Production technology of novel cotton polyester denim
A production process, technology for denim, applied in liquid/gas/vapor yarn/filament processing, fiber type, final product manufacturing, etc., to solve problems such as unsmooth dyeing, damaged filament luster, and unsmooth dyeing , to reduce the amount of dye utilization, improve color fastness, reduce friction and stretching effect
- Summary
- Abstract
- Description
- Claims
- Application Information
AI Technical Summary
Problems solved by technology
Method used
Image
Examples
Embodiment 1
[0071] Embodiment 1: a kind of viscose filament:
[0072] The filaments in this application can be prepared using existing technologies. As an example but not a limitation, this embodiment provides a cellulose filament, the preparation process of which includes:
[0073] 1) Preparation of spinning solution: add the cleaned and dried waste viscose fabric crumbs to a certain amount of dimethylacetamide DMAc solvent, treat at 160°C for 30min under a nitrogen atmosphere, then cool to 100°C, add pre- Weighed LiCl, then stirred continuously at 80°C for 30min until the cellulose was completely dissolved; since the obtained cellulose solution contained impurities and air bubbles, a transparent cellulose solution was obtained through filtration and defoaming treatment, and the mass fraction of cellulose in it was is 3%, the mass fraction of LiCl is 8%;
[0074] 2) Spinning: feed the cellulose solution into the metering pump, adjust the extrusion parameters, and directly enter the coag...
Embodiment 2
[0075] Embodiment 2: a kind of filament denim:
[0076] First, this embodiment provides a color fixing agent solution composition, which is prepared by the following steps:
[0077] 1) Ultrasound-assisted and at a temperature of 55°C, slowly add an aqueous solution of iron salt dropwise to an aqueous solution of 1,10-phenanthroline, and stir for 25 minutes with ultrasonic assistance;
[0078] 2) Maintain the temperature in step 1), slowly add tannin solution to the mixed solution in step 1), adjust the pH to 5.2 with acetic acid solution after stirring for 30 minutes, and ultrasonically assist stirring for 60 minutes;
[0079] 3) The mixed solution in step 2) was cooled to room temperature, followed by adding carboxymethyl cellulose hydrogel and halogenated pyridyl ketone compound, stirring at room temperature and constant speed for 60 min, and adjusting the pH to 6.8 with formic acid solution.
[0080] The preparation steps of the above color-fixing agent solution compositio...
Embodiment 3
[0107] Example 3: Another filament denim:
[0108] This embodiment provides another kind of filament denim, its formula and preparation process are basically the same as in Example 2, the difference is that in this embodiment, when preparing the color fixing agent solution composition, the halogenation in step 3) The pyridyl ketone compound is the compound 2-chlorophenyl pyridyl ketone in the form of formula (1b); and the filament denim is prepared according to the process of Example 2 by using the filament described in Example 1.
PUM
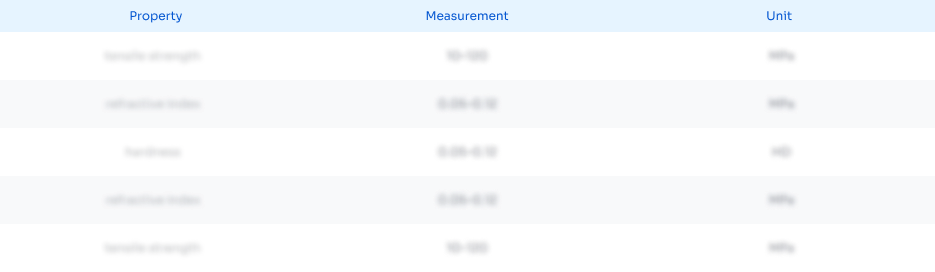
Abstract
Description
Claims
Application Information

- R&D Engineer
- R&D Manager
- IP Professional
- Industry Leading Data Capabilities
- Powerful AI technology
- Patent DNA Extraction
Browse by: Latest US Patents, China's latest patents, Technical Efficacy Thesaurus, Application Domain, Technology Topic, Popular Technical Reports.
© 2024 PatSnap. All rights reserved.Legal|Privacy policy|Modern Slavery Act Transparency Statement|Sitemap|About US| Contact US: help@patsnap.com