Corrugated paperboard and corrugated carton production process
A corrugated cardboard and corrugated paper technology, which is applied to paper/cardboard layered products, paper/cardboard containers, papermaking, etc., can solve the problems of ineffective flame retardancy and fire prevention, poor moisture and water resistance, and poor compressive strength of corrugated cartons. Sufficient effect of shock absorption performance utilization
- Summary
- Abstract
- Description
- Claims
- Application Information
AI Technical Summary
Problems solved by technology
Method used
Image
Examples
Embodiment 1
[0065] The flame retardant glue includes the following components in parts by weight: 26 parts of cationic starch, 0.8 part of caustic soda, 0.3 part of borax, 22 parts of micropowdered silica gel, 13 parts of reinforcing resin, 3 parts of terpene resin, 2 parts of melamine, polyamide 3 parts of imine, 4 parts of formaldehyde, 0.8 part of antioxidant, 1.2 parts of emulsifier, 0.1 part of coupling agent, 1.2 parts of water quality stabilizer, 1.2 parts of bridging agent, 0.5 part of aluminum sulfate, 0.5 part of polyethylene oxide and water ; The content of the water is 50% of the total weight of all components.
[0066] The preparation steps of the flame retardant glue are as follows:
[0067] 1) Add micropowder silica gel, terpene resin, antioxidant, caustic soda and 20% water into No. 1 mixing cylinder and stir and mix. The mixing temperature is 18°C. After stirring for 20 minutes, heat up to 10°C / min. 60°C, stir for 10 minutes and then cool to room temperature to form No. ...
Embodiment 2
[0084] The flame retardant glue includes the following components in parts by weight: 32 parts of cationic starch, 2.0 parts of caustic soda, 0.5 parts of borax, 42 parts of micropowdered silica gel, 23 parts of reinforcing resin, 8 parts of terpene resin, 10 parts of melamine, polyamide 11 parts of imine, 10 parts of formaldehyde, 4.8 parts of antioxidant, 5.2 parts of emulsifier, 0.2 part of coupling agent, 1.8 parts of water quality stabilizer, 1.8 parts of bridging agent, 1 part of aluminum sulfate, 1 part of polyethylene oxide and water ; The content of the water is 50% of the total weight of all components.
[0085] Further, the preparation steps of the flame retardant glue are as follows:
[0086] 1) Add micropowder silica gel, terpene resin, antioxidant, caustic soda and 20% water into No. 1 mixing cylinder and stir and mix. The mixing temperature is 45°C. After stirring for 20 minutes, heat up to 10°C / min. 60°C, stir for 10 minutes and then cool to room temperature t...
Embodiment 3
[0094] The flame retardant glue includes the following components in parts by weight: 29 parts of cationic starch, 1.4 parts of caustic soda, 0.4 parts of borax, 33 parts of micropowder silica gel, 18 parts of reinforcing resin, 5 parts of terpene resin, 6 parts of melamine, polyamide 7 parts of imine, 7 parts of formaldehyde, 2.8 parts of antioxidant, 3.1 parts of emulsifier, 0.15 part of coupling agent, 1.5 parts of water quality stabilizer, 1.5 parts of bridging agent, 0.7 part of aluminum sulfate, 0.7 part of polyethylene oxide and water ; The content of the water is 50% of the total weight of all components.
[0095] The preparation steps of the flame retardant glue are as follows:
[0096] 1) Add micropowder silica gel, terpene resin, antioxidant, caustic soda and 20% water into No. 1 mixing cylinder and stir and mix. The mixing temperature is 30°C. After stirring for 20 minutes, heat up to 10°C / min. 60°C, stir for 10 minutes and then cool to room temperature to form No...
PUM
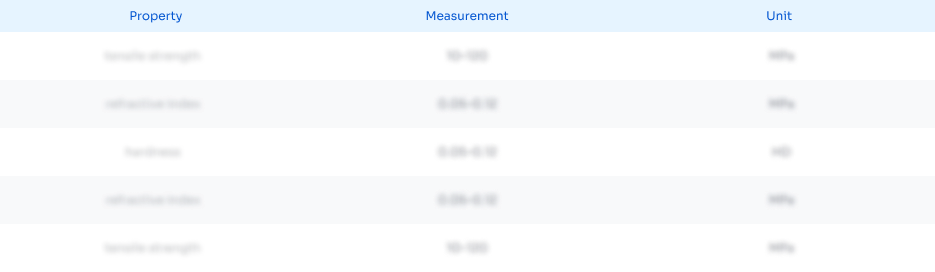
Abstract
Description
Claims
Application Information

- R&D Engineer
- R&D Manager
- IP Professional
- Industry Leading Data Capabilities
- Powerful AI technology
- Patent DNA Extraction
Browse by: Latest US Patents, China's latest patents, Technical Efficacy Thesaurus, Application Domain, Technology Topic, Popular Technical Reports.
© 2024 PatSnap. All rights reserved.Legal|Privacy policy|Modern Slavery Act Transparency Statement|Sitemap|About US| Contact US: help@patsnap.com