Manufacturing method of medium-carbon CrMo steel wire rod free of annealing and drawing
A manufacturing method, an annealing-free technology, applied in the direction of temperature control, metal rolling, etc., can solve the problems of high mechanical performance requirements for uniform cleaning rods, failure to meet the rolling temperature requirements in the two-phase region, and coarse pearlite grains. , to avoid the formation of abnormal tissue in the center, improve the internal quality and reduce the strength
- Summary
- Abstract
- Description
- Claims
- Application Information
AI Technical Summary
Problems solved by technology
Method used
Image
Examples
Embodiment 1
[0030] The specifications of the non-annealing medium carbon CrMo steel wire rod involved in this example are φ14mm, and the contained components and their mass percentages are: C: 0.36%, Si: 0.18%, Mn: 0.70%, P: 0.010%, S: 0.003 %, Cr: 1.06%, Mo: 0.17%, Al: 0.025%, N: 0.0056%, O: 0.0008%, H: 0.0001%, and the balance is iron and unavoidable impurity elements.
[0031] The production process of this annealing-free medium carbon CrMo steel wire rod is as follows:
[0032] The smelting raw materials are configured according to the chemical composition of the wire rod, followed by KR molten iron pretreatment-converter smelting-LF+RH refining-continuous casting-continuous casting slab warm or hot delivery-continuous casting slab heating, billet opening-intermediate billet surface cleaning - Reheating - Descaling with high pressure water - Controlled rolling and temperature control - Controlled cooling - Wire rod.
[0033] In the KR hot metal pretreatment, the molten iron is desulf...
Embodiment 2
[0039] The specifications of the non-annealing medium carbon CrMo steel wire rod involved in this embodiment are φ5.5mm, and the components and their mass percentages are: C: 0.35%, Si: 0.18%, Mn: 0.69%, P: 0.0012%, S : 0.003%, Cr: 1.05%, Mo: 0.17%, Al: 0.028%, N: 0.0055%, O: 0.0008%, H: 0.0001%, and the balance is iron and unavoidable impurity elements.
[0040] The production process of wire rod is basically the same as Example 1, but there are differences in its rolling and cooling process, as follows:
[0041] The continuous casting billet is opened to obtain the intermediate billet (140mm 2 ), heating stage I at 800°C, heating stage II at 980-1010°C, heating stage III at 1025°C, heating stage III holding time for 45 minutes, total heating time of 100 minutes, residual oxygen in the furnace: 0.9%, and descaling with high-pressure water after leaving the furnace , and then rolled. The rough rolling start temperature is 900℃, the total compression ratio is 68%; the finishi...
PUM
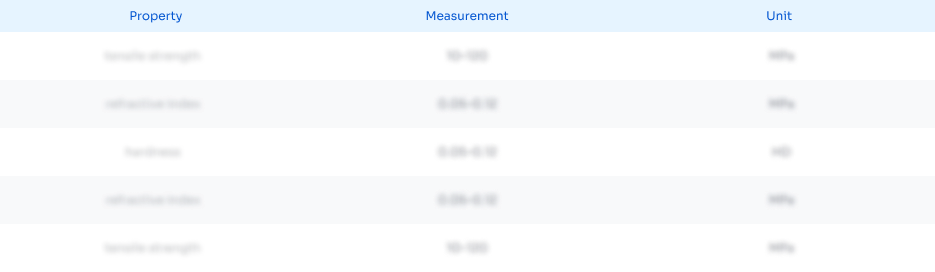
Abstract
Description
Claims
Application Information

- R&D Engineer
- R&D Manager
- IP Professional
- Industry Leading Data Capabilities
- Powerful AI technology
- Patent DNA Extraction
Browse by: Latest US Patents, China's latest patents, Technical Efficacy Thesaurus, Application Domain, Technology Topic, Popular Technical Reports.
© 2024 PatSnap. All rights reserved.Legal|Privacy policy|Modern Slavery Act Transparency Statement|Sitemap|About US| Contact US: help@patsnap.com