Method and device for continuously producing m-aminophenol
An aminophenol and production room technology, which is applied in the field of continuous production of m-aminophenol, can solve the problems of high requirements for workers' operating skills, difficult alkali-melting operation, and easy occurrence of flushing, etc., and achieves good heat transfer effect and avoids flushing. Temperature phenomenon, the effect of precise temperature control
- Summary
- Abstract
- Description
- Claims
- Application Information
AI Technical Summary
Problems solved by technology
Method used
Image
Examples
Embodiment 1
[0030] The schematic diagram of the production device for continuous production of m-aminophenol is as follows: figure 1 As shown, 360kg of sodium m-sulfamic acid (after conversion), 154kg of sodium hydroxide and 160kg of potassium hydroxide are sequentially put into the batching tank 1, stirred, and the temperature is raised to 250°C by feeding low-temperature heat transfer oil. Continuously discharge the material into the heating spiral pipe reactor 2, raise the temperature to 300°C, and the heating time is 1.0h. Then, the materials were continuously discharged into the thermal insulation spiral pipe reactor 3 by using a double auger, and kept at 300° C. for 1.0 h. After the heat preservation is over, use the duplex auger to push the material into the dilution tank 4 for dilution, and then obtain 183.3kg of m-aminophenol crude product after desalination, acid precipitation and purification, with a yield of 91.19%, and its m-aminophenol content GC test is 99.70%.
Embodiment 2
[0032] The schematic diagram of the production device for continuous production of m-aminophenol is as follows: figure 1 As shown, put 360kg of sodium m-sulfamic acid (purified), 154kg of sodium hydroxide, and 160kg of potassium hydroxide into batching tank 1 in sequence, and heat up to 250°C with heat transfer oil while stirring. Continuously discharge the material into the heating spiral pipe reactor 2, raise the temperature to 300°C, and heat up for 2.0 hours. Then continuously feed into the thermal insulation spiral pipe reactor 3, and keep the temperature at 300°C for 2.0h. After the heat preservation is finished, push the material into the dilution tank 4 for dilution, and then obtain 180.2 kg of m-aminophenol crude product after desalination, acid analysis and purification, with a yield of 89.65%, and the m-aminophenol content is 99.68% by GC test.
Embodiment 3
[0034] The schematic diagram of the production device for continuous production of m-aminophenol is as follows: figure 1 As shown, put 360kg of sodium m-sulfamic acid (purified), 140kg of sodium hydroxide, and 145kg of potassium hydroxide into the batching tank 1 in sequence, and heat up to 250°C with heat transfer oil while stirring. Continuously discharge the material into the heating spiral pipe reactor 2, raise the temperature to 300°C, and heat up for 2.0 hours. Then continuously feed into the thermal insulation spiral pipe reactor 3, and keep the temperature at 300°C for 2.0h. After the heat preservation is completed, push the material into the dilution tank 4 for dilution, and then obtain 179.5 kg of m-aminophenol crude product after desalination, acid analysis and purification, with a yield of 89.30%, and its m-aminophenol content is 99.75% by GC test.
PUM
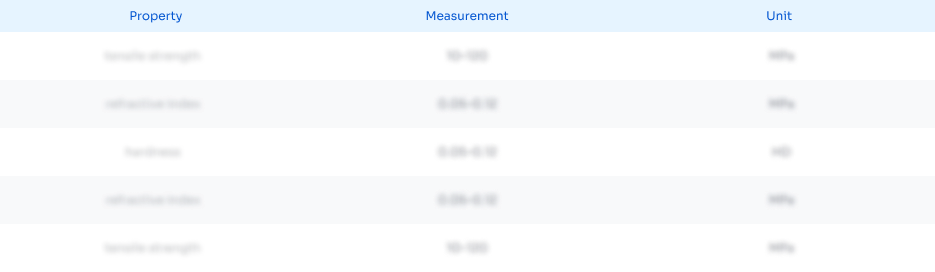
Abstract
Description
Claims
Application Information

- Generate Ideas
- Intellectual Property
- Life Sciences
- Materials
- Tech Scout
- Unparalleled Data Quality
- Higher Quality Content
- 60% Fewer Hallucinations
Browse by: Latest US Patents, China's latest patents, Technical Efficacy Thesaurus, Application Domain, Technology Topic, Popular Technical Reports.
© 2025 PatSnap. All rights reserved.Legal|Privacy policy|Modern Slavery Act Transparency Statement|Sitemap|About US| Contact US: help@patsnap.com