Zirconium-containing electrothermal alloy and preparation method of zirconium-containing alloy
An electrothermal alloy and zirconium alloy technology, which is applied in the direction of improving process efficiency and energy efficiency, can solve the problems of large fluctuation of zirconium element composition and reducing the yield of electroslag ingots.
- Summary
- Abstract
- Description
- Claims
- Application Information
AI Technical Summary
Problems solved by technology
Method used
Image
Examples
Embodiment 1
[0056] This embodiment provides a zirconium-containing electrothermal alloy, which includes: carbon: ≤0.03%, chromium: 19%-22%, aluminum: 3.3%-3.6%, zirconium: 0.35%-0.43%, silicon: ≤0.5%, titanium: 0.2% to 0.6%, manganese: ≤0.5%, magnesium ≥0.004%, sulfur: ≤0.01%, phosphorus: ≤0.03%, and the balance is Fe. The preparation method of this alloy is as follows:
[0057] (1) Vacuum induction smelting: According to the element ratio principle of zirconium-containing alloys, the smelting raw materials that can obtain carbon, chromium, aluminum, zirconium, silicon, titanium, manganese, magnesium and iron elements are weighed, and the raw materials include industrial pure iron and metal chromium , graphite, aluminum ingots, iron zirconium, titanium sponge, nickel-magnesium alloy; put industrial pure iron and metal chromium in the crucible of the induction furnace; put graphite, aluminum ingots, iron zirconium, and titanium sponge in the feeding bin, and finally add Nickel-magnesium a...
Embodiment 2
[0073] This embodiment provides a zirconium-containing electrothermal alloy, which includes: carbon: ≤0.03%, chromium: 19%-22%, aluminum: 3.3%-3.6%, zirconium: 0.35%-0.43%, silicon: ≤0.5%, titanium: 0.2% to 0.6%, manganese: ≤0.5%, magnesium ≥0.004%, sulfur: ≤0.01%, phosphorus: ≤0.03%, and the balance is Fe. The preparation method of this alloy is as follows:
[0074] (1) Vacuum induction smelting: According to the element ratio principle of zirconium-containing alloys, the smelting raw materials that can obtain carbon, chromium, aluminum, zirconium, silicon, titanium, manganese, magnesium and iron elements are weighed, and the raw materials include industrial pure iron and metal chromium , graphite, aluminum ingots, iron zirconium, titanium sponge, nickel-magnesium alloy; put industrial pure iron and metal chromium in the crucible of the induction furnace; put graphite, aluminum ingots, iron zirconium, and titanium sponge in the feeding bin, and finally add Nickel-magnesium a...
PUM
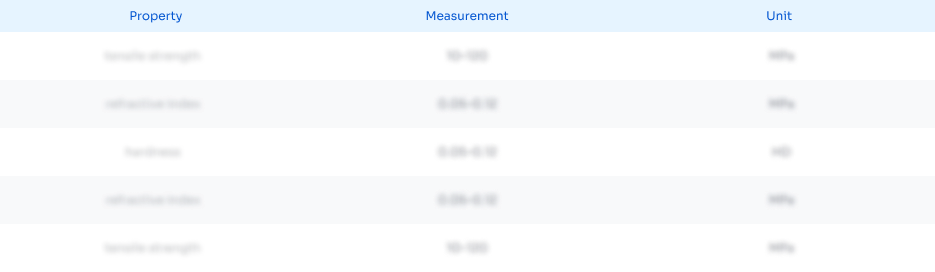
Abstract
Description
Claims
Application Information

- R&D Engineer
- R&D Manager
- IP Professional
- Industry Leading Data Capabilities
- Powerful AI technology
- Patent DNA Extraction
Browse by: Latest US Patents, China's latest patents, Technical Efficacy Thesaurus, Application Domain, Technology Topic, Popular Technical Reports.
© 2024 PatSnap. All rights reserved.Legal|Privacy policy|Modern Slavery Act Transparency Statement|Sitemap|About US| Contact US: help@patsnap.com