Zirconium nitride aluminum/aluminium oxide composite coating firmly combined with hard alloy and preparation method thereof
A technology with strong combination and zirconium-aluminum nitride, which is applied in metal material coating process, coating, ion implantation plating, etc., can solve the problems of insufficient energy, obstruction, and low deposition temperature, so as to avoid low hardness and solve the problem of bonding The effect of low strength and high toughness
- Summary
- Abstract
- Description
- Claims
- Application Information
AI Technical Summary
Problems solved by technology
Method used
Examples
Embodiment 1
[0026] Put the clean cemented carbide substrate into the vacuum chamber of the plasma-enhanced compound ion coating system, and when the vacuum of the back is evacuated to 0.05Pa, turn on the auxiliary heating device on the furnace wall to heat the substrate, and turn on the rotating power supply at the same time to make the substrate Rotate continuously, heat until the substrate temperature reaches 380°C; then pass argon gas into the vacuum chamber, adjust the flow rate of argon gas to ensure the pressure is 0.2Pa, and then apply a DC bias voltage of -200V and a pulse bias voltage of -400V to the substrate , using the ionized Ar + Etch the surface of the substrate for 80 minutes; turn off the bias voltage of the substrate in turn, adjust the flow of argon gas to ensure that the working pressure is 0.15Pa, turn on the main arc power supply of evaporation plating for evaporation coating, the main arc current on the crucible is 180A, and evaporate the raw material for Co 0.15 N...
Embodiment 2
[0028] Put the clean cemented carbide substrate into the vacuum chamber of the plasma-enhanced composite ion coating system, and when the vacuum of the back is evacuated to 0.05Pa, turn on the auxiliary heating device on the furnace wall to heat the substrate, and at the same time turn on the rotating power to make the substrate Rotate continuously, heat until the substrate temperature reaches 380°C; then pass argon gas into the vacuum chamber, adjust the flow rate of argon gas to ensure the pressure is 0.15Pa, and then apply a DC bias voltage of -200V and a pulse bias voltage of -300V to the substrate , using the ionized Ar + Etch the surface of the substrate for 30 minutes; turn off the bias voltage of the substrate in turn, adjust the flow of argon to ensure that the working pressure is 0.2Pa, turn on the main arc power supply of evaporation plating for evaporation coating, the main arc current on the crucible is 220A, and evaporate the raw material for Co 0.2 Ni 0.2 Cr ...
Embodiment 3
[0030] Put the clean cemented carbide substrate into the vacuum chamber of the plasma-enhanced composite ion coating system, and when the vacuum of the back is evacuated to 0.05Pa, turn on the auxiliary heating device on the furnace wall to heat the substrate, and at the same time turn on the rotating power to make the substrate Rotate continuously, heat until the substrate temperature reaches 380°C; then pass argon gas into the vacuum chamber, adjust the flow rate of argon gas to ensure the pressure is 0.15Pa, and then apply a DC bias of -100V and a pulse bias of -200V to the substrate , using the ionized Ar + Etch the surface of the substrate for 90 minutes; turn off the bias voltage of the substrate in turn, adjust the flow of argon to ensure that the working pressure is 0.2Pa, turn on the main arc power supply of evaporation plating for evaporation coating, the main arc current on the crucible is 205A, and evaporate the raw material for Co 0.2 Ni 0.2 Cr 0.2 al 0.2 Y 0...
PUM
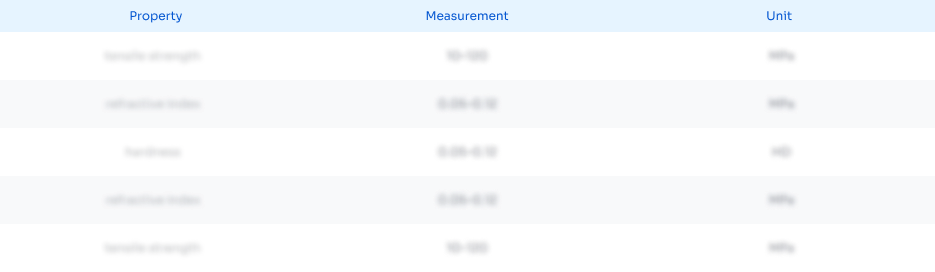
Abstract
Description
Claims
Application Information

- R&D Engineer
- R&D Manager
- IP Professional
- Industry Leading Data Capabilities
- Powerful AI technology
- Patent DNA Extraction
Browse by: Latest US Patents, China's latest patents, Technical Efficacy Thesaurus, Application Domain, Technology Topic, Popular Technical Reports.
© 2024 PatSnap. All rights reserved.Legal|Privacy policy|Modern Slavery Act Transparency Statement|Sitemap|About US| Contact US: help@patsnap.com