A steel slag treatment method using oxidation desulfurization and reduction dephosphorization two-step method
A technology of oxidative desulfurization and treatment method, which is applied in the field of iron and steel metallurgy, and can solve the problems of reducing dephosphorization of steel slag, desulfurization ability, adverse effects of molten steel composition, etc.
- Summary
- Abstract
- Description
- Claims
- Application Information
AI Technical Summary
Problems solved by technology
Method used
Image
Examples
Embodiment 1
[0029] This embodiment discloses a steel slag treatment method using two-step oxidation desulfurization and reduction dephosphorization methods, such as figure 1 shown, including the following steps:
[0030] Step S1. Oxidize and desulfurize the steel slag; pass Ar and O into the molten steel slag 2 The mixed gas, the SO obtained by oxidation 2 Overflowing and removing from the slag phase, the removal rate of S is 82-97%;
[0031] CaS+0 2 =CaO+SO 2
[0032] In step S1, the oxidizing atmosphere is Ar and O 2 The mixed gas, because it does not contain N 2 , to avoid the production of NOx, the resulting SO 2 It overflows and removes from the slag phase, making the removal rate of S as high as 82-97%.
[0033] Compared with the prior art, the present invention can thoroughly solve the problem of removing sulfur and phosphorus in steel slag, greatly improve the recycling rate of steel slag, realize the full utilization of steel slag, S and P, reduce the cost of steelmaking,...
Embodiment 2
[0053] This embodiment adopts converter steel slag, wherein, TFe content is 18.2%, P 2 o 5 The content is 1.64%, the S content is 0.07%, and the dual natural alkalinity is 3.1. Put cold steel slag into a high-purity corundum crucible, heat it to 1650°C in a tubular resistance furnace and keep it warm for 30 minutes. After the steel slag is completely melted, an oxidizing atmosphere is provided through a thin corundum tube inserted from the top of the crucible. 2 The content is 10-35%, and the oxidation time is 15 minutes. After the reaction time is up, the crucible is taken out and rapidly cooled in the air. After crushing and grinding, the sulfur content and metal iron content of the slag are determined by a carbon-sulfur analyzer and chemical analysis.
[0054] The analysis results showed that the O in the atmosphere 2 The content is controlled at 10%, 15%, 20%, 30%, and 35%, and the removal rates of sulfur in steel slag are 54%, 82%, 91%, 95%, and 97%, respectively. It ...
Embodiment 3
[0058] This embodiment 3 and embodiment 1 adopt the same steel slag and adopt the same process flow for oxidation desulfurization treatment, the difference is that the oxygen partial pressure is controlled at 20%, and the oxidation time range is 5-20min. After the reaction time is reached, the The crucible was taken out and cooled rapidly in the air, and after crushing and grinding, the sulfur content of the slag was determined by a carbon-sulfur analyzer.
[0059] By analyzing Table 2, it can be seen that when the oxidative desulfurization time is 5 minutes, the sulfur removal rate is 47%, the sulfur removal rate exceeds 90% after the desulfurization time exceeds 10 minutes, and the sulfur removal rate does not increase significantly after the desulfurization time exceeds 15 minutes. 10 to 15 minutes.
[0060] Table 2 Changes of sulfur removal rate in steel slag with oxidation desulfurization time
[0061] Oxidative desulfurization time (min) 5 10~15 >15 Su...
PUM
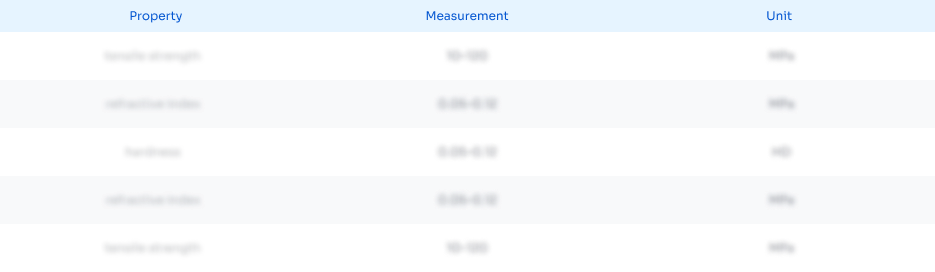
Abstract
Description
Claims
Application Information

- Generate Ideas
- Intellectual Property
- Life Sciences
- Materials
- Tech Scout
- Unparalleled Data Quality
- Higher Quality Content
- 60% Fewer Hallucinations
Browse by: Latest US Patents, China's latest patents, Technical Efficacy Thesaurus, Application Domain, Technology Topic, Popular Technical Reports.
© 2025 PatSnap. All rights reserved.Legal|Privacy policy|Modern Slavery Act Transparency Statement|Sitemap|About US| Contact US: help@patsnap.com