High-toughness halogen-free cyanate composite material and preparation method thereof
A technology of halocyanate and composite materials, which is applied in the field of high-toughness halogen-free cyanate composite materials and its preparation, can solve the problems of uneven dispersion of carbon nanotubes, low toughness, and insignificant toughening effect, and achieve enhanced Toughness, enhanced toughness, high toughness and effects on mechanical strength and corrosion resistance
- Summary
- Abstract
- Description
- Claims
- Application Information
AI Technical Summary
Problems solved by technology
Method used
Image
Examples
Embodiment 1
[0024] The specific preparation process of phosphorus-containing cyanate ester resin is as follows:
[0025] ①Add 1kg of 2,2-dimethyl-3-hydroxypropanal and 2.703 ferric chloride into 30L acetone solution, stir and mix and heat to 55-60℃, and then add phosphorus pentoxide to it every 20min, keeping each Add the same amount each time. The total mass of phosphorus pentoxide added is 2.145kg. After the addition is complete, stir at constant temperature for 30 minutes, then heat up to 80-85°C and stir for 3 hours, and then heat up to 60-65°C to evaporate and remove the solvent acetone. The obtained solid product is added to water and stirred evenly and then filtered and dried to obtain an aldehyde phosphate;
[0026] ②Weigh 0.935kg of p-hydroxyaniline and add it to 15L ethanol solution, add 1kg of the aldehyde phosphate prepared in step ① to it at room temperature, stir and react for 1-1.5h, solids are formed, then filter to obtain polyphenol-based phosphoric acid ester;
[0027] ③Put 1...
Embodiment 2
[0033] The specific preparation process of the phosphorus-containing cyanate ester resin is the same as in Example 1, and the amount of 2,2-dimethyl-3-hydroxypropionaldehyde added in the first step of Example 1 is replaced with 0.5 kg.
[0034] The specific preparation process of the modified carbon nanotubes is the same as in Example 1, and the added amount of 4-pentene azide in the second step of Example 1 is replaced with 25 g.
Embodiment 3
[0036] A specific preparation method of a high-toughness halogen-free cyanate ester composite material is as follows: 1 kg of the phosphorus-containing cyanate resin prepared in Example 1 and 21 g of the modified carbon nanotubes prepared in Example 1 are simultaneously added to the reaction vessel, Warm up to 130-140℃, miscible and stir for 40-50min, then pour into the preheated mold, degas bubbles under 150℃ vacuum for 30min, and then increase from 160℃ to 220℃ according to the heating rate of 20℃ per hour After curing, treat at 250°C for 5-6h, and then cool to room temperature to obtain halogen-free cyanate ester composite.
PUM
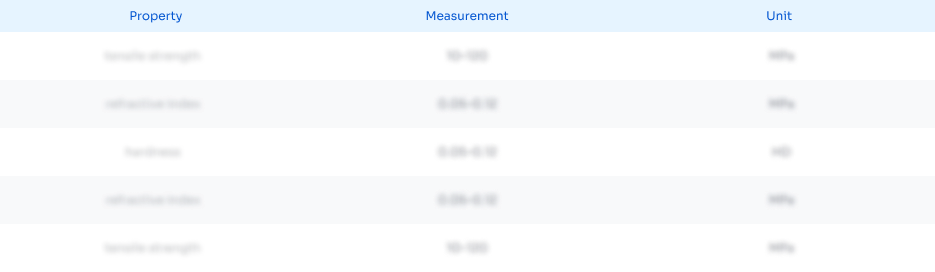
Abstract
Description
Claims
Application Information

- R&D Engineer
- R&D Manager
- IP Professional
- Industry Leading Data Capabilities
- Powerful AI technology
- Patent DNA Extraction
Browse by: Latest US Patents, China's latest patents, Technical Efficacy Thesaurus, Application Domain, Technology Topic, Popular Technical Reports.
© 2024 PatSnap. All rights reserved.Legal|Privacy policy|Modern Slavery Act Transparency Statement|Sitemap|About US| Contact US: help@patsnap.com