Aluminum alloy and casting method thereof
A technology of aluminum alloy and molten aluminum, applied in the field of aluminum alloy materials, can solve the problems of increasing the trouble of composition adjustment, high melting point of pure silicon element, and high impurity content, and achieves a solution that is conducive to lean management, reduces impurity content, and contains less impurities. Effect
- Summary
- Abstract
- Description
- Claims
- Application Information
AI Technical Summary
Problems solved by technology
Method used
Image
Examples
Embodiment 1
[0075] (1) Preparation of aluminum alloy silicon ingot:
[0076] Table 1 is the element content table of the aluminum alloy silicon ingot prepared by default.
[0077] Table 1. Content % of each element in aluminum alloy silicon ingot
[0078]
[0079] Concrete preparation steps are as follows:
[0080] 1. Raw material melting: put aluminum ingots (70%) and scrap (grade 1 scrap, 6-series aluminum alloy rod head and tail / soup / excess waste) (30%) into the melting furnace for melting;
[0081] 2. Pure silicon smelting: After the raw materials are melted, the temperature of the molten aluminum is controlled at 750°C, and pure silicon (grade 441) is added;
[0082] 3. Refining: for the first refining, the amount of refining agent is 0.2kg / ton of aluminum, the nitrogen pressure is 0.15mpa, the purity of nitrogen is ≥99.96%, and the refining time is 15min / time;
[0083] 4. Composition analysis: remove slag from the refined aluminum liquid, and then take samples for spectral ana...
Embodiment 2
[0147] Table 1. Contents of elements in aluminum alloy silicon ingots
[0148]
[0149]
[0150] (1) Preparation of aluminum alloy silicon ingot:
[0151] 1. Raw material melting: put aluminum ingots (80%) and scrap (grade 1 scrap, 6-series aluminum alloy rod head and tail / soup / excess scrap) (20%) into the melting furnace for melting;
[0152] 2. Pure silicon smelting: After the raw materials are melted, control the temperature of the molten aluminum to 800°C, and add pure silicon (grade 441);
[0153] 3. Refining: for the first refining, the amount of refining agent is 1.2kg / ton of aluminum, the nitrogen pressure is 0.45mpa, the nitrogen purity is ≥99.96%, and the refining time is 30min / time;
[0154] 4. Composition analysis: remove slag from the refined aluminum liquid, and then take samples for spectral analysis;
[0155] 5. Composition adjustment: According to the results of spectral analysis, calculate the content of each element in the aluminum liquid, compare it...
Embodiment 3
[0186] 1. Preparation of aluminum alloy silicon ingot
[0187] Table 1. Contents of elements in aluminum alloy silicon ingots
[0188]
[0189] The specific preparation steps of aluminum alloy silicon ingot are as follows:
[0190] 1. Raw material melting: put aluminum ingots (80%) and scrap (grade 1 scrap, 6-series aluminum alloy rod head and tail / soup / excess scrap) (20%) into the melting furnace for melting;
[0191] 2. Pure silicon smelting: After the raw materials are melted, control the temperature of the molten aluminum to 780°C, and add pure silicon (grade 441);
[0192] 3. Refining: for the first refining, the amount of refining agent is 0.8kg / ton of aluminum, the pressure of nitrogen is 0.35mpa, the purity of nitrogen is ≥99.96%, and the refining time is 25min / time;
[0193] 4. Composition analysis: remove slag from the refined aluminum liquid, and then take samples for spectral analysis;
[0194] 5. Composition adjustment: According to the results of spectral a...
PUM
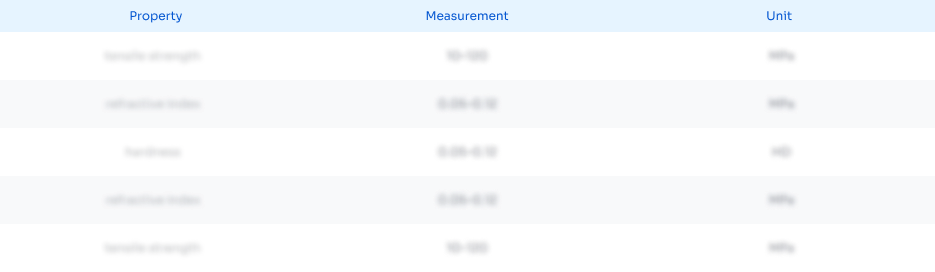
Abstract
Description
Claims
Application Information

- Generate Ideas
- Intellectual Property
- Life Sciences
- Materials
- Tech Scout
- Unparalleled Data Quality
- Higher Quality Content
- 60% Fewer Hallucinations
Browse by: Latest US Patents, China's latest patents, Technical Efficacy Thesaurus, Application Domain, Technology Topic, Popular Technical Reports.
© 2025 PatSnap. All rights reserved.Legal|Privacy policy|Modern Slavery Act Transparency Statement|Sitemap|About US| Contact US: help@patsnap.com