Continuous production process of beta-alanine
A production process, alanine technology, applied in the field of β-alanine, can solve problems such as large heat release, complicated operation, and flushing phenomenon, and achieve high mass transfer and heat transfer efficiency, high resource utilization, and avoid flushing The effect of material flying temperature
- Summary
- Abstract
- Description
- Claims
- Application Information
AI Technical Summary
Problems solved by technology
Method used
Image
Examples
Embodiment 1
[0027] β-aminopropionitrile and liquid caustic soda with a concentration of 22% are passed into the preheating pipeline with a mixing ratio of 1:2.3 (v / v) through metering pumps respectively, and β-aminopropionitrile and liquid caustic soda are respectively preheated to 80 ℃, then the raw material feed liquid enters the microchannel reactor for hydrolysis reaction, the microchannel reactor includes a star-shaped reactor and a pipeline reactor connected in sequence, the reaction temperature is 150 ℃, the reaction time is 90s, and the reaction pressure is 1.5MPa. After the completion, the reaction feed liquid containing β-alanine sodium, ammonia gas and a small amount of sodium hydroxide enters the high-temperature atmospheric tray distillation deammoniation system, and the ammonia gas drives the feed liquid self-circulation at a temperature of 105 ° C, while the ammonia gas Separated from the water vapor through the tray, the ammonia gas is recovered, and the water gas is return...
Embodiment 2
[0029] Adopt the production method of example 1, difference is that use concentration is the liquid caustic soda of 33%, the mixing ratio of β-aminopropionitrile and liquid caustic soda is 1:1.5 (v / v), 130 ℃ of reaction temperature, 40s of reaction time, reaction Pressure 1.0MPa. The product yield is 96%, and the product purity is 99.7%.
Embodiment 3
[0031] Adopting the production method of Example 1, the difference is that using a concentration of 40% liquid caustic soda, the mixing ratio of β-aminopropionitrile and liquid caustic soda is 1:1 (v / v), the reaction temperature is 100 ° C, the reaction time is 20s, and the reaction Pressure 0.2MPa. The product yield is 95.4%, and the product purity is 99.6%.
PUM
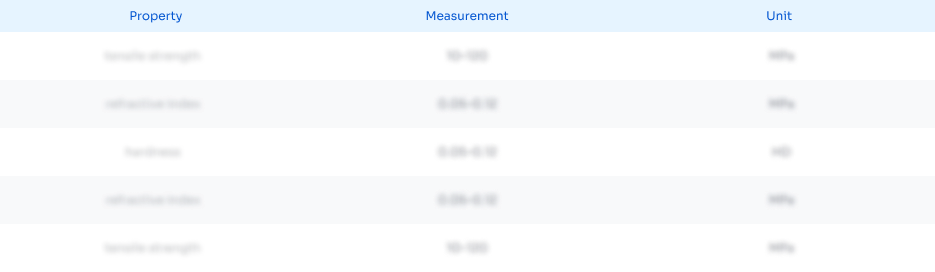
Abstract
Description
Claims
Application Information

- Generate Ideas
- Intellectual Property
- Life Sciences
- Materials
- Tech Scout
- Unparalleled Data Quality
- Higher Quality Content
- 60% Fewer Hallucinations
Browse by: Latest US Patents, China's latest patents, Technical Efficacy Thesaurus, Application Domain, Technology Topic, Popular Technical Reports.
© 2025 PatSnap. All rights reserved.Legal|Privacy policy|Modern Slavery Act Transparency Statement|Sitemap|About US| Contact US: help@patsnap.com