Spraying quick-setting waterproof coating for marine corrosion prevention and preparation method and construction method thereof
A marine anti-corrosion and waterproof coating technology, applied in the field of materials, can solve problems affecting the performance and appearance of buildings, moldy buildings, and affecting service life
- Summary
- Abstract
- Description
- Claims
- Application Information
AI Technical Summary
Problems solved by technology
Method used
Examples
Embodiment example 1
[0034] The spray quick-setting waterproof coating for marine anticorrosion is composed of A and B materials; among them, A material is composed of the following components: 70# emulsified asphalt 50Kg, neoprene latex 30kg, zinc oxide dispersion 8Kg, filler slurry 13Kg, sodium silicate aqueous solution 1Kg, anti-aging agent 2246 2Kg, anti-mold antibacterial agent zinc pyrithione 0.05Kg, silicone defoamer 0.2Kg;
[0035] Material B consists of the following components: calcium nitrate 11Kg, ethylene glycol 1Kg, alkyl polyoxyethylene ether 0.2Kg, deionized water 87.8Kg.
[0036] In the first embodiment, the zinc oxide dispersion liquid is composed of the following components: zinc oxide 50Kg, sodium bentonite 0.5Kg, sodium hydroxide 0.03Kg, sodium methylene dinaphthalene sulfonate 0.7Kg, organic silicon defoamer 0.4Kg , Deionized water 48.37Kg.
[0037] In the first embodiment, the filler slurry is composed of the following components: wollastonite 30Kg, kaolin 40Kg, sodium bent...
Embodiment example 2
[0050] In the second example, material A is composed of the following components: 40Kg of 90# emulsified asphalt, 30kg of neoprene latex, 20kg of pre-crosslinked styrene-butadiene latex, 12Kg of zinc oxide dispersion, 5Kg of filler slurry, 2Kg of sodium silicate aqueous solution, anti-aging Agent 2246 1.5Kg, anti-mold antibacterial agent zinc pyrithione 0.07Kg, silicone defoamer 0.2Kg;
[0051] Material B consists of the following components: calcium acetate 13Kg, ethylene glycol 3Kg, alkyl polyoxyethylene ether 0.3Kg, deionized water 83.7Kg.
[0052] In the second embodiment, the zinc oxide dispersion liquid is composed of the following components: zinc oxide 60Kg, sodium bentonite 1.2Kg, sodium hydroxide 0.04Kg, sodium methylene dinaphthalene sulfonate 1.2Kg, silicone defoamer 0.4Kg , Deionized water 37.16Kg.
[0053] In the second embodiment, the filler slurry is composed of the following components: calcium carbonate 73g, kaolin 5Kg, sodium bentonite 0.5Kg, sodium hydroxi...
Embodiment example 3
[0055] In this embodiment three, material A consists of the following components: 90# emulsified asphalt 50Kg, pre-crosslinked chloroprene latex 25kg, styrene-butadiene latex 10kg, zinc oxide dispersion 8Kg, filler slurry 12Kg, sodium silicate aqueous solution 1.5Kg, Anti-aging agent 2246 2Kg, anti-mold antibacterial agent pyrithione zinc 0.05Kg, silicone defoamer 0.15Kg;
[0056] Material B consists of the following components: barium nitrate 10Kg, aluminum nitrate 5Kg, ethylene glycol 4.5Kg, alkyl polyoxyethylene ether 0.5Kg, deionized water 80Kg.
[0057] In the third example, the zinc oxide dispersion liquid is composed of the following components: zinc oxide 55Kg, sodium bentonite 1.0Kg, sodium hydroxide 0.03Kg, sodium methylene dinaphthalene sulfonate 1.0Kg, silicone defoamer 0.3Kg , Deionized water 42.67Kg.
[0058] In the third example, the filler slurry is composed of the following components: calcium carbonate 60g, mica powder 10Kg, sodium bentonite 1.0Kg, sodium hy...
PUM
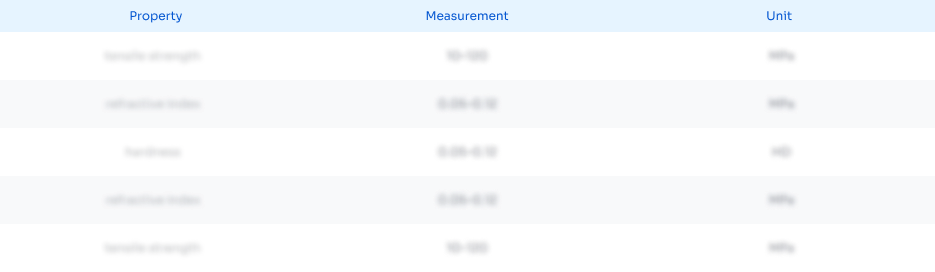
Abstract
Description
Claims
Application Information

- R&D
- Intellectual Property
- Life Sciences
- Materials
- Tech Scout
- Unparalleled Data Quality
- Higher Quality Content
- 60% Fewer Hallucinations
Browse by: Latest US Patents, China's latest patents, Technical Efficacy Thesaurus, Application Domain, Technology Topic, Popular Technical Reports.
© 2025 PatSnap. All rights reserved.Legal|Privacy policy|Modern Slavery Act Transparency Statement|Sitemap|About US| Contact US: help@patsnap.com