material after pulverization and purification treatment.
[0040] (2) Oxidation of ferrous ions: adjust the pH of the filtrate to be less than 1, add hydrogen peroxide to oxidize the ferrous ions, the excess hydrogen peroxide is 50%, the oxidation temperature is 45° C., and react for 1 h.
[0041] (3) Lithium and iron phosphorus are separated to prepare iron phosphate: add LiOH to the reaction solution in step (2), adjust...
Embodiment 2
[0044] (1) Weigh the positive electrode active material 50 of the waste lithium iron phosphate battery and add it into the sulfuric acid solution. According to the stoichiometric calculation of lithium in the raw material, the excess of sulfuric acid is 0%. The liquid-solid ratio was controlled to be 1.5:1, the leaching temperature was 60° C., and the leaching time was 100 min to obtain a suspension. The above suspension was filtered.
[0045] The waste lithium ion battery material processed in this step can be the waste lithium ion battery cathode material after pulverization and purification treatment.
[0046] (2) Oxidation of ferrous ions: adjust the pH of the filtrate to be less than 1, add hydrogen peroxide to oxidize the ferrous ions, the excess hydrogen peroxide is 100%, the oxidation temperature is 45° C., and react for 5 hours.
[0047] (3) Lithium, iron and phosphorus are separated to prepare ferric phosphate: add LiOH to the reaction solution in step (2), adjust ...
Embodiment 3
[0050] (1) Weigh 50 g of the positive electrode active material of the waste lithium iron phosphate battery, and add it into the sulfuric acid solution. According to the stoichiometric calculation of lithium in the raw material, the excess of sulfuric acid is 100%. The liquid-solid ratio was controlled to be 2.5:1, the leaching temperature was 60° C., and the leaching time was 100 minutes to obtain a suspension. The above suspension was filtered.
[0051] The waste lithium ion battery material processed in this step can be the waste lithium ion battery cathode material after pulverization and purification treatment.
[0052] (2) Oxidation of ferrous ions: adjust the pH of the filtrate to be less than 1, add hydrogen peroxide to oxidize the ferrous ions, the excess hydrogen peroxide is 100%, the oxidation temperature is 45° C., and react for 2 hours.
[0053] (3) Lithium, iron and phosphorus are separated to prepare iron phosphate: add LiOH to the reaction solution in step (2...
PUM
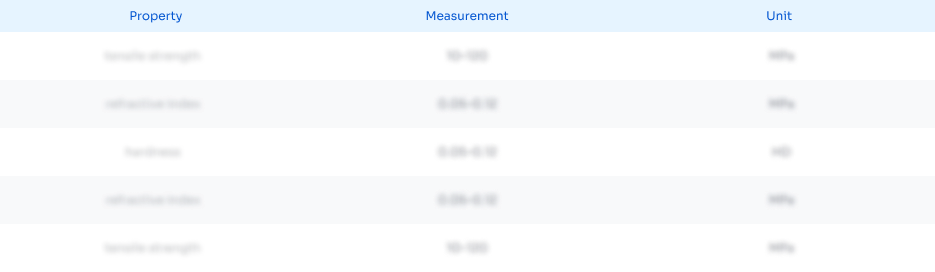
Abstract
Description
Claims
Application Information

- Generate Ideas
- Intellectual Property
- Life Sciences
- Materials
- Tech Scout
- Unparalleled Data Quality
- Higher Quality Content
- 60% Fewer Hallucinations
Browse by: Latest US Patents, China's latest patents, Technical Efficacy Thesaurus, Application Domain, Technology Topic, Popular Technical Reports.
© 2025 PatSnap. All rights reserved.Legal|Privacy policy|Modern Slavery Act Transparency Statement|Sitemap|About US| Contact US: help@patsnap.com