Preparation method of VN@Co electrocatalyst
An electrocatalyst, cobalt chloride hexahydrate technology, applied in chemical instruments and methods, physical/chemical process catalysts, electrodes, etc., can solve the problem of reducing electrochemical specific surface area and catalytic effect, unsuitable for large-scale industrial production, nitrogen The catalytic activity of vanadium is not high, and the effect of long service life, long life and small overpotential is achieved.
- Summary
- Abstract
- Description
- Claims
- Application Information
AI Technical Summary
Problems solved by technology
Method used
Image
Examples
Embodiment 1
[0023] 1) The raw materials of urea, ammonium metavanadate, cobalt chloride hexahydrate, and sodium hypophosphite are batched according to the following mass composition ratio: CH 4 N 2 O: NH 4 VO 3 :CoCl 2 *6H 2 O:NaH 2 PO 2 =8:1:1:6;
[0024] 2) After mixing the urea, ammonium metavanadate and cobalt chloride hexahydrate after step 1 proportioning, the grinding time is 20min, after grinding, the mixture is passed through a 60-mesh sieve, and the mixture with larger particle size is screened out. Put the ground mixture into a small porcelain boat, place the small porcelain boat at one end of the large porcelain boat, add the sodium hypophosphite after step 1 ratio to the other end of the large porcelain boat, and place the large porcelain boat in a tubular atmosphere In the furnace, connect one end of the tubular atmosphere furnace containing sodium hypophosphite to the air inlet, and add two furnace plugs at both ends of the tubular atmosphere furnace;
[0025] 3) Pa...
Embodiment 2
[0028] 1) The raw materials of urea, ammonium metavanadate, cobalt chloride hexahydrate, and sodium hypophosphite are batched according to the following mass composition ratio: CH 4 N 2 O: NH 4 VO 3 :CoCl 2 *6H 2 O:NaH 2 PO 2 =9:2:2:7;
[0029] 2) After mixing the urea, ammonium metavanadate, and cobalt chloride hexahydrate after the proportioning of step 1, grind the mixture for 25 minutes, then pass the mixture through a 60-mesh sieve after grinding, and sieve out the mixture with larger particle size. Put the ground mixture into a small porcelain boat, place the small porcelain boat at one end of the large porcelain boat, add the sodium hypophosphite after step 1 ratio to the other end of the large porcelain boat, and place the large porcelain boat in a tubular atmosphere In the furnace, connect one end of the tubular atmosphere furnace containing sodium hypophosphite to the air inlet, and add two furnace plugs at both ends of the tubular atmosphere furnace;
[0030...
Embodiment 3
[0033] 1) The raw materials of urea, ammonium metavanadate, cobalt chloride hexahydrate, and sodium hypophosphite are batched according to the following mass composition ratio: CH 4 N 2 O: NH 4 VO 3 :CoCl 2 *6H 2 O:NaH 2 PO 2 =10:3:3:8;
[0034] 2) After mixing the urea, ammonium metavanadate, and cobalt chloride hexahydrate after the proportioning of step 1, grind the mixture for 28 minutes, and then pass the mixture through a 60-mesh sieve after grinding, and sieve out the mixture with larger particle size. Put the ground mixture into a small porcelain boat, place the small porcelain boat at one end of the large porcelain boat, add the sodium hypophosphite after the ratio in step 1 to the other end of the large porcelain boat, and place the large porcelain boat in a tubular atmosphere In the furnace, connect one end of the tubular atmosphere furnace containing sodium hypophosphite to the air inlet, and add two furnace plugs at both ends of the tubular atmosphere furna...
PUM
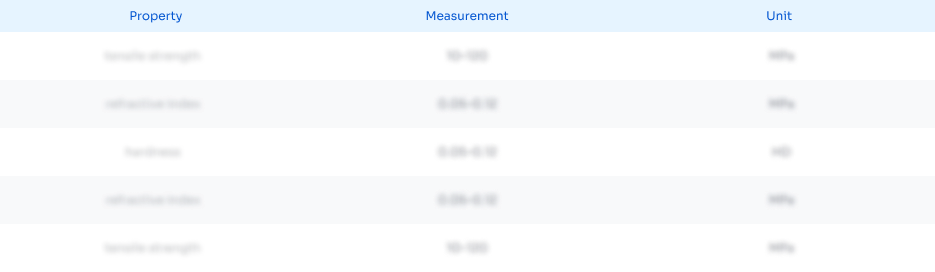
Abstract
Description
Claims
Application Information

- R&D
- Intellectual Property
- Life Sciences
- Materials
- Tech Scout
- Unparalleled Data Quality
- Higher Quality Content
- 60% Fewer Hallucinations
Browse by: Latest US Patents, China's latest patents, Technical Efficacy Thesaurus, Application Domain, Technology Topic, Popular Technical Reports.
© 2025 PatSnap. All rights reserved.Legal|Privacy policy|Modern Slavery Act Transparency Statement|Sitemap|About US| Contact US: help@patsnap.com