Method for preparing fuel cell metal bipolar plate flow field through electrochemical etching
A metal bipolar plate and fuel cell technology, applied in fuel cells, electrochemical generators, circuits, etc., can solve problems such as stress corrosion, low processing efficiency, and residual stress of metal plate deformation, so as to improve corrosion resistance and facilitate Process, improve the effect of water management
- Summary
- Abstract
- Description
- Claims
- Application Information
AI Technical Summary
Problems solved by technology
Method used
Image
Examples
Embodiment example 1
[0025] (1) Experimental pretreatment The experiment selected 316 stainless steel plate of 69*127*1mm as the base material. First, the stainless steel plate was immersed in sodium hydroxide solution for ultrasonic treatment to achieve surface degreasing. After the ultrasonic treatment was completed, the stainless steel plate taken out was deionized Wash with water. (2) Make the anti-corrosion layer. Apply the photosensitive ink evenly on the surface of the stainless steel plate through a scraper coater to ensure uniformity, no bubbles, and no leaks. Bake at 80C for 60 minutes. Paste the printed film on the photosensitive ink, use an 8W iodine-gallium lamp with a lamp distance of 5cm, expose for 5 minutes, and develop with a pre-configured 1% sodium carbonate developer to obtain the desired pattern. Then bake at 155°C for 60 minutes. (3) Electrochemical etching Prepare an electrolyte solution of 16% sodium nitrate, 2% citric acid, 6 mL / l ethylene glycol, and 0.18 g / L saccharin...
Embodiment example 2
[0027] (1) Experimental pretreatment The experiment uses 316 stainless steel plate of 69*127*1mm as the base material. First, immerse the stainless steel plate in sodium hydroxide solution for ultrasonic treatment to achieve surface degreasing. After the ultrasonic treatment is completed, use oxalic acid solution Wash to remove residual lye, and finally wash with deionized water. Observe the surface of the stainless steel plate. If a uniform liquid film is formed on the surface, the degreasing effect is good, otherwise repeat the previous steps. (2) Make the anti-corrosion layer. Apply the photosensitive ink evenly on the surface of the stainless steel plate through a scraper coater to ensure uniformity, no bubbles, and no leaks. Bake at 80 degrees Celsius for 20 minutes. Paste the printed film on the photosensitive ink, use an 8W iodine-gallium lamp with a lamp distance of 5cm, expose for 5 minutes, and develop with a pre-configured 1% sodium carbonate developer to obtain the...
Embodiment example 3
[0029] (1) Experimental pretreatment The experiment uses 316 stainless steel plate of 69*127*1mm as the base material. First, immerse the stainless steel plate in sodium hydroxide solution for ultrasonic treatment to achieve surface degreasing. After the ultrasonic treatment is completed, use oxalic acid solution Wash to remove residual lye, and finally wash with deionized water. Observe the surface of the stainless steel plate. If a uniform liquid film is formed on the surface, the degreasing effect is good, otherwise repeat the previous steps. (2) Make the anti-corrosion layer. Apply the photosensitive ink evenly on the surface of the stainless steel plate through a scraper coater to ensure uniformity, no bubbles, and no leaks. Bake at 80 degrees Celsius for 20 minutes. Paste the printed film on the photosensitive ink, use an 8W iodine-gallium lamp with a lamp distance of 5cm, expose for 5 minutes, and develop with a pre-configured 1% sodium carbonate developer to obtain the...
PUM
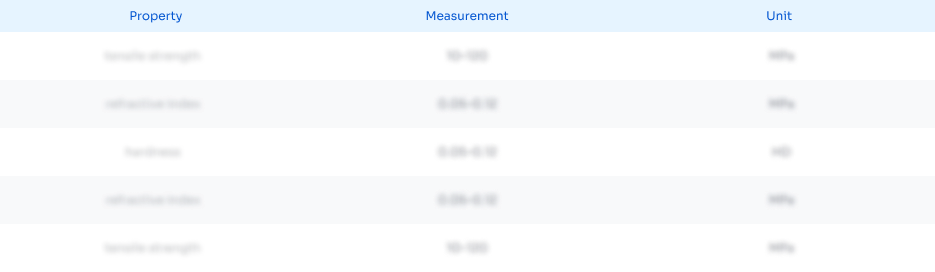
Abstract
Description
Claims
Application Information

- R&D
- Intellectual Property
- Life Sciences
- Materials
- Tech Scout
- Unparalleled Data Quality
- Higher Quality Content
- 60% Fewer Hallucinations
Browse by: Latest US Patents, China's latest patents, Technical Efficacy Thesaurus, Application Domain, Technology Topic, Popular Technical Reports.
© 2025 PatSnap. All rights reserved.Legal|Privacy policy|Modern Slavery Act Transparency Statement|Sitemap|About US| Contact US: help@patsnap.com