Process for hydrogenating treatment of waste lubricating oil by tandem type double-boiling-bed reactors
A technology of fluidized bed reactor and waste lubricating oil, which is applied in hydrotreating process, treatment of hydrocarbon oil, petroleum industry, etc., can solve the problems of device startup, frequent shutdown, difficult economic benefits for the owner, and inability to solve the problem, and achieves operating costs. The effect of less, considerable economic benefits, and compact device layout
- Summary
- Abstract
- Description
- Claims
- Application Information
AI Technical Summary
Problems solved by technology
Method used
Image
Examples
Embodiment 1
[0034] 1) Get 50 kilograms of recovered waste lubricating oil and add it to a jacketed steam-heated reaction kettle, and feed N into the reaction kettle equipped with waste lubricating oil 2 , Exhaust the air in the reactor. Seal the feed port of the reaction kettle, pass steam into the jacket of the reaction kettle to heat the waste lubricating oil, heat the waste lubricating oil to 65±5°C, slowly and evenly add it to the centrifuge chamber of the normally rotating centrifuge, and carry out waste lubrication The oil is centrifuged to separate water and ≥25μm solid particles. After the centrifuge runs normally for 30 minutes, stop the centrifuge, take out the waste lubricating oil from the upper part of the centrifuge chamber, and pour the water and solid particles in the lower part of the centrifuge chamber into the waste oil pool.
[0035] The analytical data of the pretreated waste engine oil are listed in Table 1.
[0036] Table 1 The property index of waste engine oil a...
Embodiment 2
[0055] 1) The pretreatment process of the waste lubricating oil is the same as that of Example 1 except that the heating temperature of the waste lubricating oil is 45±5° C. and the centrifuge rotates normally for 50 minutes.
[0056] 2) The evaluation process conditions of the waste lubricating oil on the evaluation device of the serial double ebullating bed reactor are listed in Table 6, and other operating steps are exactly the same as step 2) of Example 1.
[0057] Table 6 Process conditions for waste lubricating oil fluidized bed hydrotreating
[0058] Process conditions
Spherical Prehydrotreating Catalyst
Spherical primary hydrotreating catalyst
Total system pressure, MPa
12
12
230
340
Liquid space velocity, h -1
0.3
1.0
Hydrogen oil ratio (v)
500 / 1
500 / 1
Hydrogen purity, m%
>95
>95
[0059] 3) Except for maintaining the constant temperature at 345° C. for 3....
Embodiment 3
[0063] 1) The pretreatment process of the waste lubricating oil is the same as that of Example 1 except that the heating temperature of the waste lubricating oil is 75±5° C. and the centrifuge rotates normally for 20 minutes.
[0064] 2) The evaluation process conditions of the waste lubricating oil on the evaluation device of the serial double ebullated bed reactor are listed in Table 7, and other operating steps are exactly the same as step 2) of Example 1.
[0065] Table 7 Process conditions for waste lubricating oil fluidized bed hydrotreating
[0066] Process conditions
Spherical Prehydrotreating Catalyst
Spherical primary hydrotreating catalyst
Total system pressure, MPa
18
18
230
340
Liquid space velocity, h -1
0.8
0.6
Hydrogen oil ratio (v)
1000 / 1
1000 / 1
Hydrogen purity, m%
>90
>90
[0067] 3) Except for maintaining the constant temperature at 330° C. for 4...
PUM
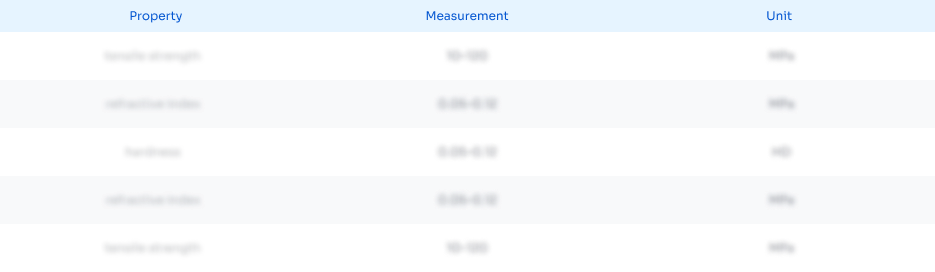
Abstract
Description
Claims
Application Information

- R&D
- Intellectual Property
- Life Sciences
- Materials
- Tech Scout
- Unparalleled Data Quality
- Higher Quality Content
- 60% Fewer Hallucinations
Browse by: Latest US Patents, China's latest patents, Technical Efficacy Thesaurus, Application Domain, Technology Topic, Popular Technical Reports.
© 2025 PatSnap. All rights reserved.Legal|Privacy policy|Modern Slavery Act Transparency Statement|Sitemap|About US| Contact US: help@patsnap.com