Method for preparing graphene oxide grafted carbon fiber based on thiol-ene chemical reaction
A chemical reaction, carbon fiber technology, used in carbon fiber, fiber processing, textiles and papermaking, etc., can solve the problems of difficult industrialization, harsh reaction conditions, long reaction period, etc., to achieve short reaction period, improve interface properties, and improve overall mechanical properties Effect
- Summary
- Abstract
- Description
- Claims
- Application Information
AI Technical Summary
Problems solved by technology
Method used
Examples
Embodiment 1
[0014] This example illustrates a method for preparing graphene oxide grafted carbon fibers based on the chemical reaction of mercaptoene provided by the present invention.
[0015] Step 1: Put 4g of carbon fiber into 150mL of hydrogen peroxide with a mass percent solubility of 30%, then react in an oil bath at 80°C for 1 hour, wash the resulting product with deionized water 4 times, and dry it in vacuum at 110°C Dry in the box for 24 hours to obtain oxidized carbon fiber;
[0016] The second step: put 4g of oxidized carbon fiber into a round bottom flask, add 150mL of a mixed solution of ethanol and mercaptopropyltriethoxysilane with a volume ratio of 95:5, adjust the pH of the solution to 4 with acetic acid, and then The reaction was carried out under the condition of an oil bath at ℃ for 6 hours. After the reaction, the product was washed 4 times with a mixed solution of ethanol and deionized water, and dried in a vacuum oven at 100 ℃ for 24 hours to obtain mercapto-functio...
Embodiment 2
[0020] This example illustrates a method for preparing graphene oxide grafted carbon fibers based on the chemical reaction of mercaptoene provided by the present invention.
[0021] Step 1: Put 4g of carbon fiber into 50mL of hydrogen peroxide with a mass percent solubility of 30%, then react in an oil bath at 50°C for 3 hours, wash the resulting product with deionized water for 4 times, and dry it under vacuum at 110°C Dry in the box for 24 hours to obtain oxidized carbon fiber;
[0022] The second step: put 4g of oxidized carbon fiber into a round bottom flask, add 50mL of a mixed solution of ethanol and 2-mercaptoethyltriethoxysilane with a volume ratio of 95:5, adjust the pH of the solution to 6 with acetic acid, and then React in an oil bath at 60°C for 8 hours. After the reaction, the product is washed 4 times with a mixed solution of ethanol and deionized water, and dried in a vacuum oven at 100°C for 24 hours to obtain mercapto-functionalized carbon fibers;
[0023] S...
Embodiment 3
[0026] This example illustrates a method for preparing graphene oxide grafted carbon fibers based on the chemical reaction of mercaptoene provided by the present invention.
[0027] Step 1: Put 4g of carbon fiber into 100mL of hydrogen peroxide with a mass percent solubility of 30%, then react in an oil bath at 70°C for 2 hours, wash the resulting product with deionized water 4 times, and dry it under vacuum at 110°C Dry in the box for 24 hours to obtain oxidized carbon fiber;
[0028] Step 2: Put 4g of oxidized carbon fiber into a round bottom flask, add 100mL of a mixed solution of ethanol and mercaptopropyltrimethoxysilane with a volume ratio of 95:5, adjust the pH of the solution to 5 with acetic acid, and then React under oil bath conditions for 7 hours. After the reaction, the product is washed 4 times with a mixed solution of ethanol and deionized water, and dried in a vacuum oven at 100°C for 24 hours to obtain mercapto-functionalized carbon fibers;
[0029] Step 3: A...
PUM
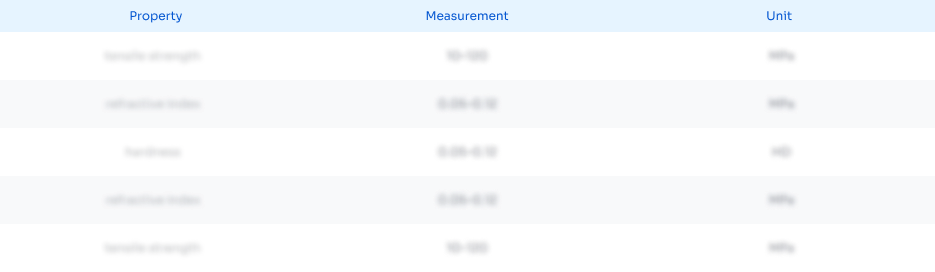
Abstract
Description
Claims
Application Information

- R&D Engineer
- R&D Manager
- IP Professional
- Industry Leading Data Capabilities
- Powerful AI technology
- Patent DNA Extraction
Browse by: Latest US Patents, China's latest patents, Technical Efficacy Thesaurus, Application Domain, Technology Topic, Popular Technical Reports.
© 2024 PatSnap. All rights reserved.Legal|Privacy policy|Modern Slavery Act Transparency Statement|Sitemap|About US| Contact US: help@patsnap.com