Differential grinding roller type rapid biomass catalytic pyrolysis device and method
A technology of catalytic pyrolysis and biomass, which is applied in the field of differential-speed roller-type rapid catalytic pyrolysis of biomass, can solve the problems of reducing reactor processing efficiency, increasing the cost of biomass processing, and failing to guarantee the catalytic effect, etc., to achieve Compact structure, large specific heat capacity, good catalytic effect
- Summary
- Abstract
- Description
- Claims
- Application Information
AI Technical Summary
Problems solved by technology
Method used
Image
Examples
Embodiment 1
[0049] Bagasse with a moisture content of 8wt% is crushed to an average particle size of 8mm, and enters the differential roller pyrolysis reactor 3 through the screw feed system 2 at a feed rate of 120kg / h; the catalytic layer is activated by steam Activated carbon is extruded onto the surface of the grinding disc, and the friction layer is made of friction coating, such as Figure 4 As shown; by adjusting the power of the motor, the active high-speed roller shaft speed is guaranteed to be 10r / min, and a 4:5 gear transmission is used to drive the low-speed roller shaft speed to 8r / min; enter the high temperature in the differential grinding roller pyrolysis reactor 3 The temperature of the molten salt in the molten salt heat exchange tube 307 is 400°C, and the measured temperature in the pyrolysis reactor is 310°C; the pyrolysis product is separated from the gas-solid and condensed from the pyrolysis gas to obtain the target product 4-ethylphenol The yield of bio-oil, 4-ethyl...
Embodiment 2
[0051] The pine wood with a moisture content of 8wt% is crushed to an average particle size of 8 mm, and then sent into the differential grinding roller pyrolysis reactor 3 after passing through the screw feed system 2 at a feed rate of 100 kg / h; The temperature of the low-speed roller shaft is 15r / min, and the speed of the low-speed roller is 10r / min; the temperature of the molten salt entering the high-temperature molten salt heat exchange tube 307 in the differential grinding roller pyrolysis reactor 3 is 650°C to ensure that the temperature in the pyrolysis reactor is maintained At 500°C; the catalyst of the disc catalyst layer is solid potassium phosphate, and the friction layer is friction coating, such as Figure 4 Shown; After the pyrolysis product is subjected to gas-solid separation and pyrolysis gas condensation, coke, bio-oil and combustible gas three-phase pyrolysis products are obtained, and the respective yields are 29.4wt%, 48.6wt% and 22.0wt%; The content of t...
Embodiment 3
[0053] The corn cob with a moisture content of 8wt% was crushed to an average particle size of 10mm, and then impregnated with ZnCl 2 and dried, ZnCl 2 The loading capacity is 15.4wt%; through the screw feeding system 2 with the feed rate of 100kg / h, the material particles are sent into the differential grinding roller pyrolysis reactor 3, and the speed ratio of the two grinding rollers is 1:2; by adjusting The power of the motor ensures that the speed of the high-speed roller shaft is 10r / min; the temperature of the molten salt entering the high-temperature molten salt heat exchange coil 307 in the differential roller pyrolysis reactor 3 is 440°C, and the temperature in the pyrolysis reactor is 340°C ; After the pyrolysis product is separated from gas and solid and condensed from the pyrolysis gas, coke, bio-oil and combustible gas three-phase pyrolysis products are obtained, and the respective yields are 43.2wt%, 48.1wt% and 8.7wt%, wherein the target product The yield of f...
PUM
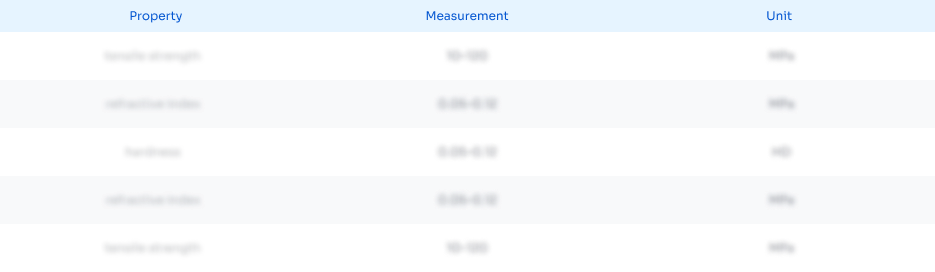
Abstract
Description
Claims
Application Information

- Generate Ideas
- Intellectual Property
- Life Sciences
- Materials
- Tech Scout
- Unparalleled Data Quality
- Higher Quality Content
- 60% Fewer Hallucinations
Browse by: Latest US Patents, China's latest patents, Technical Efficacy Thesaurus, Application Domain, Technology Topic, Popular Technical Reports.
© 2025 PatSnap. All rights reserved.Legal|Privacy policy|Modern Slavery Act Transparency Statement|Sitemap|About US| Contact US: help@patsnap.com