High-antifriction iron-based sulfide powder metallurgy oil-containing bearing material as well as preparation method and application thereof
A vulcanized powder and bearing material technology, applied in bearings, bearing components, shafts and bearings, etc., can solve the problems of high production cost, reduced service life of sliding bearings and shafts, friction coefficient sliding bearings and shaft wear and burns, etc., to achieve Effect of reducing the coefficient of friction and improving the anti-friction effect
- Summary
- Abstract
- Description
- Claims
- Application Information
AI Technical Summary
Problems solved by technology
Method used
Image
Examples
Embodiment 1
[0023] (1) Take 18.0% copper, 0.60% carbon, 0.8% tungsten, 0.6% chromium, 0.8% molybdenum, 0.8% nickel, 0.8% vanadium by weight, and the balance is iron Fe, and use a double cone mixer to mix , mixed evenly and pressed to obtain a pressed density of 6.6g / cm 3 The disc sample; then place it at a temperature of 1110°C for sintering for 40 minutes to prepare a sintered material;
[0024] (2) Sulfur coating: the sulfur is dispersed into powder by sieving, and the sulfur powder is weighed and evenly sprayed on the surface of the sintered material to obtain the coated material; the amount of sulfur accounts for about 0.08% by weight of the sintered material;
[0025] (3) Vulcanization process: In a nitrogen atmosphere, place the coating material at a temperature of 120°C and keep it warm for 120 minutes. Since this temperature is higher than the melting point of sulfur, the sulfur is in a molten state and can enter the pores of the sintered material and enter the sintered material. ...
Embodiment 2
[0027] (1) Take 20.0% copper, 0.75% carbon, 1.6% tungsten, 1.2% chromium, 1.6% molybdenum, 1.6% nickel, 1.6% vanadium by weight, and the balance is iron Fe, and mix with a double cone mixer , mixed evenly and pressed to obtain a pressed density of 6.3g / cm 3 The disc sample; then place it at a temperature of 1120°C for sintering for 40 minutes to prepare a sintered material;
[0028] (2) Sulfur coating: the sulfur is dispersed into powder by sieving, and the sulfur powder is weighed and evenly sprayed on the surface of the sintered material to obtain the coating material; the amount of sulfur accounts for about 0.60% of the weight of the sintered material;
[0029] (3) Vulcanization process: In a nitrogen atmosphere, place the coating material at a temperature of 140°C and keep it warm for 60 minutes. Since this temperature is higher than the melting point of sulfur, the sulfur is in a molten state and can enter the pores of the sintered material and enter the sintered material...
Embodiment 3
[0031] (1) Take 20.0% copper, 0.9% carbon, 2.0% tungsten, 1.8% chromium, 2.6% molybdenum, 3% nickel, 1.8% vanadium by weight, and the balance is iron Fe, and use a double cone mixer to mix , mixed evenly and pressed to obtain a pressed density of 6g / cm 3 The disc sample; then place it at a temperature of 1110°C for sintering for 40 minutes to prepare a sintered material;
[0032] (2) Sulfur coating: the sulfur is dispersed into powder by sieving, and the sulfur powder is weighed and evenly sprayed on the surface of the sintered material to obtain the coating material; the amount of sulfur accounts for about 0.80% of the weight of the sintered material;
[0033] (3) Vulcanization process: In a nitrogen atmosphere, place the coating material at a temperature of 150°C and keep it warm for 30 minutes. Since this temperature is higher than the melting point of sulfur, the sulfur is in a molten state and can enter the pores of the sintered material and enter the sintered material. ...
PUM
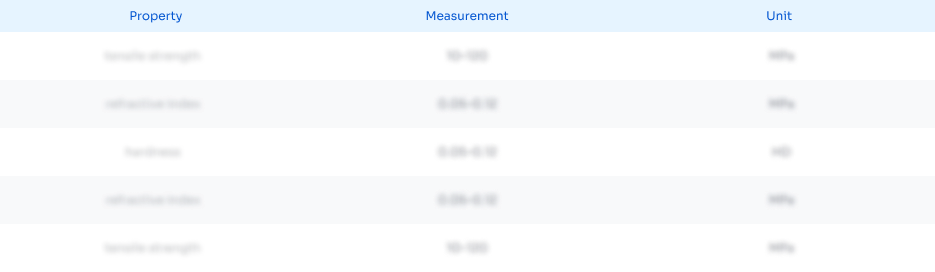
Abstract
Description
Claims
Application Information

- R&D Engineer
- R&D Manager
- IP Professional
- Industry Leading Data Capabilities
- Powerful AI technology
- Patent DNA Extraction
Browse by: Latest US Patents, China's latest patents, Technical Efficacy Thesaurus, Application Domain, Technology Topic, Popular Technical Reports.
© 2024 PatSnap. All rights reserved.Legal|Privacy policy|Modern Slavery Act Transparency Statement|Sitemap|About US| Contact US: help@patsnap.com