Preparation method of polyolefin-based composite material
An olefin-based composite material and polyolefin technology, applied in the field of polymer material preparation, can solve the problems of increased purification treatment, time-consuming, poor uniformity of composite materials, etc., achieve thermal deformation temperature and elongation at break improvement, avoid purification treatment, The effect of stable performance
- Summary
- Abstract
- Description
- Claims
- Application Information
AI Technical Summary
Problems solved by technology
Method used
Examples
Embodiment 1
[0022] A preparation method of a polyolefin-based composite material: 1 weight part of ethylene-vinyl acetate copolymer is dissolved in 25 weight parts of liquid silane coupling agent KH-550 through a paddle stirrer at 120 ° C, and then Add the carbon nanotube of 0.15 weight part, stir and mix, turn over to vacuum filtration device and solid and liquid are separated, the solid that separation obtains is put into internal mixer, the additive paraffin / calcium carbonate mixture of adding 0.06 weight part wherein, in Melting and preforming at 110°C, followed by hot pressing; wherein, the mass ratio of paraffin wax to calcium carbonate in the paraffin wax / calcium carbonate mixture is 2:1.
Embodiment 2
[0024] A preparation method of a polyolefin-based composite material: 1 weight part of low-density polyethylene is dissolved in 30 weight parts of liquid titanate coupling agent NDZ-201 by a magnetic stirrer at 120 ° C, and then Add 0.2 parts by weight of graphene, stir and mix, transfer to an evaporation recovery device to separate the solid from the liquid, put the separated solid into an extruder, add 0.05 parts by weight of polyethylene wax as an additive, and melt at 130°C Preformed and then injection molded.
Embodiment 3
[0026] A preparation method of a polyolefin-based composite material: 1 part by weight of homopolypropylene is dissolved in 35 parts by weight of liquid dioctyl phthalate at 160 °C with a vibrating agitator, and then 0.06 The graphite of parts by weight is stirred and mixed, and is transferred to a mechanical filter press device to separate solids and liquids, and the solids obtained by separation are dropped into an open mill, and the mixture of additive polyethylene wax / ammonium polyphosphate of 0.05 parts by weight is added thereto. Melting and preforming at 150°C, followed by hot pressing and cutting; wherein, the mass ratio of polyethylene wax to ammonium polyphosphate in the polyethylene wax / ammonium polyphosphate mixture is 4:1.
PUM
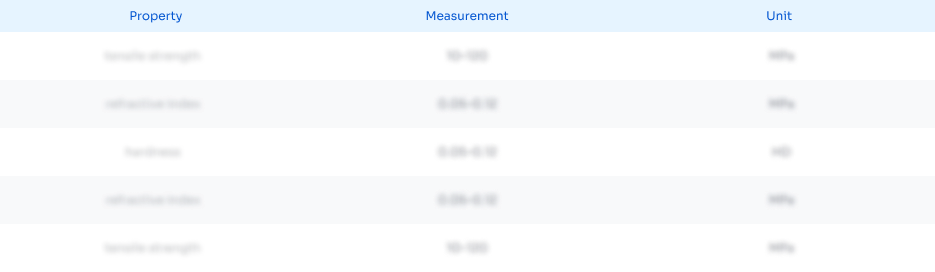
Abstract
Description
Claims
Application Information

- Generate Ideas
- Intellectual Property
- Life Sciences
- Materials
- Tech Scout
- Unparalleled Data Quality
- Higher Quality Content
- 60% Fewer Hallucinations
Browse by: Latest US Patents, China's latest patents, Technical Efficacy Thesaurus, Application Domain, Technology Topic, Popular Technical Reports.
© 2025 PatSnap. All rights reserved.Legal|Privacy policy|Modern Slavery Act Transparency Statement|Sitemap|About US| Contact US: help@patsnap.com