Preparation method of thick CrN coating on surface of cladding material
A cladding material and coating technology, applied in the direction of metal material coating process, coating, reactor fuel elements, etc., can solve the problem of low fault tolerance capacity of accidents, achieve the effect of improving fault tolerance capacity of accidents and improving mechanical properties
- Summary
- Abstract
- Description
- Claims
- Application Information
AI Technical Summary
Problems solved by technology
Method used
Image
Examples
preparation example Construction
[0042] figure 1 It is a flow chart of the preparation method of the CrN thick coating on the surface of the cladding material provided by the present invention. see figure 1 , the preparation method of cladding material surface CrN (chromium nitride) thick coating provided by the invention comprises:
[0043] Step 101: Prepare cladding material to be plated.
[0044]In the present invention, the cladding material made of zirconium (Zr) alloy is used as the substrate or workpiece, and the cladding material includes Zr-2, Zr-4, Zr-5, M5, ZIRLO, N18, N36, E635 and other nuclear zirconium alloys , and the improved and optimized nuclear zirconium alloy. Use multi-arc ion plating technology or other technologies based on multi-arc ion plating to prepare an accident-resistant, unsaturated thick CrN coating as a protective coating on the surface of the cladding material zirconium alloy by PVD method.
[0045] Step 102: Perform pretreatment on the cladding material to form a pretre...
Embodiment 1
[0073] Base material: Zr-4 zirconium alloy
[0074] The preparation method comprises the following steps:
[0075] (1) Pretreatment: Clean the surface of the cladding material, pipe fittings or workpiece, remove dust, oil, grease, and after drying, install the clamp, keep the distance between the target and the base at 180mm, and vacuumize to 3.0×10 -3 Pa, the deposition temperature is at 420°C.
[0076] (2) Electron gun cleaning: Use a hollow cathode electron gun to clean the pretreated cladding material workpiece again, fill the electron gun with an atmosphere of 1.0-3.0 PaAr, excite argon ions, increase the bias voltage on the workpiece, and activate the surface of the substrate for 5 minutes.
[0077] (3) Generate transition layer: adjust the Ar pressure to 0.3Pa, ignite the Cr arc source, sputter and clean the Cr target under the action of a high bias voltage of -750V, arc current 120A, duty cycle 80%, deposit Cr as the transition layer, and deposit Time 200S.
[0078]...
Embodiment 2
[0081] Base material: M5 zirconium alloy
[0082] The preparation method comprises the following steps:
[0083] (1) Pre-treatment: Clean the surface of the cladding material, pipe fittings or workpiece, remove dust, oil, grease, and after drying, install the clamp, keep the distance between the target and the base at 220mm, and vacuumize to 4.0×10 -3 Pa, the deposition temperature is 350°C.
[0084] (2) Electron gun cleaning: Use a hollow cathode electron gun to clean the pretreated workpiece again, fill the electron gun with an atmosphere of 1.0-3.0 PaAr, excite argon ions, increase the bias voltage on the workpiece, and activate the surface of the substrate for 5 minutes.
[0085] (3) Generate transition layer: adjust the Ar pressure to 0.3Pa, ignite the Cr arc source, sputter and clean the Cr target under the action of a high bias voltage of -750V, arc current 120A, duty cycle 80%, deposit Cr as the transition layer, and deposit Time 200S.
[0086] (4) Deposition gradie...
PUM
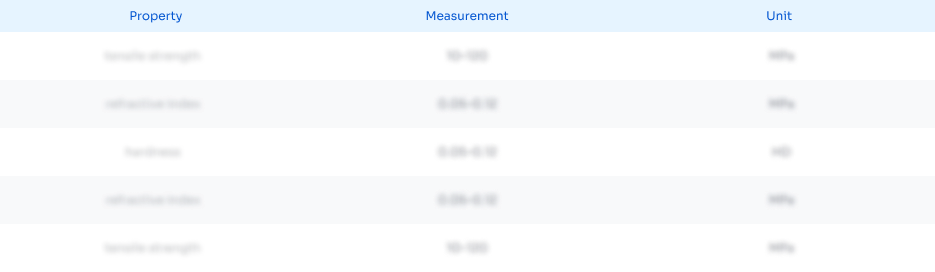
Abstract
Description
Claims
Application Information

- Generate Ideas
- Intellectual Property
- Life Sciences
- Materials
- Tech Scout
- Unparalleled Data Quality
- Higher Quality Content
- 60% Fewer Hallucinations
Browse by: Latest US Patents, China's latest patents, Technical Efficacy Thesaurus, Application Domain, Technology Topic, Popular Technical Reports.
© 2025 PatSnap. All rights reserved.Legal|Privacy policy|Modern Slavery Act Transparency Statement|Sitemap|About US| Contact US: help@patsnap.com