Preparation method for rubber composite material
A composite material and rubber technology, applied in the field of material preparation, can solve problems such as poor compatibility and difficulty in dispersing
- Summary
- Abstract
- Description
- Claims
- Application Information
AI Technical Summary
Problems solved by technology
Method used
Examples
example 1
[0020] The preparation method of rubber composite material of the present invention, comprises the steps:
[0021] (1) Weigh the silica slurry, make a suspension with a mass fraction of 0.1, and place it on an electric stirrer to stir for pre-dispersion; Slowly add the ethanol solution of coupling agent Si69 dropwise in the medium, the addition amount is 3% of the quality of the silica; high-speed stirring makes the coupling agent Si69 and the silica suspension fully mixed uniformly to obtain an activated modified silica suspension;
[0022] (2) Prepare modified silica in the same way, and grind it in a colloid mill for 30 minutes;
[0023] (3) Use potassium hydroxide to adjust the pH value of the modified silica suspension or modified white carbon black dispersion system to about 9, then weigh the natural rubber latex into the dispersion system, stir and disperse with an electric stirrer for 2 hours;
[0024] (4) Coagulate with calcium chloride solution, crepe, granulate, an...
Embodiment 2
[0038] On the basis of embodiment one, the preparation method of rubber composite material of the present invention comprises the following steps:
[0039] (1) Weigh the silica slurry, make a suspension with a mass fraction of 0.1, and place it on an electric stirrer to stir for pre-dispersion; Slowly add the ethanol solution of coupling agent Si69 dropwise in the medium, and the addition amount is 4% of the silica mass; high-speed stirring makes the coupling agent Si69 and the silica suspension fully mixed uniformly to obtain an activated modified silica suspension;
[0040] (2) Prepare modified silica in the same way, and grind it in a colloid mill for 33 minutes;
[0041] (3) Use potassium hydroxide to adjust the pH value of the modified silica suspension or modified white carbon black dispersion system to about 9, then weigh the natural rubber latex into the dispersion system, stir and disperse with an electric stirrer for 2 hours;
[0042] (4) Coagulate with calcium chlo...
Embodiment 3
[0045] The preparation method of rubber composite material of the present invention, comprises the steps:
[0046] (1) Weigh the silica slurry, make a suspension with a mass fraction of 0.1, and place it on an electric stirrer to stir for pre-dispersion; Slowly add the ethanol solution of coupling agent Si69 dropwise, the addition is 5% of the quality of the silica; high-speed stirring makes the coupling agent Si69 and the silica suspension fully mixed evenly to obtain an activated modified silica suspension;
[0047] (2) Prepare modified silica in the same way, and grind it in a colloid mill for 35 minutes;
[0048] (3) Use potassium hydroxide to adjust the pH value of the modified silica suspension or the modified silica dispersion system to about 9, then weigh the natural rubber latex into the dispersion system, stir and disperse with an electric mixer for 2 hours;
[0049] (4) Coagulate with calcium chloride solution, crepe, granulate, and dry at 65°C for 48 hours to obta...
PUM
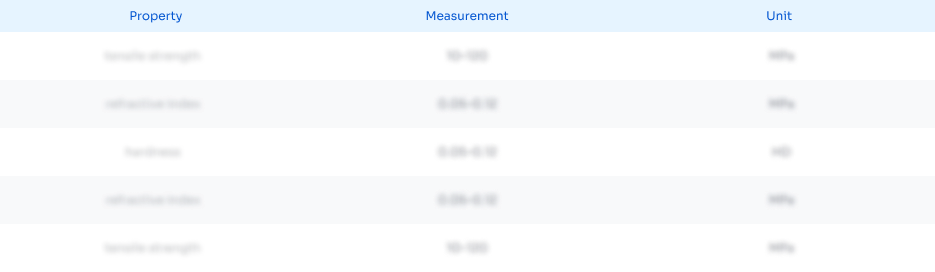
Abstract
Description
Claims
Application Information

- Generate Ideas
- Intellectual Property
- Life Sciences
- Materials
- Tech Scout
- Unparalleled Data Quality
- Higher Quality Content
- 60% Fewer Hallucinations
Browse by: Latest US Patents, China's latest patents, Technical Efficacy Thesaurus, Application Domain, Technology Topic, Popular Technical Reports.
© 2025 PatSnap. All rights reserved.Legal|Privacy policy|Modern Slavery Act Transparency Statement|Sitemap|About US| Contact US: help@patsnap.com